.60 Nitro to Electric
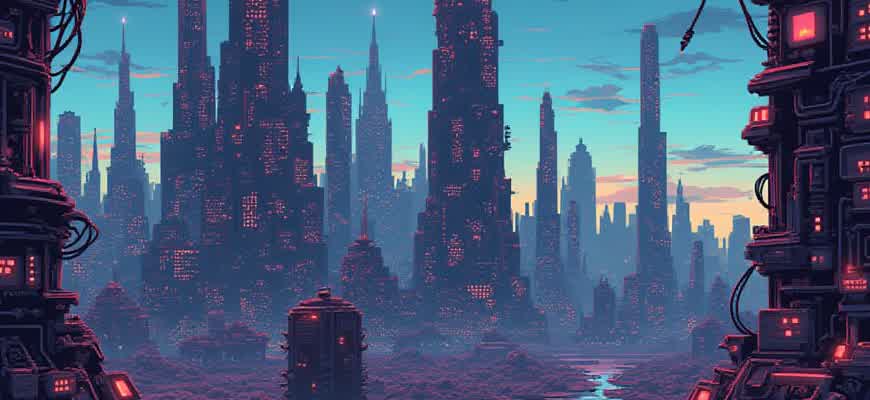
The shift from traditional .60 Nitro-powered engines to electric systems has gained significant momentum in the RC hobby community. This change is driven by several factors that affect performance, maintenance, and overall user experience. Electric motors offer advantages such as quieter operation, simpler setup, and less ongoing maintenance compared to nitro engines. Understanding the key differences between these two power sources is essential for enthusiasts considering the switch.
Key Differences:
- Noise and Vibration: Nitro engines produce significant noise and vibration, which can affect both the user and surrounding environments. In contrast, electric motors operate quietly, providing a smoother flying experience.
- Maintenance: Nitro engines require regular maintenance such as cleaning, tuning, and refueling. Electric systems, on the other hand, demand minimal upkeep, mainly battery management.
- Cost: Initial costs for nitro engines can be higher due to the need for fuel and spare parts. Electric motors, though, may have higher upfront costs for batteries and chargers but save money in the long run with fewer consumables.
Performance Considerations:
- Power Delivery: Electric motors provide instant power with no need for warm-up time, offering consistent and smooth throttle response throughout the flight.
- Flight Time: While nitro engines generally provide longer run times due to fuel capacity, electric systems are often limited by battery life, which can vary depending on battery type and weight.
"The real benefit of switching to electric is the ease of use and low maintenance, but it's important to understand the performance trade-offs before making the leap."
Comparison Table:
Feature | Nitro Engine | Electric Motor |
---|---|---|
Noise Level | High | Low |
Maintenance | High (fuel, tuning, cleaning) | Low (battery management) |
Power Response | Variable (requires warm-up) | Instantaneous |
Flight Time | Longer | Shorter |
Understanding the Differences Between .60 Nitro and Electric Engines
When comparing .60 Nitro engines to electric motors in RC vehicles, it's crucial to understand the fundamental differences that affect performance, maintenance, and overall user experience. Each type of engine has its own set of characteristics that make it suitable for different types of enthusiasts and uses. The .60 Nitro engine is a combustion-based motor that requires fuel and produces exhaust gases, whereas electric motors are powered by batteries and generate less noise and heat.
Although both types of engines can provide high performance, their operational requirements differ significantly. Below is a comparison of key aspects to consider when choosing between a .60 Nitro and an electric motor for your RC vehicle.
Key Differences
- Fuel Type: Nitro engines rely on a specialized fuel mixture of nitromethane, methanol, and oil, while electric motors use rechargeable batteries, usually LiPo (Lithium Polymer).
- Noise and Emissions: Nitro engines produce noticeable noise and exhaust gases, which can affect the environment and the user experience. Electric motors, in contrast, operate quietly and emit no pollutants.
- Maintenance: Nitro engines require regular maintenance such as cleaning, tuning, and replacing parts like glow plugs. Electric motors are generally more maintenance-free but still require attention to the battery and wiring.
Performance Factors
- Speed and Power: Nitro engines are known for their raw power and speed, especially in larger models. Electric motors, however, can deliver instantaneous torque, offering impressive acceleration.
- Run Time: A .60 Nitro engine's run time depends on the fuel tank size and the rate of consumption, typically providing about 15-20 minutes per tank. Electric vehicles, on the other hand, run based on battery life, with run times varying between 15 to 30 minutes depending on the battery capacity.
