Nitro Dipping System
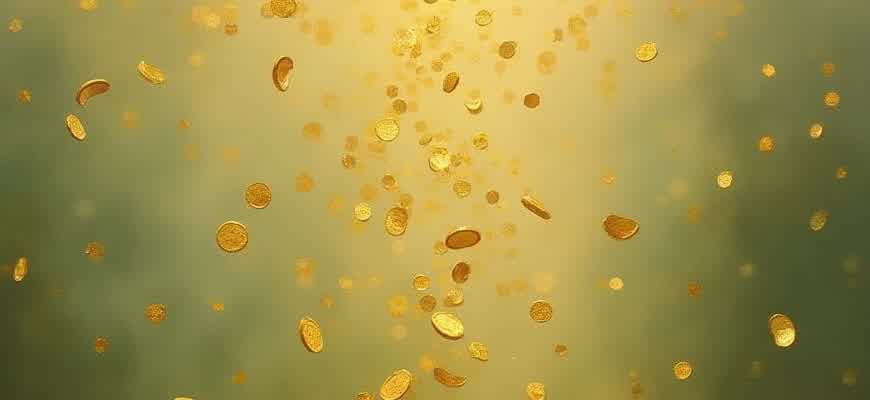
The Nitro Dipping System is a highly effective method used in industrial applications for enhancing the surface properties of materials, especially metals. It involves the process of dipping a substrate into a nitrogen-rich solution to improve durability, corrosion resistance, and fatigue strength. This technique is particularly useful for components exposed to extreme environmental conditions or heavy mechanical stress.
Key Benefits of Nitro Dipping:
- Increased wear resistance
- Improved surface hardness
- Enhanced corrosion protection
- Extended lifespan of components
The system typically works by immersing the material in a bath containing a controlled concentration of nitrogen compounds. The procedure modifies the microstructure of the material's surface, forming a hardened layer that provides superior mechanical properties.
It is essential to maintain precise temperature and time control during the dipping process to achieve optimal results. Improper conditions can lead to defects such as surface cracking or insufficient hardness.
Common Applications:
- Aerospace components
- Automotive parts
- Heavy machinery
- Tooling and dies
Process Comparison
Method | Advantages | Disadvantages |
---|---|---|
Nitro Dipping | Superior surface hardness, corrosion resistance | Requires precise process control |
Other Surface Treatments | Cheaper, easier implementation | Lower durability and wear resistance |
Choosing the Right Materials for Nitro Dipping Process
The nitro dipping technique involves submerging an object into a liquid, usually a special hydrographic film, that is then transferred onto the surface of the object. To ensure a successful application, it is crucial to choose the right materials for the dipping process. The material of the object, the type of film, and the compatibility of chemicals play a significant role in the final outcome of the dipped product.
Selecting appropriate materials will determine the durability, finish, and quality of the coating. Proper surface preparation, as well as knowing the material's reaction to the film and chemicals, are key factors to consider when performing nitro dipping.
Key Considerations When Selecting Materials
- Material Compatibility: Not all materials respond well to hydrographic films. Common materials like plastic, metal, and glass are ideal candidates. Materials that are porous or absorbent, such as wood, may require extra steps to prepare the surface.
- Surface Preparation: Before dipping, ensure that the surface is clean, smooth, and free of any contaminants. Improper preparation can lead to peeling or uneven application.
- Film Compatibility: Choose films that are designed for the type of material being dipped. Some films are specifically engineered for plastic, while others work better on metals or ceramics.
Choosing Between Different Types of Films
- Polyester Films: Ideal for plastics and metals, they offer a smooth finish and vibrant colors.
- Polyurethane Films: Provide greater durability and resistance to wear and tear, making them suitable for high-stress items.
- Hydrophobic Films: These films are water-resistant, making them a good choice for objects that will be exposed to moisture.
Material Compatibility Table
Material Type | Suitable Film Types | Preparation Steps |
---|---|---|
Plastic | Polyester, Polyurethane | Clean, sand lightly, apply primer if necessary |
Metal | Polyester, Polyurethane | Clean thoroughly, remove rust, apply primer |
Glass | Polyester | Clean well, avoid sanding |
When choosing the right materials for nitro dipping, remember that the success of the process depends on both the material properties and the type of hydrographic film you use. Always test your combination to ensure optimal results.
