Nitro Engine to Electric Conversion Chart
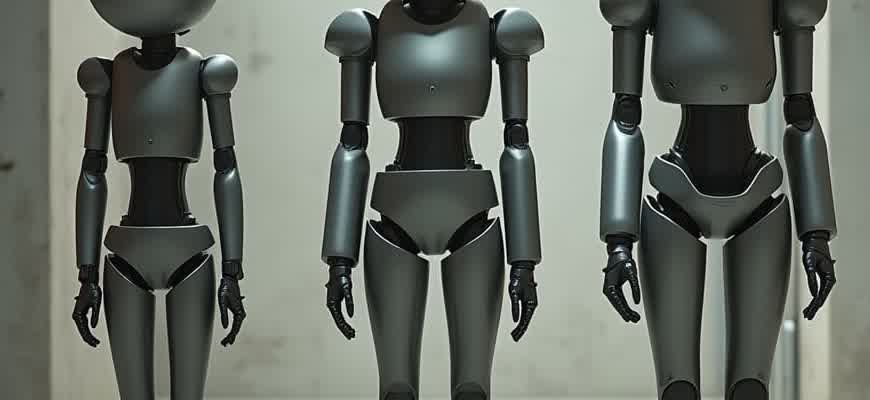
Converting a model car from a nitro engine to an electric motor setup is a popular modification for hobbyists seeking more efficiency and lower maintenance. This transition requires understanding the key differences between both power sources and their components. Below is an overview of what is typically involved in the conversion process.
Key Components Comparison
Component | Nitro Engine | Electric Motor |
---|---|---|
Power Source | Fuel (Nitromethane or Methanol) | Battery (LiPo, NiMH) |
Maintenance | High (Frequent tune-ups) | Low (Mainly battery care) |
Weight | Heavier | Lighter |
Runtime | Varies (Fuel dependent) | Varies (Battery dependent) |
Important Considerations
When converting to an electric system, it is crucial to ensure that the motor's size and power output match the vehicle's requirements. Some adjustments in the chassis or drivetrain may be necessary to accommodate the electric components.
Below is a checklist to guide you through the conversion:
- Choose a suitable electric motor and ESC (Electronic Speed Controller) based on the vehicle's size and weight.
- Replace the fuel tank with a battery holder or compartment.
- Modify the drivetrain if necessary to match the electric motor's characteristics.
- Ensure proper cooling for the motor and ESC, as electric systems can generate significant heat.
Choosing the Right Electric Motor for Your Nitro Engine
When converting a nitro engine to an electric powertrain, selecting the correct electric motor is essential for achieving optimal performance. The motor must match the power characteristics of the nitro engine to ensure a similar driving experience. One of the key factors in this decision is understanding the power-to-weight ratio, as it directly influences the handling and speed of the vehicle.
Electric motors come in various sizes and specifications, so it's important to carefully assess your vehicle's requirements. Consider the vehicle's weight, the type of driving you plan to do, and the desired top speed. By understanding these factors, you can make a more informed decision that will lead to better performance and efficiency.
Key Factors to Consider
- Power Output: Match the motor's power (measured in watts) to the nitro engine's output in horsepower.
- Voltage: Choose the correct voltage for your motor, ensuring it aligns with your battery's rating.
- Motor Type: Brushless motors are typically preferred for their efficiency and longevity compared to brushed motors.
- Motor Size: Ensure the motor size fits within your vehicle's chassis without causing clearance issues.
Common Motor Options
- Low RPM, High Torque: Ideal for vehicles that require heavy lifting or off-road capability.
- High RPM, Low Torque: Best suited for high-speed racing vehicles on smooth tracks.
- Medium RPM, Balanced Torque: A versatile choice for all-around performance in various conditions.
Tip: Always check the motor's KV rating (RPM per volt). A lower KV rating typically indicates more torque, while a higher KV rating is better for speed.
Comparing Motor Specifications
Motor Type | Power Output (Watts) | Voltage | Torque |
---|---|---|---|
Brushless | 1000-3000 | 6-12V | High |
Brushed | 500-2000 | 6-12V | Medium |
Step-by-Step Guide to Dismantling Your Nitro Engine
Disassembling your nitro engine is a crucial first step in converting it to an electric power system. The process requires patience and precision, as many parts need to be carefully removed without causing damage. Make sure you have the right tools and a clean, organized workspace to begin the procedure. Proper handling of engine components ensures a smooth conversion and avoids unnecessary complications later.
