Convert Nitro Engine to Gas
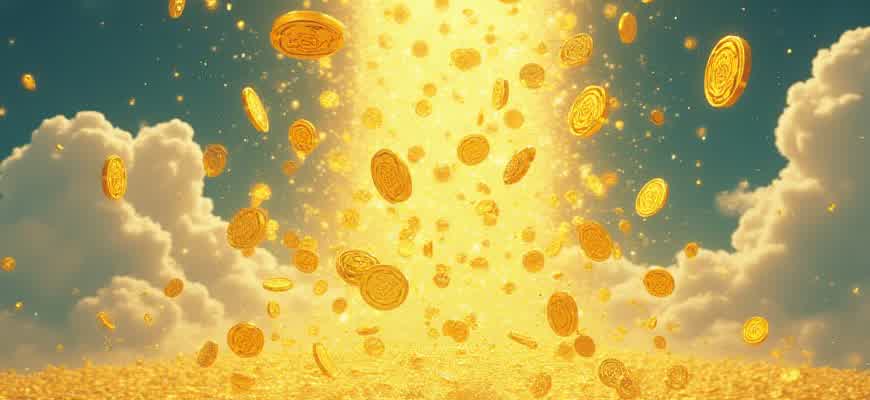
Converting a nitro engine to a gas-powered engine requires a series of modifications to the fuel system, ignition, and engine components. The key differences between the two types of engines are primarily based on the fuel mixture, ignition timing, and engine design. Gas engines typically run on a gasoline-oil mixture, whereas nitro engines use a specialized fuel containing nitromethane and methanol. To make the conversion, several steps must be followed to ensure proper function and performance.
Important Note: Always consult the engine manufacturer’s guidelines before making any changes, as modifications may void warranties or damage components if done incorrectly.
Here are the primary steps for converting a nitro engine to gas:
- Fuel System Modification: The nitro engine will need a new fuel tank, fuel lines, and carburetor compatible with gasoline fuel.
- Ignition System Update: The spark plug and ignition timing system should be adjusted to match gasoline’s combustion characteristics.
- Engine Tuning: Recalibrate the carburetor for the correct air-fuel ratio suitable for gas engines.
- Compression Adjustment: Gas engines typically require higher compression, so adjusting the engine’s piston and cylinder is essential.
Component | Nitro Engine | Gas Engine |
---|---|---|
Fuel Type | Nitromethane & Methanol | Gasoline & Oil |
Ignition | Glow Plug | Spark Plug |
Compression Ratio | Lower | Higher |
Choosing the Right Conversion Kit for Your Nitro Engine
When it comes to converting a Nitro engine to run on gasoline, selecting the correct conversion kit is critical for achieving optimal performance and longevity. There are various factors to consider, including engine specifications, fuel compatibility, and ease of installation. By understanding the key components and their functions, you can ensure a smooth transition and maximize the benefits of gasoline over Nitro fuel.
The conversion kit includes several key parts such as carburetors, fuel lines, ignition systems, and exhaust systems. However, not all kits are the same, and selecting the wrong one can lead to poor performance or engine damage. Carefully evaluate the options based on your engine's specifications, as well as the quality of the components included in the kit.
Factors to Consider When Choosing a Conversion Kit
- Engine Compatibility: Ensure the kit is designed for your specific Nitro engine model. Some kits are universal, while others are tailored for certain brands and sizes.
- Fuel System Requirements: Gasoline engines require a different fuel delivery system. Verify that the kit includes the correct carburetor and fuel lines compatible with gasoline.
- Performance Enhancements: Look for kits that offer additional features like upgraded carburetors or high-efficiency ignition systems, which can improve engine performance.
- Ease of Installation: Choose a kit that is straightforward to install and comes with clear instructions. Complicated installations may require professional help, increasing costs.
Steps for Selecting the Right Kit
- Research your engine's specifications, including engine displacement and the type of fuel it currently uses.
