Liquid Nitrogen Systems
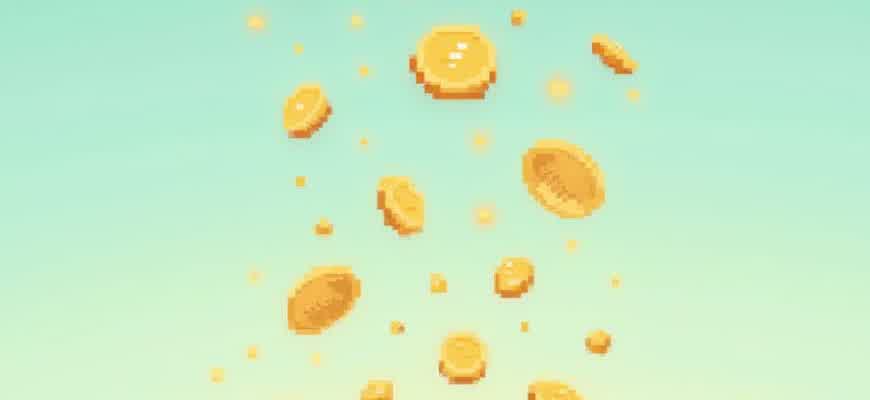
Cryogenic systems designed for handling liquid nitrogen are vital in various scientific and industrial applications. These systems allow for the safe storage, transport, and utilization of nitrogen in its liquid form at extremely low temperatures. Below, we will break down the key components and functions of these systems.
- Storage Tanks: Insulated vessels used for keeping liquid nitrogen at cryogenic temperatures.
- Pumping Units: Devices that transfer liquid nitrogen from storage to points of use.
- Pressure Regulators: Instruments that control the pressure within the system to ensure safe operation.
One of the crucial aspects of liquid nitrogen systems is their insulation, which minimizes heat transfer and evaporation. A typical cryogenic system includes several key components working in unison:
- Vacuum Insulation: Ensures minimal heat exchange with the environment.
- Heat Exchangers: Efficiently manage the cooling and warming cycles in the system.
- Safety Valves: Prevent overpressure conditions and potential accidents.
Note: Proper maintenance and regular inspection of liquid nitrogen systems are essential to prevent malfunction and ensure the safety of users.
Component | Function |
---|---|
Storage Tank | Stores liquid nitrogen at low temperatures to maintain its state. |
Transfer Lines | Facilitate the movement of liquid nitrogen to various points of use. |
Pressure Relief Valve | Ensures safe operation by regulating internal pressure. |
Choosing the Right Liquid Nitrogen System for Your Industry
Selecting the appropriate liquid nitrogen (LN2) system is crucial for ensuring operational efficiency and safety across different industrial applications. Whether for food preservation, pharmaceuticals, or metalworking, each industry requires specific system characteristics to meet its unique demands. Understanding the key factors that influence system design and functionality can prevent costly mistakes and improve overall system performance.
Several considerations must be taken into account when choosing an LN2 system, such as capacity, delivery method, and compatibility with existing infrastructure. Evaluating your operational requirements will help determine the best solution for your facility’s needs.
Key Considerations for System Selection
- Application Type: The system should be tailored to the particular industry needs, such as cryogenic freezing for food or cooling for metalworking.
- Flow Rate: Determine the required LN2 delivery rate to maintain optimal temperatures for your processes.
- Storage Capacity: The size of the LN2 tank should align with your production schedule and volume requirements.
- Safety Features: Ensure the system has necessary safety controls like pressure relief valves and temperature sensors.
Steps to Choose the Right System
- Assess Industry Needs: Start by identifying the specific requirements of your process, including temperature range and volume.
- Review Available Technologies: Compare different LN2 delivery methods like pressurized liquid nitrogen or vaporized systems.
- Consult with Experts: Work with engineers or manufacturers who specialize in LN2 systems for guidance and recommendations.
- Consider Long-Term Maintenance: Choose systems that are easy to maintain and service to minimize downtime.
“Safety and operational efficiency should be the top priorities when selecting a liquid nitrogen system. A well-designed system can enhance productivity and minimize the risks associated with handling cryogenic liquids.”
