How Does a Nitrogen Generator System Work
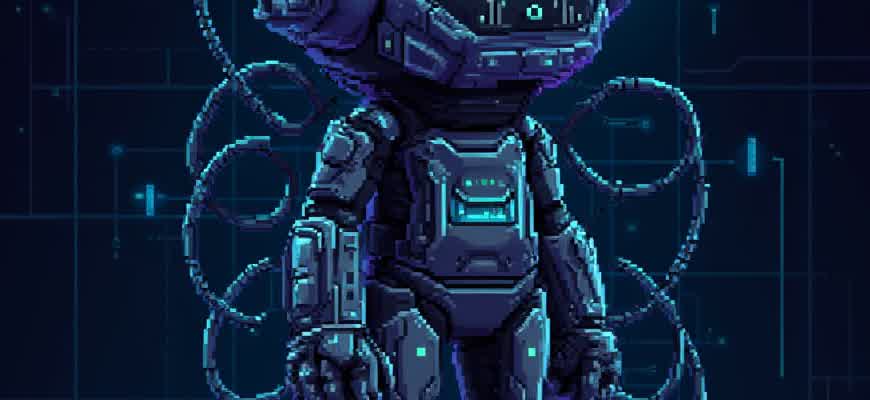
A nitrogen generation system operates by separating nitrogen from ambient air and providing a continuous supply of pure nitrogen gas. The process typically involves several advanced technologies designed to filter, separate, and compress the air to produce nitrogen at the required purity levels. Below is a breakdown of how this system works:
- Air Compression: The air is first drawn into the system and compressed to a higher pressure for further treatment.
- Separation Process: Nitrogen is separated from oxygen and other gases using methods like Pressure Swing Adsorption (PSA) or Membrane Technology.
- Purity Adjustment: The nitrogen gas is then purified to the desired concentration level, which can range from 95% to 99.99% depending on the application.
The main technologies used in nitrogen generation systems are:
- Pressure Swing Adsorption (PSA): A process where air is passed through adsorbent materials that preferentially capture oxygen, leaving nitrogen to pass through.
- Membrane Technology: Air is filtered through semi-permeable membranes that allow nitrogen to pass through while retaining other gases.
Note: PSA technology is commonly used in industrial applications, offering higher purity nitrogen and lower energy consumption compared to membrane technology.
The generated nitrogen can be used in various industries, such as:
Industry | Application |
---|---|
Food & Beverage | Packaging and preservation of food products |
Pharmaceuticals | Inert atmosphere for sensitive processes |
Electronics | Providing a clean and controlled environment for manufacturing |
Understanding the Basic Principle of Nitrogen Generation
Nitrogen generators operate by separating nitrogen from the air, which consists primarily of oxygen (21%) and nitrogen (78%). The primary method for nitrogen extraction is through two main techniques: Pressure Swing Adsorption (PSA) and Membrane Separation. Each method exploits different properties of gases to efficiently separate nitrogen, which can then be used in various industrial applications.
In a PSA system, air is passed through adsorbent materials that selectively capture oxygen, allowing nitrogen to flow through. The process involves alternating pressure cycles that release the trapped oxygen, regenerating the adsorbent for continuous operation. Membrane systems, on the other hand, utilize semi-permeable membranes that allow faster diffusion of oxygen over nitrogen, separating the gases based on their molecular size and permeability.
Pressure Swing Adsorption (PSA) System
- Air Intake: Ambient air is drawn into the system.
- Adsorption: The air is passed through a bed of adsorbent material, which captures oxygen.
- Pressure Adjustment: Pressure is varied to release the adsorbed oxygen.
- Product Nitrogen: The nitrogen is separated and collected for use.
Membrane Separation System
- Air Intake: Compressed air is introduced into the system.
- Membrane Filtration: The air passes through membranes that selectively allow oxygen to pass more easily than nitrogen.
- Nitrogen Collection: The nitrogen gas is collected on the other side of the membrane.
Important: Both PSA and membrane systems offer efficient nitrogen generation, but PSA generally produces higher purity nitrogen, while membrane systems are more compact and cost-effective for lower purity requirements.
Comparison of PSA and Membrane Systems
Feature | PSA System | Membrane System |
---|---|---|
Purity | Higher | Lower |
Cost | Higher initial cost | Lower initial cost |
Efficiency | Very efficient for high purity | Efficient for medium or low purity |
Maintenance | Requires periodic maintenance | Low maintenance |
Key Components of a Nitrogen Generator System
A nitrogen generator system operates through a series of components that work together to produce nitrogen gas from the air. These components are designed to ensure high purity and efficient separation of nitrogen from oxygen and other gases. The core elements of a nitrogen generator system include filtration units, air compressors, separation modules, and nitrogen storage tanks. Each of these parts plays a crucial role in the overall performance of the system, from intake to final gas output.