Before starting, ensure the engine is completely cool and disconnected from any power source. Gather the required tools such as screwdrivers, pliers, and wrenches. Following these steps carefully will guide you through the disassembly process, allowing you to safely remove and prepare your nitro engine for the conversion.
1. Prepare the Engine for Dismantling
- Remove any attached fuel lines and disconnect the throttle linkage from the carburetor.
- Unscrew the exhaust system, making sure no parts are left connected to the engine.
- Disconnect the engine from the chassis, removing any mounting screws or brackets holding it in place.
2. Remove External Components
- Carefully detach the carburetor, making sure to keep track of screws and gaskets.
- Unbolt the flywheel and any remaining external parts like the pull start mechanism.
- Take out the cooling head, paying attention to any washers or seals that may be present.
3. Disassemble the Engine Internals
- Take off the cylinder head and remove the piston from the engine block.
- Inspect the crankshaft for any signs of wear or damage before detaching it.
- Remove the bearings and seals, keeping them aside if they are still in good condition for reuse.
Important: Always keep track of small parts like screws, washers, and seals. It's essential to organize them properly to avoid confusion when reassembling or storing the engine for future use.
4. Final Checks
Component | Check |
---|---|
Crankcase | Look for cracks or wear that might affect performance after reassembly. |
Piston | Check for any signs of scoring or damage that could impact the engine's efficiency. |
Flywheel | Inspect for any cracks or broken teeth that could cause malfunctions during operation. |
Tip: Always use a clean cloth to wipe off any excess oil or fuel residue during disassembly to avoid contaminating the new electric components.
How to Calculate Battery Capacity for Electric Conversion
When converting a nitro-powered vehicle to an electric one, determining the appropriate battery size is essential for ensuring optimal performance and range. The main factors that influence battery capacity include vehicle weight, motor power, desired range, and efficiency. By carefully calculating these parameters, you can select the right battery size for your conversion project.
The key formula to calculate the required battery capacity is based on the vehicle's energy consumption per distance unit, and the desired range. Once you have this information, you can estimate the battery's total energy requirement in watt-hours (Wh) and choose a suitable battery pack.
Step-by-Step Battery Capacity Calculation
- Step 1: Determine the average power consumption of your electric motor, typically measured in watts (W).
- Step 2: Estimate the desired range of your vehicle, usually in miles or kilometers.
- Step 3: Calculate the energy consumption per unit of distance. This can be done by dividing the power consumption by the vehicle's efficiency.
- Step 4: Multiply the energy consumption by the desired range to get the total required energy in watt-hours (Wh).
- Step 5: Add a safety margin (10-20%) to account for unforeseen conditions, such as rough terrain or high speeds.
Example Calculation
Parameter | Value |
---|---|
Motor Power | 1500 W |
Efficiency | 0.8 |
Desired Range | 30 miles |
Energy Consumption (Wh per mile) | 1500 / 0.8 = 1875 W (per hour) |
Total Energy Requirement | 1875 W * 30 miles = 56,250 Wh |
Required Battery Capacity (including margin) | 56,250 Wh * 1.2 = 67,500 Wh |
Important: Always choose a battery with a voltage and capacity that matches the motor’s requirements. Ensure the battery can handle the peak power demand of the motor without overheating or underperforming.
Converting Fuel Tank Space to Battery Compartment in Nitro Engines
When transitioning from a nitro engine to an electric setup, one of the primary challenges is repurposing the available space, particularly the fuel tank compartment, to accommodate the new battery pack. The size and shape of the fuel tank are designed to house liquid fuel, so it's crucial to evaluate how the available space can be adapted for batteries while maintaining proper weight distribution and structural integrity. Proper planning ensures that the conversion does not affect the performance or durability of the vehicle.
To successfully convert the fuel tank space into a battery compartment, it's important to account for several factors such as the size of the battery, wiring configurations, cooling needs, and the method of securing the battery in place. This modification often requires custom fittings and brackets, as well as ensuring that there is sufficient ventilation for the battery to avoid overheating.
Steps for Conversion
- Measure the fuel tank area to ensure the battery can fit securely.
- Remove any fuel lines and tank components to clear space.
- Install custom brackets or compartments to hold the battery in place.
- Ensure proper wiring paths for the battery, avoiding interference with other components.
- Verify adequate airflow around the battery for cooling purposes.
Considerations for Battery Placement
- Battery Size: Ensure that the battery fits snugly in the fuel tank compartment, with extra room for any required wiring and connectors.
