What Is a Nitrogen System
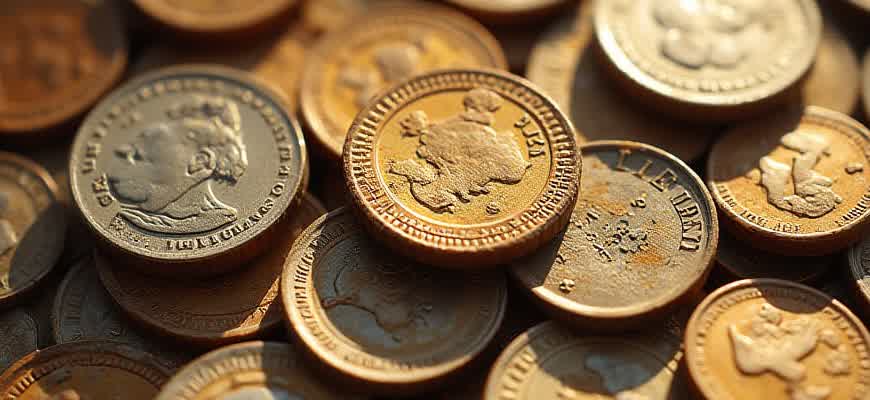
A nitrogen system is a critical component used in various industries to supply and manage nitrogen gas for different processes. Nitrogen is often used due to its inert properties, providing a safe, stable, and controlled atmosphere in numerous applications.
Such systems are designed to produce, store, and distribute nitrogen gas with specific purity and pressure levels. There are several types of nitrogen systems, each suited for distinct needs. Below are some of the key components and applications:
- Nitrogen Generation: The process where nitrogen is extracted from the air using methods like Pressure Swing Adsorption (PSA) or Membrane Separation.
- Nitrogen Storage: The storage of nitrogen in liquid or gas form in tanks or cylinders for later use.
- Nitrogen Distribution: The transport of nitrogen to the required locations through pipelines or cylinders.
"Nitrogen systems are vital in industries such as electronics manufacturing, food preservation, and oil and gas exploration, ensuring optimal conditions for various operations."
System Type | Application |
---|---|
Nitrogen Generator | Used for on-site nitrogen production, reducing reliance on external gas suppliers. |
Liquid Nitrogen Storage | For industries requiring large volumes of ultra-cold nitrogen for cooling or inert atmospheres. |
Cylinder Systems | Portable nitrogen storage for smaller operations or specific needs. |
Understanding the Basic Components of a Nitrogen System
A nitrogen system consists of several key components that work together to produce, store, and distribute nitrogen gas in various applications. Whether used in industrial processes, food preservation, or medical fields, understanding the roles of each component is crucial for maintaining efficient and safe operations. Below is a breakdown of these essential elements.
The main components of a nitrogen system include nitrogen generators, storage tanks, pressure regulators, and distribution piping. Each of these parts plays a specific role in ensuring that the nitrogen is produced at the required purity level and delivered at the correct pressure to its intended location.
Key Elements of a Nitrogen System
- Nitrogen Generator: This device is responsible for producing nitrogen gas from the air using processes like pressure swing adsorption (PSA) or membrane separation.
- Storage Tanks: These tanks are used to store nitrogen at high pressure, ensuring a steady supply when demand exceeds the production capacity of the generator.
- Pressure Regulators: These components control and maintain the pressure of the nitrogen gas as it moves through the system to ensure that it meets the required specifications.
- Distribution Piping: The piping network transports nitrogen gas from the generator or storage tank to the point of use. It is designed to handle the high pressures associated with nitrogen delivery.
Each component of the nitrogen system is designed to optimize efficiency, minimize wastage, and ensure that nitrogen is available at the right time and pressure for the required application.
Component Functionality in Detail
Component | Function |
---|---|
Nitrogen Generator | Produces nitrogen gas by separating nitrogen from the air using PSA or membrane technology. |
Storage Tank | Stores nitrogen gas at high pressure for later use, ensuring uninterrupted supply. |
Pressure Regulator | Maintains the correct pressure for the nitrogen as it moves through the system. |
Distribution Piping | Transports nitrogen to the required points of use, maintaining pressure and flow rates. |
How Nitrogen Systems Improve Industrial Operations
Nitrogen systems have become essential in various industrial operations due to their ability to provide a reliable, safe, and efficient environment for processes that require an inert atmosphere. These systems help reduce the risk of fire, corrosion, and contamination, making them indispensable in industries such as food packaging, pharmaceuticals, and oil refining. By generating high-purity nitrogen on-site, companies can lower costs associated with bulk gas deliveries and reduce the dependency on external suppliers.