- Cost of Operation: Nitro engines can be expensive to operate due to the cost of fuel, maintenance, and parts replacement. Electric motors typically incur lower operating costs, especially with the growing longevity of modern batteries.
Maintenance and Setup
Aspect | Nitro Engine | Electric Engine |
---|---|---|
Maintenance | High, requires tuning, cleaning, and part replacements | Low, mainly focused on battery care and motor check-ups |
Setup Time | Longer, due to fuel mixing and tuning | Shorter, mainly charging and connecting components |
Important: Nitro engines are more suited for enthusiasts who enjoy the hands-on experience of tuning and maintaining a combustion engine, while electric motors are ideal for users seeking convenience, quieter operation, and lower maintenance.
Choosing the Right Electric Motor for Your .60 Nitro Conversion
When converting a .60 Nitro engine model to electric power, selecting the appropriate motor is crucial for achieving the best performance. The key factors to consider are the motor's power output, efficiency, and compatibility with your aircraft's design. A well-chosen electric motor will provide a smooth transition from fuel to electric, delivering similar or even superior performance compared to the original nitro engine.
Electric motors for conversions come in a variety of types and sizes, each designed to meet different needs. It's important to understand the specifications of your aircraft and balance motor size, weight, and power requirements to ensure optimal flight characteristics. In this guide, we will explore the factors that should influence your decision-making process when choosing an electric motor for a .60 Nitro conversion.
Motor Types and Specifications
Before making a choice, you'll want to be familiar with the types of motors available and the specific parameters to look for:
- Brushless Motors: These are the most commonly used motors in electric conversions due to their efficiency and reliability. They come in various sizes, typically identified by their stator size (e.g., 36xx, 40xx series).
- KV Rating: The KV rating indicates the motor's RPM per volt. A higher KV rating means more speed but potentially less torque, while a lower KV rating provides greater torque but at lower speeds.
- Motor Power: The motor's power output must be matched to the thrust required by your aircraft. Typically, you will need a motor that provides between 800 to 1200 watts for a .60 Nitro-sized model.
Matching the Motor to Your Aircraft's Specifications
To select the right motor, consider the following parameters:
- Weight: The motor’s weight must not exceed the payload capacity of the aircraft. A heavier motor will affect the aircraft's balance and flight performance.
- Propeller Size: The motor must be able to spin a propeller of appropriate size without overstressing the system. A larger propeller demands more power, so be sure to choose a motor that can handle the load.
- Battery Compatibility: Ensure the motor is compatible with the voltage and current rating of your chosen battery pack. The battery and motor must work together to provide reliable power for long-duration flights.
Recommended Motors for .60 Nitro Conversions
Motor Model | KV Rating | Power Output | Suggested Battery |
---|---|---|---|
XYZ 4035 | 500 | 1000W | 6S LiPo |
ABC 4120 | 700 | 1200W | 6S LiPo |
DEF 4050 | 600 | 950W | 5S LiPo |
Keep in mind that choosing a motor with too high of a KV rating might result in excessive speed, which can cause unnecessary wear and tear on other components, such as the ESC and propeller.
Essential Tools and Components for a Successful Conversion
Converting a .60 Nitro engine to an electric powertrain requires precision, technical knowledge, and a few key components. Without the right tools and parts, the conversion process can be challenging and time-consuming. Understanding which tools are necessary will help ensure a smooth transition from fuel to electric power.
Proper planning and selecting the right components are critical to maintaining performance and ensuring the longevity of the electric system. Below is a detailed breakdown of the essential tools and components required for the conversion process.
Key Tools for Conversion
- Basic Hand Tools – Screwdrivers, pliers, and wrenches are necessary for disassembling the Nitro engine and installing electric components.
- Soldering Kit – For connecting wires to the electric motor, ESC, and battery pack. A high-quality soldering iron will ensure solid connections.
- Heat Shrink Tubing – Used to cover solder joints and ensure insulation and protection against heat and moisture.
- Calipers and Measuring Tools – To measure the available space for the motor, ESC, and battery to ensure a correct fit.
- Drill – Needed for modifying the airframe or motor mount to accommodate new components.
Essential Components for Electric Conversion
- Electric Motor – A motor that fits the aircraft's power requirements and weight capacity is essential. A common choice is the brushless outrunner motor.
- ESC (Electronic Speed Controller) – The ESC regulates power between the battery and motor, ensuring smooth acceleration and braking.
- Battery Pack – A high-capacity LiPo or Li-ion battery is essential for providing the necessary power and flight duration. Ensure the voltage and capacity are appropriate for the selected motor and ESC.