- Weight Distribution: The battery placement can affect the vehicle’s center of gravity. Position the battery for balanced handling and performance.
- Safety: Ensure that the battery is properly insulated and secured to prevent damage during operation.
Note: Always test the setup in controlled conditions to confirm that the new battery compartment does not interfere with the vehicle's overall performance.
Comparison: Fuel Tank vs Battery Compartment
Feature | Fuel Tank | Battery Compartment |
---|---|---|
Size | Typically larger to hold liquid fuel | Customized to fit battery size |
Cooling | Minimal, as fuel does not require cooling | Active cooling or ventilation needed to prevent overheating |
Weight Distribution | Forward weight, typically close to the engine | Balance and positioning critical for handling |
Motor Mounting and Compatibility Challenges
When converting from a nitro engine to an electric motor, one of the first challenges is ensuring that the new electric motor fits into the existing motor mount. Nitro engines typically have specific mounting points that are different from those used in electric motors. This discrepancy can cause alignment issues, requiring either custom solutions or additional components to make the conversion work properly.
Another factor to consider is the compatibility between the motor and the powertrain components such as the drivetrain, gearbox, and chassis. Electric motors come in various sizes, mounting patterns, and shaft types, which must be compatible with the existing setup to ensure smooth operation and optimal performance.
Key Compatibility Issues
- Motor Size: The physical dimensions of the electric motor may differ from the original nitro engine, which can lead to issues fitting it into the available space.
- Mounting Plate: The bolt pattern and design of the motor mounting plate may not align with the electric motor, requiring an adapter plate or custom fabrication.
- Shaft Size and Type: Electric motors have different shaft designs, and ensuring the right type is crucial for smooth integration with the drivetrain components.
- Weight Distribution: The weight and balance of the vehicle may change, as electric motors often differ in mass compared to their nitro counterparts, affecting handling.
Mounting Solutions
- Use of Adapter Plates: Custom adapter plates can help align the motor with the existing mount points.
- Motor Mount Conversion Kits: Some manufacturers offer kits designed to make conversions easier, reducing the need for custom solutions.
- Custom Mounting Solutions: For unique applications, creating a custom motor mount might be the most effective option.
Important Considerations
Always double-check the mounting dimensions before beginning any conversion to avoid unnecessary modifications and potential damage to the motor or vehicle structure.
Sample Compatibility Chart
Component | Nitro Engine Specs | Electric Motor Specs |
---|---|---|
Mounting Hole Pattern | Standard Nitro | Custom Adapter Plate Required |
Shaft Size | 5mm | 6mm (common for electric) |
Weight | 500g | 600g |
How to Adjust Your Vehicle’s Gearbox for Electric Drive
When converting a vehicle from a nitro engine to an electric motor, one of the crucial tasks is adjusting the gearbox to work with the new electric drive system. Traditional internal combustion engines require different gear ratios to operate efficiently, but electric motors function with a different set of requirements. This can affect performance, efficiency, and overall driving experience.
To properly adjust the gearbox, you'll need to understand how the electric motor operates and how it interacts with the vehicle's transmission. Electric motors provide consistent torque across a wide range of RPMs, which means that traditional multi-gear transmissions may not be necessary. In some cases, the gearbox might need to be replaced or modified to better match the power characteristics of the electric motor.
Steps to Modify the Gearbox
- Assess the Motor Characteristics: Understand the power band and torque curve of the electric motor. This will help determine if the existing gearbox can be retained or if modifications are needed.
- Determine Gearbox Requirements: Some electric drive systems do not require a gearbox, while others may benefit from a single-speed transmission. Choose based on the torque and speed requirements.
- Remove the Nitro Engine Components: Disconnect and remove the nitro engine and transmission components that are not compatible with the electric motor setup.
- Modify or Replace the Gearbox: Modify the existing gearbox by adjusting gear ratios or completely replace it with a system designed for electric drive.
- Install the Electric Motor: Fit the motor to the transmission, ensuring that the coupling is secure and that the motor's output is effectively transferred to the wheels.
Important Considerations
Electric motors have a broader torque range than internal combustion engines. This means that gear ratios, if used, should be chosen to complement the motor’s torque characteristics, providing a balance between acceleration and top speed.
Some vehicles may benefit from a reduction gearbox to enhance efficiency, especially at higher speeds. It’s important to test the vehicle after the modification to ensure smooth shifting and proper motor performance.