Comparison Table: Types of LN2 Systems
System Type | Applications | Storage Capacity | Flow Rate |
---|---|---|---|
Pressurized Delivery | Food Processing, Pharmaceutical | Large | High |
Vaporized Nitrogen | Metalworking, Cryopreservation | Medium | Moderate |
Portable Systems | Research, Laboratories | Small | Low |
Understanding Safety Standards for Liquid Nitrogen Handling
Liquid nitrogen (LN2) is widely used in various industries, from healthcare to engineering, but its extremely low temperature poses significant risks to personnel. Safe handling of liquid nitrogen requires adherence to strict protocols, ensuring both the safety of workers and the integrity of equipment. Understanding these safety standards is critical for preventing accidents and ensuring that LN2 is used efficiently and safely.
When dealing with liquid nitrogen, it is essential to follow established safety procedures to mitigate hazards such as asphyxiation, frostbite, and pressure-related incidents. This involves implementing proper storage, transportation, and usage protocols. Here are some key aspects of liquid nitrogen safety standards.
Key Safety Practices
- Ventilation: Always use LN2 in well-ventilated areas to prevent the buildup of nitrogen gas, which can displace oxygen and lead to asphyxiation.
- Protective Equipment: Wear appropriate personal protective equipment (PPE), including cryogenic gloves, face shields, and safety goggles to prevent direct contact with LN2.
- Proper Storage: Store LN2 in approved, vented containers to prevent the buildup of pressure. Always ensure that storage tanks are equipped with safety valves.
- Training: Ensure that all personnel handling LN2 are trained in proper safety protocols and emergency procedures.
Common Hazards and Preventive Measures
Hazard | Preventive Measure |
---|---|
Asphyxiation | Ensure adequate ventilation and use oxygen monitors in confined spaces. |
Frostbite | Always use cryogenic gloves and goggles when handling liquid nitrogen. |
Pressure Build-up | Store LN2 in containers with safety pressure relief valves. |
Important: Liquid nitrogen should never be stored or transported in non-vented containers, as the pressure build-up can lead to catastrophic failure.
Emergency Protocols
- In case of skin contact: Immediately flush the affected area with warm water and seek medical attention.
- In case of gas release in confined spaces: Evacuate the area immediately and call for emergency assistance.
- In case of container failure: Move to a safe area and alert the appropriate personnel to manage the situation.
Optimizing Liquid Nitrogen Storage and Transport
Efficient storage and transportation of liquid nitrogen (LN2) are critical to maintaining its quality and minimizing losses. Ensuring that containers are adequately insulated, minimizing heat transfer, and regularly monitoring system performance are vital steps in achieving optimization. Proper planning for storage and distribution ensures that LN2 remains at the required low temperatures while reducing operational costs.
By focusing on appropriate equipment, regular maintenance, and proper handling procedures, businesses can improve LN2 storage and transport efficiency. This can also reduce environmental impact and enhance safety standards. Below are key strategies to achieve these goals.
Key Strategies for Optimizing Storage and Transportation
- Insulation: Use vacuum-insulated storage vessels to reduce heat transfer and evaporation losses.
- Efficient Routing: Optimize delivery routes to minimize transportation time and prevent temperature increases during transit.
- Pressure Management: Ensure the storage containers maintain an appropriate pressure to avoid nitrogen boil-off.
- Leak Prevention: Regularly inspect storage systems for leaks to avoid nitrogen loss and ensure safety.
Best Practices for Storage and Transportation
- Use of Cryogenic Tanks: Select cryogenic tanks that are designed specifically for LN2, with built-in temperature and pressure monitoring systems.
- Regular Maintenance: Perform routine inspections and maintenance on both storage tanks and transportation vehicles to prevent degradation and ensure efficiency.
- Temperature Control: Constantly monitor temperatures during transportation to ensure LN2 remains below its boiling point.
Regular monitoring and the use of high-quality insulation materials are fundamental in reducing operational costs associated with liquid nitrogen storage and transportation.