- Compare different conversion kits available for your engine type, paying attention to the compatibility with your engine's components.
- Check for online reviews and feedback from other users who have completed the conversion.
- Consider your skill level for installation, and whether you need a simple kit or one that requires more advanced technical knowledge.
"Choosing the right conversion kit isn't just about cost; it's about ensuring your engine runs smoothly and efficiently after the conversion."
Comparison of Popular Conversion Kits
Brand | Compatibility | Performance Enhancements | Price Range |
---|---|---|---|
Brand A | Universal | Upgraded Carburetor, High-Efficiency Ignition | $100 - $150 |
Brand B | Specific Models | Improved Fuel Delivery System | $120 - $180 |
Brand C | Universal | Enhanced Exhaust System | $90 - $130 |
Step-by-Step Process of Converting a Nitro Engine to Gas
Converting a nitro engine to gas requires several key modifications to ensure compatibility with the new fuel type. The process involves adjusting fuel systems, tuning, and replacing certain components. By following a structured approach, you can achieve a smooth transition and improve engine performance on gas fuel.
Before beginning the conversion, gather the necessary parts, tools, and knowledge of the specific engine model you are working with. Each engine might have unique requirements, so ensure you have all the information beforehand. Below is a general guide to help with the conversion process.
Necessary Modifications
- Fuel System Conversion: The most critical aspect is switching from nitro fuel to gas. This includes replacing the carburetor, fuel tank, and fuel lines designed for nitro fuel.
- Ignition System: Nitro engines rely on a glow plug to ignite the fuel, whereas gas engines require a spark plug. Replacing the glow plug with a suitable spark plug is essential.
- Compression Adjustment: Gas engines generally need higher compression than nitro engines. You may need to adjust the compression settings or replace the piston and cylinder assembly.
- Exhaust System: The exhaust system may also need to be modified for better gas engine performance. Ensure the exhaust outlet size matches the new engine's requirements.
Conversion Process
- Start by removing the nitro engine components such as the carburetor, glow plug, and fuel system parts.
- Replace the carburetor with a gas-specific model that is compatible with your engine.
- Swap the glow plug for a spark plug of the correct size and heat range.
- Adjust the compression by either modifying the cylinder head or installing a higher-compression piston and cylinder assembly.
- Install a new ignition system that includes a spark plug, ignition coil, and associated wiring.
- Finally, replace the exhaust system if needed, ensuring it is designed to handle the different pressures and temperatures of a gas engine.
Important Considerations
Be mindful of the engine's tuning requirements after the conversion. Gas engines often have different fuel-to-air ratios and spark timing compared to nitro engines. Properly tune the engine for optimal performance.
Comparison of Nitro and Gas Engine Components
Component | Nitro Engine | Gas Engine |
---|---|---|
Fuel Type | Nitromethane-based fuel | Gasoline or gas-based fuel |
Ignition | Glow plug | Spark plug |
Compression | Lower compression | Higher compression |
Carburetor | Nitro-specific carburetor | Gas-specific carburetor |
Common Challenges During Conversion and How to Overcome Them
Converting a Nitro engine to run on gas can be a complex process, requiring precise modifications and adjustments. One of the main challenges is ensuring that the engine components are compatible with the new fuel system. Differences in combustion characteristics between Nitro and gasoline fuel can lead to issues such as poor performance, inefficient fuel consumption, and engine damage if not addressed properly.
Another significant challenge is the proper calibration of the ignition timing and fuel delivery system. These parameters must be finely tuned to ensure the engine runs smoothly on gasoline without causing misfires or overheating. In addition, replacing the nitro-specific parts with those designed for gas operation can be costly and time-consuming.
Key Issues and Solutions
- Fuel System Compatibility: The fuel delivery system for Nitro engines is different from gas engines, requiring new injectors, fuel lines, and a different carburetor setup.