- Propeller – Choose a propeller that matches the motor's power and ensures optimal efficiency. A larger diameter or different pitch may be necessary depending on the motor's specs.
- Battery Charger – A compatible charger designed for LiPo or Li-ion batteries will ensure safe and efficient charging.
Important Considerations
The weight distribution and balance of the aircraft will change after replacing the engine and fuel system with electric components. Make sure to check and adjust the CG (center of gravity) for optimal flight performance.
Component | Purpose |
---|---|
Brushless Motor | Provides efficient power for the aircraft's propulsion system |
ESC | Controls motor speed and manages power flow |
Battery Pack | Supplies power to the motor for flight |
Propeller | Converts motor power into thrust |
Charger | Ensures safe and efficient charging of the battery |
Choosing the Right Battery for Your Electric Setup
When converting your .60 Nitro engine to an electric setup, selecting the right battery is crucial for optimal performance and longevity. The battery type you choose will significantly influence the power, weight, and efficiency of your model. A proper battery ensures reliable power delivery, optimal flight time, and safe operation. Let's explore key factors to consider when making your decision.
There are various factors to take into account, including battery chemistry, voltage, capacity, and weight. These elements directly affect the overall performance of your electric model. To make an informed decision, it’s important to understand how each factor contributes to your setup.
Key Factors to Consider
- Battery Chemistry: The most common types of battery chemistry are LiPo (Lithium Polymer) and NiMH (Nickel-Metal Hydride). LiPo batteries offer higher energy density and are generally lighter, providing better performance. NiMH batteries, however, are safer and more durable but often bulkier and heavier.
- Voltage: The voltage of your battery must match the power requirements of your electric motor. Typically, 6S or 8S LiPo batteries are used for setups that replace a .60 Nitro engine. Ensure that the voltage rating suits your motor’s specifications to avoid underpowering or damaging components.
- Capacity (mAh): The capacity, measured in milliamp-hours (mAh), defines the battery's energy storage. Higher capacity allows for longer flight times, but it also adds weight. It's essential to balance power and weight for optimal flight performance.
- Weight: Weight is an important consideration in any RC model. A battery that’s too heavy can affect the balance and handling of the plane. Always aim for a battery that provides sufficient power without overburdening your setup.
Battery Selection Process
- Determine Your Power Requirements: Check the specifications of your motor and ESC (Electronic Speed Controller) to identify the required voltage and current draw.
- Select Appropriate Chemistry: Decide between LiPo and NiMH based on your need for power, weight, and safety. LiPo is preferred for most electric conversions due to its lighter weight and higher efficiency.
- Calculate Capacity: Choose a battery with the right mAh rating. A higher capacity will provide longer flight times, but balance this with the weight limitations of your model.
- Ensure Proper Fit: Verify that the battery physically fits within the designated battery compartment of your plane.
Important: Always check the manufacturer’s guidelines for both the motor and battery. Using an incorrect battery type or size can lead to overheating, loss of performance, or even failure of the setup.
Example Battery Options
Battery Type | Voltage | Capacity (mAh) | Weight (g) |
---|---|---|---|
LiPo | 22.2V (6S) | 5000 mAh | 650 g |
LiPo | 25.2V (7S) | 4000 mAh | 750 g |
NiMH | 12V | 3000 mAh | 800 g |
Guide to Converting Your Nitro Engine to Electric Power
If you're looking to switch your RC vehicle from nitro to electric power, it's important to follow a systematic approach. This transition can significantly improve the performance and convenience of your model. The process requires careful planning and the right components to ensure a smooth switch. Below is a step-by-step guide to help you replace your nitro engine with an electric motor.
Before beginning the conversion, ensure that your RC car is compatible with electric systems. You will need a suitable motor, electronic speed controller (ESC), battery, and additional accessories like a mount for the motor and gear mesh adjustments. This guide covers the essential steps involved in the conversion process.
Step-by-Step Conversion Process
- Remove the Nitro Engine: Start by detaching the nitro engine from your RC car. This involves unscrewing the engine mounts, disconnecting the fuel lines, and removing the exhaust system.
- Clean the Chassis: After removing the engine, clean the chassis thoroughly to prepare it for the electric components. Any debris or leftover fuel residue should be cleared.
- Install the Electric Motor: Choose an appropriate electric motor for your vehicle. Install the motor by securing it into place with the mounting kit. Make sure to align the motor with the gear mesh for optimal performance.
- Connect the ESC and Battery: Attach the ESC to the motor and ensure proper wiring. Select a compatible battery, typically LiPo, and place it securely in the battery compartment. Connect the ESC to the battery and motor, following the manufacturer's guidelines.