Summary Table of Optimization Strategies
Strategy | Benefit |
---|---|
Vacuum-insulated storage | Reduces heat transfer and nitrogen loss |
Efficient routing | Minimizes transportation time and temperature fluctuations |
Pressure control | Maintains LN2 at proper temperature and pressure |
Cost Considerations: What to Expect When Installing a Liquid Nitrogen System
When planning the installation of a liquid nitrogen (LN2) system, it's crucial to understand the associated costs. These costs can vary greatly depending on the scale and complexity of the system, as well as the specific needs of your operation. Factors such as equipment, installation services, and ongoing maintenance play significant roles in the overall budget. Understanding these elements early can help avoid unexpected expenses and ensure smoother project management.
One of the most important aspects of LN2 system installation is the initial investment. The cost structure is typically influenced by the size of the facility, the capacity of the system, and the safety standards that need to be met. Below is a breakdown of the key cost components:
Key Cost Components
- Equipment Purchase: The price of tanks, compressors, and piping can be significant, depending on the required system capacity.
- Installation Services: Professional installation is essential to ensure the system is set up according to regulations and optimized for safety and efficiency.
- Safety Features: Compliance with safety standards often necessitates additional investments in monitoring systems, alarms, and emergency shutoff valves.
- Maintenance Costs: Ongoing maintenance is necessary to keep the system functioning efficiently and safely. This can include inspections, part replacements, and system upgrades.
Note: It's important to factor in both the initial installation costs and long-term maintenance requirements when budgeting for a liquid nitrogen system. Regular servicing is essential for minimizing downtime and avoiding costly repairs.
Example of Initial Installation Costs
Cost Component | Estimated Cost |
---|---|
Equipment (Tanks & Compressors) | $50,000 - $150,000 |
Installation Services | $20,000 - $50,000 |
Safety Features | $5,000 - $20,000 |
Maintenance (Annual) | $5,000 - $15,000 |
In addition to direct costs, consider potential cost-saving opportunities such as choosing energy-efficient equipment or negotiating long-term maintenance contracts. These choices can reduce overall expenses while ensuring the system operates optimally over time.
Common Uses of Liquid Nitrogen in Industrial Operations
Liquid nitrogen (LN2) plays a critical role in various industrial processes due to its low temperature and inert nature. As a versatile cryogenic fluid, it is utilized in a wide range of applications that require rapid cooling, preservation, or a controlled atmosphere. The ability to rapidly absorb heat and its non-reactive properties make it indispensable in numerous sectors such as manufacturing, food processing, and pharmaceuticals.
This technology has been integrated into many industrial systems to enhance productivity, improve safety, and reduce operational costs. Whether in cryogenic cooling for metals or in preserving biological materials, liquid nitrogen offers unique solutions that are difficult to replicate with other substances. Below are some of the most common industrial uses of LN2.
Key Applications of Liquid Nitrogen in Industry
- Metal Processing: Liquid nitrogen is commonly used for cooling metals during machining, forging, and grinding. It allows for faster processing speeds and enhances material properties, such as hardness.
- Food and Beverage: LN2 is employed for quick freezing of food products, ensuring minimal loss of nutrients and preserving texture and flavor.
- Medical and Pharmaceutical: Cryopreservation of biological samples and pharmaceutical products often involves liquid nitrogen to maintain cell integrity over long periods.
- Electronics and Semiconductor Manufacturing: LN2 is used in cooling systems for the production and testing of electronic components, helping maintain performance under extreme conditions.
- Cryogenic Cleaning: LN2 is utilized in cleaning and degreasing industrial equipment without the need for chemical solvents, reducing environmental impact.
Advantages of Using Liquid Nitrogen
Benefit | Explanation |
---|---|
Fast Cooling | Liquid nitrogen's extremely low temperature allows for rapid cooling of objects, speeding up various processes, such as metal hardening or food freezing. |
Non-reactive | LN2 does not interact with most materials, making it a safe and effective medium for preserving sensitive substances, such as biological samples. |
Cost-effective | Compared to other cooling agents, liquid nitrogen is relatively inexpensive and can be produced in large quantities, making it an economical choice for industrial applications. |
Liquid nitrogen’s ability to cool and preserve without causing chemical reactions is a key reason it is so widely used across various industries. Its versatility continues to drive innovation in fields ranging from food preservation to advanced materials manufacturing.