To address this, consider upgrading to a universal fuel system that supports both fuel types or install a dedicated gas carburetor designed for your engine.
- Ignition Timing Adjustment: Nitro engines typically operate at a different ignition timing than gas engines, which can cause problems if left unchanged.
Using an adjustable ignition system allows you to fine-tune the timing for optimal performance when switching to gasoline.
- Compression Ratio: Nitro engines have a higher compression ratio than gas engines, which could result in knocking or inefficiency when running on gasoline.
Modify the compression ratio by changing the piston or cylinder head, or use additives to reduce the chance of knocking in the engine.
Considerations for Proper Conversion
- Ensure that all engine seals are gas-compatible, as Nitro fuel can degrade rubber and plastic components over time.
- Consider upgrading the carburetor to one specifically designed for gasoline, as nitro carbs often have a different design and flow rate.
- Regularly check fuel lines and fuel tank seals to ensure no leaks, as gasoline requires a different level of sealing than Nitro fuel.
Comparison of Components
Component | Nitro Engine | Gas Engine |
---|---|---|
Fuel Delivery | Nitro-specific carburetor | Gasoline carburetor or fuel injection system |
Ignition Timing | Advanced timing | Standard timing |
Compression Ratio | Higher compression | Lower compression |
Essential Tools and Equipment for a Smooth Conversion
Converting a nitro engine to run on gasoline requires careful preparation and the right tools to ensure a smooth and efficient transition. Whether you're performing the conversion on a car, boat, or another vehicle, having the proper equipment can make a significant difference in the outcome. Below is a guide to the primary tools and parts you will need for this project.
Before starting the conversion, it is essential to have the following tools and equipment. These tools will help you modify the engine, install new components, and ensure that everything is working correctly. Here is a detailed list of the most important items required for a successful gas conversion.
Key Tools and Parts for Conversion
- Wrenches and Socket Set: For removing and installing various engine parts, such as the exhaust system, carburetor, and engine block components.
- Carburetor Conversion Kit: Essential for adapting the engine to run on gasoline instead of nitro fuel.
- Fuel Line and Pump: To ensure proper fuel flow from the gas tank to the engine, you will need a reliable fuel line and pump.
- Fuel Tank: A suitable gas tank designed for the new fuel type must be installed.
- Ignition System Components: Depending on the engine type, upgrading the ignition system may be necessary for compatibility with gasoline.
- Air Filter: The existing air filter might need to be replaced to optimize airflow for gasoline combustion.
Step-by-Step Process for Conversion
- Begin by removing the nitro engine’s carburetor and fuel system components.
- Install the new carburetor and fuel system that is compatible with gasoline.
- Replace the nitro fuel tank with a gasoline-compatible tank and connect the fuel line and pump.
- Update the ignition system if necessary, ensuring compatibility with the new fuel type.
- Test the engine to ensure proper fuel delivery and spark plug performance.
Important Considerations
When converting to gasoline, always check the manufacturer’s specifications for the engine, as certain components may need additional modifications. Pay attention to the fuel-to-air ratio, as using the wrong mixture can damage the engine.
Additional Tools You Might Need
Tool | Purpose |
---|---|
Torque Wrench | To ensure proper torque settings during reassembly. |
Multimeter | To test the electrical system and ensure spark plug compatibility. |
Safety Equipment | Gloves, goggles, and a fire extinguisher for safety during the conversion. |
Adjusting the Carburetor for Gas Fuel after Engine Conversion
After converting a Nitro engine to run on gas, proper carburetor adjustment is crucial for optimal performance. Gasoline requires a different air-fuel mixture than nitro fuel, meaning that the carburetor must be calibrated to accommodate these changes. Without proper adjustments, the engine may run inefficiently, overheat, or even fail to start.
Below is a detailed guide on how to properly adjust the carburetor for gas fuel after conversion, ensuring the engine operates smoothly and efficiently. This process involves several key steps that must be followed to ensure the engine's longevity and performance.