How Nitro Dipping Improves Product Longevity
Nitro dipping is an advanced finishing technique that significantly enhances the resilience of various products. By immersing items in a special solution containing nitrogen, manufacturers are able to create a durable and resistant surface that can withstand harsh environmental conditions. This process provides a layer of protection that not only boosts physical endurance but also extends the overall lifespan of the product.
One of the key benefits of nitro dipping is its ability to provide consistent protection across diverse materials. Whether it's plastic, metal, or composite, the solution penetrates the surface and bonds deeply, preventing wear, corrosion, and degradation. This ensures that products maintain their functionality and aesthetic qualities for much longer compared to untreated alternatives.
Benefits of Nitro Dipping for Durability
- Corrosion Resistance: Nitro dipping forms a protective layer that prevents rust and corrosion, even in challenging outdoor environments.
- Wear Resistance: The treated surface becomes more resistant to scratches and abrasions, improving the product's ability to maintain its appearance and integrity over time.
- Temperature Tolerance: Products that undergo nitro dipping are less affected by extreme heat or cold, making them suitable for a wider range of applications.
- Waterproofing: The treatment enhances the water resistance of the product, protecting it from moisture-related damage.
Application Process
- The item is cleaned and prepared for dipping to remove any contaminants.
- The product is then immersed in a nitrogen-based solution, which is carefully controlled to ensure proper coating.
- After immersion, the item is allowed to cure, ensuring the coating bonds fully to the surface.
Performance Comparison
Feature | Untreated Product | Nitro Dipped Product |
---|---|---|
Corrosion Resistance | Low | High |
Scratch Resistance | Moderate | High |
Water Resistance | Low | High |
Temperature Resistance | Moderate | High |
"Nitro dipping enhances the durability of products, ensuring they perform reliably in demanding environments while maintaining their aesthetic appeal."
Comparing Nitro Dipping with Traditional Coating Methods
In industrial applications, coating methods play a crucial role in ensuring the durability and performance of materials. Among the various methods, Nitro Dipping has gained attention for its unique advantages over traditional techniques. This process, which involves dipping components into a bath of nitrogen-based solution, differs significantly from conventional coating methods, such as powder coating or liquid spraying. Understanding the key differences between Nitro Dipping and traditional coating methods can help determine the most suitable option for specific applications.
Traditional coating methods have been widely used for years, each offering its own set of benefits and limitations. However, Nitro Dipping stands out in terms of its efficiency, adhesion strength, and environmental impact. The following sections provide a detailed comparison of these two methods, highlighting their respective strengths and weaknesses.
Key Differences in Coating Processes
- Process Complexity: Nitro Dipping typically involves fewer steps compared to traditional methods. It requires dipping parts into a nitrogen solution, whereas traditional methods may require multiple preparation stages, including priming, curing, and coating.
- Durability and Adhesion: Nitro Dipping tends to offer superior adhesion strength and resistance to wear. In contrast, traditional coatings may require additional layers to achieve the same level of durability.
- Environmental Impact: Nitro Dipping produces less environmental waste, as it avoids the use of harmful chemicals found in some traditional coating methods like spray painting or powder coating.
Advantages and Disadvantages
- Advantages of Nitro Dipping:
- Higher adhesion strength
- Less environmental impact
- Fewer processing steps
- Disadvantages of Nitro Dipping:
- Limited availability of nitrogen-based solutions for some industries
- Potentially higher initial equipment costs
- Advantages of Traditional Coating:
- Widely available materials and processes
- Can be applied to a broad range of surfaces
- Disadvantages of Traditional Coating:
- Requires multiple steps, increasing overall process time
- Higher environmental impact due to chemicals used
Comparing Cost and Efficiency
Aspect | Nitro Dipping | Traditional Coating |
---|---|---|
Process Time | Shorter | Longer (due to multiple steps) |
Cost | Higher initial setup costs | Generally lower initial cost |
Environmental Impact | Lower | Higher (chemical waste) |
Durability | Superior | Depends on layers and materials |
Important: Nitro Dipping is often preferred for high-performance applications requiring exceptional durability, while traditional methods might still be chosen for general-purpose coatings where cost is a major consideration.