- Adjust the Gear Ratio: Modify the gear ratio as needed to accommodate the electric motor's characteristics. This might involve changing the pinion or spur gear to match the motor’s power delivery.
- Test the Setup: After assembly, conduct a test run to check for any issues with power delivery, heat buildup, or component alignment.
Important Considerations
Make sure your ESC is compatible with the motor and battery you’re using. It's crucial to check the voltage rating to avoid damaging your electronics.
Recommended Components
Component | Recommendation |
---|---|
Motor | Brushless motor (typically 3650-4000KV for 1/10 scale vehicles) |
ESC | Compatible with your motor's voltage (e.g., 2S or 3S LiPo) |
Battery | LiPo, 2S or 3S depending on your motor's requirements |
Motor Mount | Custom mount for electric motor (if needed) |
Adjusting the Airframe and Mounting Points for Electric Conversion
When converting a .60 nitro-powered aircraft to electric, modifying the airframe and mounting points is essential for a successful transition. Electric power systems require different structural considerations than their nitro counterparts. The weight distribution, size of the motor, and placement of the battery all impact the overall integrity and performance of the airframe.
Proper adjustments to the fuselage and mounting points ensure a secure installation of the electric motor and other components. This step is critical, as misalignment or improper mounting can lead to imbalances, poor performance, and safety concerns during flight. Below are key steps to consider when adapting the airframe.
Airframe Modifications
- Motor Mounting Location: Determine the appropriate location for the motor by considering the original engine's placement. The electric motor may need to be mounted further forward or backward to maintain proper center of gravity (CG).
- Battery Compartment: Create space for the battery, ensuring it is securely mounted to prevent any movement during flight. The compartment should allow for easy access and provide ventilation for cooling.
- Structural Reinforcement: Reinforce the fuselage around the motor mount area to support the additional weight of the electric motor. Carbon fiber or plywood reinforcements are common choices for added strength.
Mounting Points Adjustments
- Check if the original mounting holes align with the new motor and battery positions. You may need to drill new holes or install mounting plates to ensure the components are securely fastened.
- Use vibration-damping mounts to reduce stress on the airframe caused by the electric motor's operation, especially if using high-power motors that generate more vibrations than nitro engines.
- Ensure the ESC (electronic speed controller) is mounted in a location with good airflow for cooling, away from heat-sensitive components like the battery and receiver.
Important Notes
When adjusting mounting points, always consider the weight distribution to maintain proper CG. Incorrect placement of components can lead to poor flight performance or instability.
Suggested Changes in Mounting System
Original Mount | Electric Conversion Mount |
---|---|
Standard nitro engine mount | Custom electric motor mount |
Fuel tank area | Battery compartment |
Exhaust system mount | ESC mounting point |
Testing Your Electric Model for Optimal Performance
When transitioning from a .60 Nitro model to an electric one, it's essential to ensure your electric setup operates at peak performance. This involves thorough testing of various components, including the battery, motor, and electronics. Proper testing helps identify potential issues before you go to the field, maximizing the model's efficiency and lifespan.
To start, carefully assess each part of your electric model to make sure everything is functioning as intended. Run multiple tests to fine-tune settings, such as the throttle response, motor temperature, and overall handling. By understanding these parameters, you can make informed decisions for performance adjustments.
Key Areas to Focus During Testing
- Battery Performance: Ensure the battery holds a full charge and delivers adequate power throughout the flight. Test it under various load conditions to gauge its discharge rate.
- Motor Efficiency: Check the motor for overheating. A well-functioning motor should remain cool even under heavy load.
- ESC (Electronic Speed Controller): Test the ESC response to different throttle levels to ensure smooth acceleration and deceleration.
Test Procedures
- Initial Bench Test: Perform an initial test on the ground to evaluate all systems. Observe motor function and response to throttle input.
- Flight Test: Take the model for a short flight to monitor how it performs in real conditions. Focus on battery life, motor temperature, and ESC functionality.
- Post-Flight Analysis: After flying, inspect the motor and ESC for any signs of wear. Check the battery voltage and compare it to the expected performance curve.
Important: Always make sure to perform a proper cooling down procedure after each flight to maintain battery health and motor longevity.
Optimal Performance Settings
Component | Optimal Setting |
---|---|
Battery | Discharge rate < 30%, charge fully after each flight |
Motor | Keep under 160°F (70°C) during flight |
ESC | Ensure smooth throttle progression, no lag or stuttering |