Steps to Adjust the Carburetor
- Adjust the Idle Speed: Start by setting the idle speed screw. Gasoline engines generally require a slightly higher idle speed compared to nitro engines. This is necessary to prevent stalling and ensure smooth startup.
- Set the Low-End Needle: The low-end needle controls the fuel mixture at idle and low throttle settings. Start by turning the low-end needle counterclockwise slightly to allow more fuel into the mixture, then test by running the engine at low speeds.
- Adjust the High-End Needle: The high-end needle governs the fuel flow at full throttle. Since gasoline burns differently than nitro fuel, you will need to fine-tune this setting. Typically, start with a leaner setting (turning the needle clockwise) and adjust until the engine runs cleanly at full throttle.
- Check the Air-Fuel Mixture: After adjusting both needles, check the overall air-fuel mixture by performing test runs at various speeds. If the engine sputters or hesitates, lean the mixture slightly. If the engine bogs down or lacks power, richen the mixture.
Important Tips
Remember that small adjustments can make a significant impact on engine performance. Always make gradual changes and test the engine after each adjustment.
Carburetor Settings for Gas Fuel
Needle Setting | Recommended Adjustment |
---|---|
Idle Speed Screw | Adjust for a slightly higher idle compared to nitro settings. |
Low-End Needle | Start with a rich setting and lean gradually as needed. |
High-End Needle | Lean the mixture slightly at full throttle, testing for clean acceleration. |
Testing and Tuning the Engine After Conversion
Once the Nitro engine has been converted to gas, it is crucial to conduct a series of tests and adjustments to ensure optimal performance. The initial testing phase involves checking engine response, fuel efficiency, and overall reliability. Tuning, on the other hand, involves fine-tuning various components to achieve the best balance of power and efficiency. This process may require several iterations to get the engine running smoothly.
After performing the conversion, begin by running the engine at low RPMs to assess any immediate issues, such as irregular sounds or vibrations. Gradually increase RPMs, checking for proper fuel flow and smooth combustion. Following the initial testing, proceed to detailed tuning, including adjustments to the carburetor, ignition system, and exhaust settings.
Key Testing Steps
- Check fuel system integrity: Ensure there are no leaks and that the fuel lines are properly connected.
- Monitor engine temperature: Overheating can be a sign of insufficient cooling or incorrect fuel mixture.
- Verify compression levels: This is critical for engine performance and longevity.
- Inspect spark plugs: These should be clean and properly gapped for optimal ignition.
Essential Tuning Adjustments
- Fuel Mixture: Adjust the air-fuel ratio for smoother operation. A rich mixture is often required for cold starts, while a lean mixture improves fuel efficiency once the engine warms up.
- Ignition Timing: Fine-tune the timing to ensure the spark occurs at the right moment for optimal combustion.
- Carburetor Settings: Modify the idle and high-speed needle valves to fine-tune engine response and throttle response.
- Exhaust System: Ensure proper exhaust flow to prevent backpressure that can affect engine performance.
Proper testing and tuning are essential for achieving the best performance from a converted engine. Neglecting this phase can lead to engine damage or inefficient operation.
Sample Tuning Table
Component | Adjustment Range | Purpose |
---|---|---|
Fuel Mixture | Rich to Lean | Adjust for optimal combustion and fuel efficiency |
Ignition Timing | Advanced to Retarded | Maximize power output and prevent knocking |
Carburetor Settings | Idle and High-speed Needles | Improve throttle response and idle smoothness |
Exhaust Flow | Free Flow | Reduce backpressure and increase exhaust efficiency |
Maintaining Your Gas Engine After the Conversion
Once you've successfully converted your Nitro engine to a gas-powered one, proper maintenance becomes crucial to ensure its longevity and performance. Regular upkeep will not only extend the engine's life but also help in avoiding common issues that can arise after conversion. Gas engines require different care compared to Nitro engines, so it's important to adapt your maintenance practices accordingly.