Integrating Nitro Dipping into Your Production Line
Introducing a Nitro Dipping System into an existing production line requires careful planning and precise execution to optimize efficiency and maintain product quality. The system must align with current processes, machinery, and output goals. The integration process often involves upgrading certain equipment and training staff on the new techniques to ensure smooth operation and minimal disruption.
The first step in incorporating Nitro Dipping is assessing your current production capabilities. You’ll need to identify where the system can be incorporated without compromising throughput or quality. A structured approach ensures that changes are incremental and the transition is as smooth as possible. Consider the following guidelines for integration:
Key Steps for Integration
- Evaluate Current Production Setup: Analyze where Nitro Dipping can be added, ensuring compatibility with existing equipment.
- Install Necessary Equipment: Depending on the type of system chosen, additional hardware or modifications may be needed.
- Staff Training: Ensure operators are well-versed in Nitro Dipping techniques to maintain quality standards.
- System Calibration: Calibrate the system to match your production speed and ensure consistency.
Ensure that Nitro Dipping processes align with safety standards and are compatible with the materials being processed. Proper testing should be done to confirm consistency before full-scale integration.
Implementation Process Overview
- Preparation Phase: Review current workflow and determine the best point of integration for the Nitro Dipping system.
- Installation: Set up the system and make necessary adjustments to machinery.
- Testing and Adjustment: Run test batches to evaluate performance and refine settings.
- Final Integration: Gradually increase output and fully integrate the Nitro Dipping process into regular production.
Equipment Requirements
Equipment | Description | Considerations |
---|---|---|
Nitro Dipping Tank | Primary tank for applying Nitro treatment to materials. | Size and capacity based on production volume. |
Drying System | Drying system to remove excess nitro and cure the treatment. | Ensure drying time aligns with production speeds. |
Control Panel | System controls for adjusting temperature and pressure during the process. | Intuitive interface for ease of use by operators. |
Cost Analysis: Is Investing in Nitro Dipping the Right Choice for Your Business?
The introduction of nitro dipping systems in production lines has been a game-changer for many businesses. It allows for high-quality finishes on a variety of materials with minimal effort. However, before making the decision to implement this technology, it’s crucial to evaluate whether the investment will provide a significant return. Below, we break down the essential factors influencing the cost-effectiveness of nitro dipping systems for your operations.
While the system promises improved efficiency, aesthetics, and durability, the initial investment, ongoing operational costs, and potential savings must be weighed carefully. Let’s explore the costs involved, along with potential benefits, to determine whether nitro dipping is a worthwhile investment for your business.
Key Costs Involved in Nitro Dipping Systems
- Initial Setup Costs: This includes the cost of the dipping machine, installation, and training for employees.
- Material Costs: Nitro dipping requires specialized chemicals and materials, which can increase production expenses.
- Maintenance and Operational Costs: Regular maintenance is required to ensure optimal performance, and the system's operation can be energy-intensive.
- Labor Costs: While the process automates many steps, skilled labor is still needed to manage and monitor the system.
Benefits that Offset the Costs
Nitro dipping systems provide a significant edge by reducing the time spent on manual finishing processes, improving the quality of the finished products, and lowering long-term labor costs.
- Increased Production Speed: Nitro dipping significantly reduces production time by automating surface treatment, which increases throughput.
- Improved Durability: Products finished with this method often exhibit better resistance to wear and corrosion, reducing returns and warranty claims.
- Consistent Quality: The uniform coating ensures that every product meets the desired quality standards, which can enhance your brand's reputation.
Cost-Benefit Breakdown
Expense Type | Estimated Cost | Benefit |
---|---|---|
Initial Setup | $50,000 - $150,000 | High upfront cost but offers long-term value through automation. |
Material Costs | $1,000 - $5,000 per month | Ongoing cost for chemicals but reduces need for additional finishing steps. |
Maintenance | $10,000 annually | Minimal downtime and fewer defects, ensuring a smooth workflow. |
While the initial investment can be significant, the long-term savings in labor, improved production speed, and higher product quality make nitro dipping a potentially profitable choice for businesses looking to scale efficiently. Consider these factors carefully to decide whether this technology aligns with your business needs and budget.