Another significant advantage of nitrogen systems is their ability to improve the quality and longevity of products by maintaining controlled atmospheres. This is particularly important in industries where product shelf life or stability is a critical factor. Moreover, nitrogen plays a key role in optimizing production processes by enabling precise control over reactive environments, ensuring consistency and reducing errors.
Key Benefits of Nitrogen Systems
- Increased Safety: Nitrogen’s inert properties help to minimize the risk of explosive reactions in environments that involve flammable or reactive materials.
- Cost Efficiency: On-site nitrogen generation eliminates the need for costly deliveries and storage of bulk nitrogen, leading to significant savings over time.
- Improved Product Quality: By creating controlled atmospheres, nitrogen systems prevent contamination and preserve the quality of sensitive products.
- Energy Efficiency: Advanced nitrogen systems are designed to optimize energy consumption, ensuring minimal waste during production.
Applications of Nitrogen Systems
- Food Packaging: Nitrogen is used to displace oxygen in packaging to extend shelf life and prevent spoilage.
- Pharmaceutical Manufacturing: Nitrogen maintains sterile environments, protecting products from contamination during production and storage.
- Oil Refining: Nitrogen is used to control chemical reactions and minimize the risk of fire and explosions in refining processes.
Efficiency in Operations
Nitrogen systems provide a steady supply of gas, allowing industries to maintain continuous production cycles without interruptions due to gas shortages or fluctuations in pressure.
Comparison of Nitrogen Systems and Traditional Gas Supply
Factor | Nitrogen System | Traditional Gas Supply |
---|---|---|
Cost | Lower operational costs over time | Higher long-term costs due to gas deliveries |
Reliability | Continuous, on-demand supply | Potential for supply interruptions |
Environmental Impact | Lower carbon footprint with on-site generation | Higher emissions due to transportation and storage |
Common Applications of Nitrogen Systems in Various Industries
Nitrogen systems are widely utilized across different sectors due to their versatility and safety features. In many industries, nitrogen is employed as an inert gas, helping to control environments, preserve products, or enhance production processes. It is particularly favored for its ability to displace oxygen and moisture, which can be harmful in certain conditions.
These systems are essential for reducing risks associated with fire, oxidation, and contamination. Below are some of the main industrial applications of nitrogen systems:
1. Food and Beverage Industry
In the food and beverage industry, nitrogen is extensively used for preservation, packaging, and transportation. It prevents spoilage and extends shelf life by eliminating oxygen, which can cause oxidation and contamination. Nitrogen is also used in the cryogenic freezing process to preserve food quality.
- Modified Atmosphere Packaging (MAP): Increases product shelf life and maintains freshness.
- Food Freezing: Cryogenic freezing to preserve texture and flavor.
- Wine Preservation: Nitrogen blanketing prevents oxidation in wine barrels.
2. Pharmaceutical and Chemical Industries
Nitrogen is essential in these industries for creating controlled atmospheres during the production and storage of sensitive compounds. It is used for inerting processes, preventing unwanted chemical reactions, and ensuring the safety of volatile substances.
- Inerting Processes: Prevents reactions by maintaining a non-reactive atmosphere.
- Pharmaceutical Packaging: Protects drugs from degradation due to oxygen exposure.
- Chemical Synthesis: Nitrogen is used to eliminate moisture and oxygen during chemical reactions.
3. Oil and Gas Industry
The oil and gas sector relies on nitrogen systems for several applications, including well stimulation, pipeline maintenance, and safety. Nitrogen is used for its non-flammable properties, making it ideal for creating safe working environments in hazardous conditions.
Nitrogen is used in oil and gas drilling operations to pressurize wells and prevent explosive situations.
4. Electronics Manufacturing
In electronics manufacturing, nitrogen is employed in the assembly of delicate components, where a moisture-free and oxygen-free environment is critical. This is especially important for the production of semiconductors and other sensitive materials.
Application | Industry | Purpose |
---|---|---|
Controlled Atmosphere | Electronics | Prevents oxidation in microelectronics and components. |
Packaging | Pharmaceuticals | Protects drugs from exposure to air and moisture. |
Key Considerations When Choosing a Nitrogen Generator
When selecting a nitrogen generator, several critical factors must be evaluated to ensure it meets the specific needs of your application. The primary considerations include the generator's production capacity, efficiency, and compatibility with your existing infrastructure. Understanding the intended use of nitrogen–whether for laboratory applications, industrial processes, or food packaging–will help guide the decision-making process.