Troubleshooting Liquid Nitrogen System Failures
Liquid nitrogen (LN2) systems are vital for various applications in scientific research, cryogenics, and industrial processes. However, like any complex system, they are prone to failures that can disrupt operations and compromise safety. Understanding how to systematically identify and resolve these failures is crucial for maintaining the system’s functionality and preventing costly downtime.
This guide outlines common failure points in liquid nitrogen systems and offers troubleshooting steps to resolve them effectively. By following a structured approach, technicians can quickly diagnose the problem and take appropriate corrective action.
Common Failures in Liquid Nitrogen Systems
- Low Nitrogen Supply Pressure: Insufficient pressure may lead to an inability to supply liquid nitrogen at the required rate.
- Thermal Insulation Failure: Loss of insulation efficiency can result in the evaporation of LN2, causing a drop in pressure and temperature.
- Flow Restriction: Blockages or narrowing of pipes can obstruct the flow of nitrogen, causing a system to malfunction.
- Valve Leaks: Leaking valves or seals can lead to the loss of nitrogen and decreased system efficiency.
Step-by-Step Troubleshooting Process
- Check Pressure Gauges: Verify that the supply pressure is within the recommended range. Low pressure may indicate a problem with the nitrogen tank or the supply line.
- Inspect Insulation: Examine the insulation around pipes and storage tanks. Look for signs of wear or damage that may lead to heat transfer and increased nitrogen evaporation.
- Examine Valves: Test all valves for leaks. If there is a drop in pressure, inspect seals and replace them if necessary.
- Look for Flow Obstructions: Check all lines for potential blockages, such as ice buildup or debris, which could restrict the flow of liquid nitrogen.
Important Considerations
Ensure that all safety protocols are followed when troubleshooting LN2 systems, as liquid nitrogen can pose significant hazards due to its extremely low temperatures.
Table: Common Causes of System Failure
Cause | Symptoms | Solution |
---|---|---|
Low Pressure | Inadequate nitrogen flow, unstable system operation | Check supply pressure, verify tank integrity, replace pressure regulator if needed |
Insulation Failure | Excess nitrogen evaporation, pressure drop | Inspect insulation, replace damaged sections |
Flow Restriction | Reduced nitrogen flow rate, system shutdown | Clear blockages, inspect for pipe damage |
Valve Leaks | Pressure loss, nitrogen loss | Test valves for leaks, replace seals or faulty valves |
Training Employees to Handle Liquid Nitrogen Safely and Effectively
Liquid nitrogen is widely used in various industries due to its unique properties, such as extreme cold temperatures and versatility. However, the handling of this substance comes with significant risks, making proper training essential for workers who are exposed to it. Adequate training ensures not only the safety of employees but also the efficiency of operations where liquid nitrogen is used.
Effective training programs should cover both theoretical knowledge and practical skills. Employees must be taught the correct procedures for using, storing, and disposing of liquid nitrogen, as well as how to respond to emergencies. Additionally, these programs should address the importance of safety equipment, such as cryogenic gloves, goggles, and proper ventilation systems.
Key Training Components
- Understanding Risks: Employees should be made aware of the hazards associated with liquid nitrogen, including asphyxiation, frostbite, and the potential for pressure buildup in containers.
- Proper Handling Techniques: Safe handling practices, such as using insulated containers, preventing spills, and maintaining controlled environments, should be covered in detail.
- Emergency Procedures: Training must include clear guidelines on how to handle emergencies, such as leaks or personal injuries, and how to activate first aid measures.
Effective Training Methods
- Classroom Instruction: Provide foundational knowledge on liquid nitrogen properties and safety guidelines.
- Hands-On Training: Allow employees to practice using the equipment under controlled conditions, ensuring they can react appropriately in real-world scenarios.
- Regular Drills: Conduct periodic safety drills to reinforce correct responses to emergencies and hazards.
Important Note: Employees should never work alone when handling liquid nitrogen. It is crucial to have a trained team member nearby in case of an emergency.
Safety Equipment for Liquid Nitrogen Handling
Equipment | Purpose |
---|---|
Cryogenic Gloves | Protect hands from severe cold and frostbite. |
Face Shield and Goggles | Prevent eye injury from splashes or vapor exposure. |
Ventilation Systems | Ensure a safe working environment by preventing nitrogen buildup in confined spaces. |