In this guide, we'll discuss the key steps and tips for maintaining a gas engine post-conversion. From fuel management to regular inspection of vital components, keeping your engine in top condition requires attention to detail and routine care.
Key Maintenance Practices
- Fuel Quality and Management: Always use high-quality gas that is recommended for your engine type. Avoid mixing fuel with excessive oil or impurities that can damage the internal components.
- Air Filter Cleaning: Regularly clean or replace the air filter to prevent dirt and debris from entering the engine. A clogged filter can restrict airflow and reduce engine performance.
- Spark Plug Maintenance: Check and clean the spark plugs regularly. Replace them when necessary to ensure efficient combustion and smooth engine operation.
- Engine Lubrication: Periodically inspect and lubricate moving parts to reduce wear and tear. Use the manufacturer-recommended oil for optimal performance.
Regular Inspections
- Check the fuel lines for cracks or leaks that may occur over time.
- Inspect the exhaust system for blockages or corrosion.
- Examine the carburetor for any signs of fuel buildup or clogging.
- Ensure the cooling system is functioning properly, preventing the engine from overheating.
Important: Regular maintenance and timely replacements of worn-out parts can significantly reduce the risk of engine failure.
Recommended Maintenance Schedule
Task | Frequency |
---|---|
Air Filter Cleaning | Every 10-15 hours of use |
Spark Plug Inspection | Every 20-30 hours of use |
Fuel Line Check | Every 50 hours of use |
Oil Change | Every 25-30 hours of use |
Cost Breakdown: Converting a Nitro Engine to Gas
The conversion of a nitro engine to a gas-powered one can lead to significant financial changes, both in the short and long term. While nitro engines are known for their high performance, their operational costs can be considerably higher due to fuel price fluctuations, maintenance requirements, and overall fuel consumption. In contrast, gas engines tend to offer better fuel efficiency and lower fuel costs, but they come with their own set of expenses when undergoing such a conversion. Understanding the key cost factors can help make an informed decision on whether this conversion is worthwhile in the long run.
Cost considerations are crucial in determining the overall feasibility of engine conversion. When switching from nitro to gas, it’s important to compare both the upfront investment required for the conversion and the ongoing operational costs. Key factors include fuel expenses, maintenance frequency, and the need for special parts. Below, we’ll break down these aspects and analyze how they affect the total cost over time.
Fuel Costs Comparison
Fuel is one of the most significant costs associated with any engine. Nitro fuel is typically more expensive than gasoline, and its consumption rate is usually higher. On the other hand, gas engines tend to be more fuel-efficient and cost-effective. Here's a comparison of fuel costs:
Fuel Type | Cost per Liter | Consumption Rate |
---|---|---|
Nitro | $10 - $15 | 1-2 liters per hour |
Gasoline | $1 - $2 | 0.5-1 liters per hour |
Maintenance Expenses
In addition to fuel costs, maintenance expenses vary depending on the engine type. Nitro engines tend to have higher maintenance costs due to their complex nature and the high temperatures they generate. On the other hand, gas engines generally have fewer maintenance requirements and longer intervals between services. Consider the following factors:
- Nitro Engine Maintenance: Requires frequent tuning, more replacement parts, and high-quality lubricants.
- Gas Engine Maintenance: Less frequent tuning, lower replacement part costs, and longer intervals between oil changes.
Note: While the initial conversion may involve more complex parts and labor, long-term savings in maintenance can make gas engines more economical.
Initial Conversion Costs
The conversion from nitro to gas requires specific parts and modifications that can significantly impact the initial investment. Some essential components include:
- Gasoline fuel tank and lines
- Carburetor and ignition system
- Modified exhaust system
- Additional cooling components
The cost of these parts can vary, but generally, the upfront cost of conversion is higher than simply running a nitro engine, as it involves specialized equipment and labor.