Another crucial factor to take into account is the operating costs over the lifespan of the equipment. Factors like energy consumption, maintenance requirements, and the cost of replacement parts can significantly impact long-term expenses. Below are some important points to consider when choosing the right nitrogen generator for your needs:
- Purity of Nitrogen: Ensure the generator can provide the required purity level for your application, whether it is standard industrial grade or ultra-high purity for sensitive processes.
- Flow Rate: Choose a system that can meet your required nitrogen flow rates without underperforming or leading to inefficiencies.
- Energy Efficiency: Evaluate the energy consumption of different models to avoid unnecessary operational costs.
- Maintenance and Service: Consider the ease of servicing and availability of support to minimize downtime.
Always factor in the overall operational costs, not just the initial purchase price of the nitrogen generator.
Important Factors in Nitrogen Generator Selection
- Operating Environment: Ensure the generator is designed to function efficiently in your specific working conditions, including temperature, humidity, and atmospheric pressure.
- Regulatory Compliance: Make sure the chosen nitrogen system meets relevant industry standards and regulatory requirements.
- Brand Reliability: Opt for manufacturers with a proven track record for quality and customer support.
Factor | Consideration |
---|---|
Purity | Required nitrogen purity for specific applications (e.g., 99.9% for food packaging, 99.99% for lab use) |
Flow Rate | Ensure the system meets both peak and average nitrogen demand in your operations |
Energy Efficiency | Consider energy-saving technologies like pressure swing adsorption (PSA) or membrane filtration systems |
How to Maintain a Nitrogen System for Long-Term Performance
Proper maintenance of a nitrogen system is essential for ensuring its efficient operation over time. A well-maintained system prevents failures, enhances safety, and extends the lifespan of its components. Regular checks and care are critical to keep the system functioning at optimal capacity. This guide outlines the key steps to ensure the longevity and efficiency of your nitrogen system.
Maintaining a nitrogen system involves several critical tasks such as monitoring pressure levels, inspecting the nitrogen generator, checking filters, and ensuring that all valves and pipes are leak-free. Implementing a maintenance schedule can significantly reduce the risk of unexpected downtime and costly repairs.
Key Maintenance Practices
- Monitor system pressure regularly to ensure it stays within the specified range.
- Inspect nitrogen generation equipment for wear and tear.
- Check filters and replace them when needed to maintain air quality.
- Examine piping and connections for leaks or damage.
- Verify that valves are functioning correctly and do not show signs of corrosion.
Important Checklist for Long-Term Maintenance
- Conduct monthly pressure checks and adjust settings as necessary.
- Replace filters every 6 to 12 months, depending on usage levels.
- Perform annual inspections of the nitrogen generator and all related components.
- Ensure all safety alarms and backup systems are tested periodically.
- Lubricate moving parts to prevent wear and rust.
Table: Maintenance Timeline
Task | Frequency |
---|---|
Pressure Check | Monthly |
Filter Replacement | Every 6-12 months |
Generator Inspection | Annually |
Valve and Pipe Inspection | Annually |
Note: Regular maintenance will not only improve efficiency but also ensure compliance with safety regulations and prevent unexpected system failures.
Cost Breakdown of Implementing a Nitrogen Generation System
Implementing a nitrogen generation system involves several key cost components, which must be carefully evaluated during the planning phase. The primary expenses are related to equipment, installation, and ongoing maintenance. These factors can vary significantly depending on the scale of the system, its capacity, and the specific requirements of the industry or application. Below is a detailed analysis of the costs involved in setting up a nitrogen system.
Understanding the cost breakdown is essential for making an informed decision about whether investing in a nitrogen generation system is the best solution. The costs can be divided into initial capital expenditure (CapEx) and recurring operational expenditure (OpEx). These include the purchase of equipment, installation fees, and long-term service requirements.
Cost Categories
- Capital Costs: These are the one-time expenses incurred during the installation of the nitrogen generation system.
- Operational Costs: These ongoing expenses are related to the energy consumption, maintenance, and service of the system.
- Installation and Setup: This includes the labor, transportation, and infrastructure required to integrate the system into the existing setup.
Detailed Breakdown
Cost Category | Estimated Cost |
---|---|
Equipment Purchase (Nitrogen Generator) | $50,000 - $200,000 |
Installation and Setup | $10,000 - $30,000 |
Energy Consumption (Annual) | $5,000 - $20,000 |
Maintenance and Service (Annual) | $2,000 - $10,000 |
Note: Initial capital costs can vary depending on the system’s capacity and the technology used. Larger systems designed for industrial applications will naturally require higher investments.