Understanding the key components is essential for maintaining and optimizing the performance of nitrogen generators, particularly in industrial applications such as food packaging, chemical production, and electronics manufacturing. Below are the primary components that make up a typical nitrogen generator system.
Primary Components
- Compressor: Pressurizes atmospheric air for subsequent filtration and separation.
- Pre-Filters: Remove impurities such as dust, moisture, and oil from the compressed air.
- Separation Modules: Use technologies like Pressure Swing Adsorption (PSA) or Membrane Separation to extract nitrogen.
- Storage Tank: Stores the nitrogen gas for later use, maintaining consistent pressure and flow.
- Control System: Monitors and regulates system operation, ensuring optimal performance and safety.
Function of Each Component
- Compressor: Draws in atmospheric air and increases its pressure, sending it to the filters and separation units.
- Pre-Filters: Prevent contaminants from reaching the separation modules, improving system efficiency and lifespan.
- Separation Modules: These use specific adsorbent materials or membranes to separate nitrogen from oxygen and trace gases. PSA is the most common method used in many nitrogen generators.
- Storage Tank: Once the nitrogen is separated, it is stored in a tank that ensures a steady supply of nitrogen gas when required.
- Control System: Ensures proper functioning by adjusting the flow rates, pressure, and temperature in real-time based on system feedback.
“Each of these components is integral to ensuring that the nitrogen produced is of the desired purity and consistency for specific industrial processes.”
Component Comparison
Component | Function | Technology Used |
---|---|---|
Compressor | Pressurizes the intake air for filtration and separation | Mechanical compression |
Pre-Filters | Removes dust, oil, and moisture from air | Filtration technology |
Separation Modules | Separates nitrogen from oxygen and other gases | PSA, Membrane Separation |
Storage Tank | Stores nitrogen at desired pressure for consistent supply | Tank storage technology |
Control System | Regulates operational parameters for optimal performance | Automated control systems |
How PSA Technology Powers Nitrogen Production
Pressure Swing Adsorption (PSA) technology is widely used in nitrogen generation systems due to its ability to separate nitrogen from air efficiently. This method leverages the differences in adsorption properties between nitrogen and other gases present in the atmosphere, such as oxygen, carbon dioxide, and argon. By applying varying pressures, PSA can selectively adsorb certain gases and allow others to pass through, resulting in high-purity nitrogen. This process is both cost-effective and energy-efficient, making it the preferred choice for industrial applications.
The core of the PSA system involves two or more adsorption towers filled with materials known as adsorbents, typically zeolite or activated carbon. These materials selectively trap oxygen and other gases at high pressure while allowing nitrogen to pass through. Once the adsorbent becomes saturated, the pressure is reduced, releasing the adsorbed gases and allowing the cycle to repeat. This continuous process ensures a steady supply of nitrogen at the required purity level.
PSA Process Overview
- Air Intake: Ambient air is compressed and introduced into the adsorption tower.
- Adsorption Phase: At high pressure, oxygen and other gases are adsorbed by the zeolite material, while nitrogen passes through.
- Pressure Swing: The pressure in the tower is reduced, releasing the adsorbed gases and allowing the nitrogen to be collected.
- Regeneration: The adsorbent material is regenerated by decreasing the pressure, and the system is ready for the next cycle.
PSA technology is highly effective for producing nitrogen on-demand, with purity levels typically ranging from 95% to 99.99%, depending on the configuration.
Advantages of PSA Nitrogen Generation
Advantage | Description |
---|---|
Energy Efficiency | The system uses less energy compared to traditional nitrogen production methods, such as cryogenic distillation. |
Cost-Effective | PSA systems are relatively low-cost to install and maintain, making them a viable option for many industries. |
Scalability | PSA units can be easily scaled up or down based on nitrogen demand, making them adaptable to various applications. |
Advantages of Using a Nitrogen Generator Over Compressed Air
When it comes to supplying nitrogen for industrial or laboratory applications, nitrogen generators offer several clear benefits over traditional compressed air systems. While both systems provide gases for various uses, nitrogen generators can deliver a higher degree of purity and efficiency, making them a more reliable option for many industries.
Compressed air systems often deliver a mixture of gases, including oxygen and moisture, which can affect the quality of the output in critical applications. In contrast, nitrogen generators are designed to separate nitrogen from the air, producing a more consistent and pure nitrogen supply that meets specific requirements.
Key Benefits of Nitrogen Generators
- Higher Purity: Nitrogen generators can produce nitrogen with a purity level of up to 99.999%, which is significantly higher than that of compressed air systems.
- Cost-Effectiveness: Once installed, nitrogen generators provide an on-demand nitrogen supply, eliminating the need for costly nitrogen tanks or reliance on third-party suppliers.