Gearbox and Motor Compatibility
Transmission Type | Advantages | Considerations |
---|---|---|
Single-Speed | Simple, fewer parts to maintain, optimal for electric motors | May not be ideal for high-speed applications |
Multi-Gear | Better for performance vehicles with variable speed demands | More complex, may introduce efficiency losses |
Reduction Gearbox | Improves efficiency at high speeds | Potentially slower acceleration |
Cooling Solutions for Electric Motors in Converted Nitro Engines
When converting nitro engines to electric, proper cooling of the electric motor is crucial to maintain performance and longevity. Electric motors, especially those with higher power ratings, generate significant heat during operation. Without an effective cooling system, the motor can overheat, leading to reduced efficiency and potential damage. This is where specialized cooling solutions come into play.
There are several cooling methods available, each with its own set of benefits and challenges. The choice of cooling system largely depends on the motor's size, power output, and the intended application. Some systems focus on passive cooling, while others incorporate active methods to ensure optimal temperatures are maintained even under heavy load.
Types of Cooling Solutions
- Air Cooling: This is the most common and cost-effective method. It uses fans or the natural flow of air to dissipate heat from the motor's surface.
- Water Cooling: A more efficient solution, water cooling involves circulating coolant around the motor to absorb heat. This method is often used in high-performance conversions.
- Oil Cooling: Similar to water cooling but using oil as a medium. Oil can absorb more heat than air or water, making it ideal for high-torque applications.
- Hybrid Systems: Combining air, water, or oil cooling with additional heat sinks or radiators to enhance cooling performance.
Cooling System Considerations
- Size of the Motor: Larger motors require more advanced cooling techniques to handle the increased heat production.
- Power Output: Motors with higher power outputs generate more heat, necessitating a robust cooling system.
- Environmental Factors: Operating in hot climates or confined spaces may require more aggressive cooling solutions, such as water or oil cooling.
- Maintenance: Regular inspection and maintenance of the cooling system are essential to ensure optimal performance and prevent overheating.
Performance and Cooling Efficiency
Cooling Type | Efficiency | Best Use Case |
---|---|---|
Air Cooling | Low to Medium | Casual and light-duty applications |
Water Cooling | Medium to High | High-performance applications |
Oil Cooling | High | Heavy-duty or high-torque systems |
Hybrid Systems | Very High | Extreme performance and high heat dissipation needs |
Important: A well-chosen cooling system not only enhances motor longevity but also improves overall performance, especially in high-load scenarios. Choosing the right solution based on the application is key to a successful electric conversion.
Post-Conversion Testing and Troubleshooting for Electric Systems
After converting a vehicle from a Nitro engine to an electric motor, it is essential to conduct thorough testing to ensure that all components are functioning properly. This includes verifying the performance of the electric motor, battery system, and other vital components such as the controller and wiring. Proper testing helps identify potential issues early, minimizing the risk of failures during operation.
Once the conversion is completed, it's crucial to follow a structured approach to troubleshoot common problems that may arise. Issues such as insufficient power delivery, overheating, or incorrect motor behavior can often be traced to wiring faults, incorrect component settings, or faulty connections. A systematic troubleshooting process will help you identify and fix these problems efficiently.
Key Testing Areas
- Motor Performance: Check if the motor responds smoothly and without delays when throttle input is provided.
- Battery Voltage: Measure the voltage of the battery pack under load to ensure it's consistent with specifications.
- Controller Settings: Ensure the controller is programmed correctly to manage the motor’s speed and torque effectively.
- Connection Integrity: Inspect all wiring for secure connections, ensuring there are no loose or shorted wires.
Troubleshooting Steps
- Verify Power Supply: Ensure the battery is properly charged and capable of providing the necessary voltage.
- Check for Overheating: Inspect both the motor and controller for signs of overheating, as this can indicate a power or cooling issue.
- Test Motor Response: If the motor is sluggish or erratic, check the controller settings and verify motor connections.
- Inspect Wiring: Look for any damaged or improperly connected wires that could cause intermittent or complete failure.
Common Issues and Solutions
Problem | Possible Cause | Solution |
---|---|---|
Motor Not Running | Disconnected wiring or controller failure | Inspect all connections and test controller functionality |
Overheating | Insufficient cooling or excessive load | Check cooling system, reduce load, and ensure correct motor rating |
Battery Drainage | Faulty battery or incorrect power management settings | Test battery capacity and verify the power management system |
Important: Always perform a dry run of the vehicle in a controlled environment before taking it on the road to ensure all systems are working correctly.