Additional Considerations
- System Efficiency: A higher efficiency nitrogen generator may reduce operational costs over time, making it a more cost-effective long-term option.
- Energy Source: The choice of energy (electricity vs. alternative sources) can significantly influence operational expenses.
- Scalability: Consider the potential for scaling the system to meet future demand. Larger systems typically come with a higher upfront cost but may offer better value in the long run.
Safety Protocols for Operating a Nitrogen System
Operating a nitrogen system requires strict adherence to safety protocols to prevent potential hazards such as leaks, over-pressurization, or accidental exposure to high concentrations of nitrogen. Nitrogen, while inert, can displace oxygen in confined spaces, posing a serious risk of asphyxiation. Proper training, equipment, and procedures are essential for ensuring safe operation.
The following safety measures must be implemented when handling nitrogen systems:
Key Safety Measures
- Proper Ventilation: Ensure that the work environment is well-ventilated to avoid the accumulation of nitrogen gas, which can lead to oxygen depletion.
- Personal Protective Equipment (PPE): Wear appropriate PPE such as safety goggles, gloves, and respiratory protection when working with nitrogen systems.
- Leak Detection: Use specialized detectors to monitor for nitrogen leaks in the system, especially in confined or enclosed spaces.
- System Inspection: Regularly inspect valves, pipes, and pressure regulators to ensure the integrity of the nitrogen system and prevent malfunctions.
Operational Guidelines
- Never Enter Confined Spaces: Never enter a confined space where nitrogen is used or stored without proper training and safety protocols in place.
- Pressurization Limits: Always follow the manufacturer’s guidelines for safe pressure limits to prevent over-pressurization, which could cause equipment failure or accidents.
- Shutoff Procedures: Be familiar with emergency shutdown procedures in case of system failure or leak detection.
Note: In case of nitrogen exposure, immediately move to an area with fresh air and seek medical attention if symptoms of asphyxiation occur.
Emergency Preparedness
Emergency Action | Required Action |
---|---|
Gas Leak Detection | Stop the nitrogen flow and evacuate the area while notifying safety personnel. |
Oxygen Deprivation | Evacuate the affected area, seek fresh air, and provide oxygen if necessary. |
Pressure Relief | Follow the depressurization protocol as per the system's manual to avoid damage or injury. |
Future Trends in Nitrogen System Technology
The nitrogen generation industry is continuously evolving, with a strong focus on improving efficiency, sustainability, and cost-effectiveness. As demand for nitrogen in various industrial applications grows, innovative technologies are being developed to address challenges such as energy consumption, operational costs, and environmental impact. The future of nitrogen systems will likely be shaped by advancements in membrane technology, pressure swing adsorption (PSA) systems, and automation solutions that enable smarter, more responsive operations.
Among the most notable trends is the integration of artificial intelligence (AI) and machine learning (ML) in nitrogen system monitoring and control. These technologies enable real-time data analysis, predictive maintenance, and adaptive optimization, improving system reliability and reducing downtime. Additionally, the transition to more environmentally friendly solutions, including renewable energy-powered nitrogen production, will play a pivotal role in shaping the future of the industry.
Key Future Developments
- Advanced Membrane Materials: Innovations in membrane technology are expected to improve nitrogen purity and recovery rates, reducing the overall cost of nitrogen generation.
- Smart Automation Systems: Increased adoption of AI and IoT technologies will lead to more efficient, self-regulating nitrogen systems, minimizing human intervention and enhancing system performance.
- Energy Efficiency: The next generation of nitrogen generators will prioritize energy-saving designs, such as energy recovery systems and integration with renewable energy sources.
Benefits of Emerging Technologies
"The integration of renewable energy into nitrogen production processes not only reduces carbon footprints but also promises long-term cost savings for industries reliant on nitrogen generation."
- Reduced Operational Costs: More energy-efficient systems will lower both energy consumption and operational costs, making nitrogen production more affordable for industries.
- Enhanced Sustainability: The shift to green energy solutions and more efficient processes will help reduce the environmental impact of nitrogen production.
- Improved Performance: AI-powered monitoring systems will provide more accurate and real-time performance data, optimizing nitrogen production and enhancing reliability.
Impact on Industries
Industry | Impact of Future Nitrogen System Trends |
---|---|
Food and Beverage | Improved product quality and packaging, with reduced energy costs for nitrogen supply. |
Electronics | More efficient and reliable nitrogen supply for controlled atmospheres in semiconductor manufacturing. |
Agriculture | Energy-efficient systems for enhanced crop protection and storage, contributing to sustainable farming practices. |