- Reduced Maintenance: Unlike compressed air systems, which require regular checks and maintenance, nitrogen generators are more straightforward to maintain, reducing downtime and operational costs.
Comparison of Nitrogen Generators vs. Compressed Air Systems
Feature | Nitrogen Generator | Compressed Air |
---|---|---|
Purity | Up to 99.999% | Varies, typically around 21% oxygen |
Operational Costs | Low, only electricity and occasional maintenance | High, includes costs of compressed air equipment and storage tanks |
Maintenance | Minimal, with occasional filter changes | High, requires frequent monitoring and maintenance |
"The ability to generate nitrogen on-site ensures that industries can consistently meet their requirements, without the unpredictability of supply disruptions or the high costs of purchasing nitrogen gas."
Steps Involved in Setting Up a Nitrogen Generation System
Installing a nitrogen generator system requires careful planning and execution to ensure optimal performance. The setup process involves several critical stages, including site preparation, equipment installation, and system integration. Proper adherence to these steps guarantees that the generator operates efficiently, providing consistent nitrogen output as required by the application.
Before proceeding with the installation, it’s essential to assess the site conditions, such as available space, ventilation, and electrical supply. Proper evaluation helps prevent delays and operational issues during installation.
1. Site Preparation and Planning
- Evaluate space requirements and ensure adequate ventilation for the equipment.
- Check the electrical infrastructure for compatibility with the generator’s power needs.
- Prepare the necessary plumbing and piping for the nitrogen distribution network.
2. Installation of Equipment
- Position the nitrogen generator at the prepared location, ensuring access for maintenance.
- Connect the compressor and air intake system to the generator unit.
- Install the nitrogen separation unit, which typically uses Pressure Swing Adsorption (PSA) or Membrane technology.
3. System Integration and Testing
Once the physical components are installed, the system must be integrated with the existing infrastructure. This includes connecting the nitrogen generator to the control system and verifying the safety mechanisms.
Proper testing and calibration of the system are essential before full operation, as this ensures the generator operates within the specified parameters for nitrogen purity and pressure.
4. Final Inspection and Calibration
- Conduct a thorough inspection of all connections and electrical systems.
- Test the generator's output to confirm the nitrogen purity level and flow rate.
- Adjust the system settings based on the desired specifications.
5. Ongoing Monitoring and Maintenance
After the system is operational, continuous monitoring is essential to ensure optimal performance. Regular maintenance checks should be scheduled to avoid downtime and costly repairs.
Maintenance Task | Frequency |
---|---|
Filter Replacement | Every 6 months |
Compressor Check | Every 3 months |
System Calibration | Annually |
How to Select the Ideal Nitrogen Generator for Your Company
Choosing the right nitrogen generation system for your business involves understanding the specific requirements of your operation and matching them with the capabilities of available systems. Different types of nitrogen generators cater to different production scales and purity needs, so identifying your exact requirements is key. Factors such as flow rate, purity, and operational environment play crucial roles in determining which system will best suit your needs.
Before making a decision, it’s important to evaluate how much nitrogen you need, the level of purity required, and the available space for installation. Understanding these variables will ensure you make an informed choice that supports the efficiency and cost-effectiveness of your business.
Key Factors to Consider
- Production Volume: The required flow rate of nitrogen is directly related to the volume of gas your business needs. Larger operations may require a higher capacity system.
- Purity Requirements: Different applications, such as food packaging or electronics manufacturing, may require varying levels of nitrogen purity. Ensure the generator can meet these standards.
- Energy Efficiency: Some nitrogen generators are designed to use less energy, which can lead to significant long-term savings in operational costs.
- Maintenance and Support: Consider the maintenance needs of the system and the availability of support services to minimize downtime.
Steps to Choose the Right System
- Assess your nitrogen demand: Calculate the flow rate and purity levels you need for your specific application.
- Compare system types: Decide between Pressure Swing Adsorption (PSA) or Membrane Nitrogen Generators based on the purity and flow rate required.
- Evaluate total cost of ownership: Factor in initial installation, maintenance, and energy consumption.
- Check system certifications: Ensure that the system meets industry standards and regulations relevant to your business.
Comparison Table
System Type | Flow Rate | Purity Level | Maintenance |
---|---|---|---|
PSA Nitrogen Generator | High | 99.9%+ | Moderate |
Membrane Nitrogen Generator | Medium | 95-99% | Low |
For businesses with fluctuating nitrogen needs, a modular system that allows easy scalability might be a cost-effective option in the long term.
Maintenance and Troubleshooting of Nitrogen Generation Systems
Proper upkeep of a nitrogen generator system is essential to ensure its efficient operation and prolonged lifespan. Regular maintenance helps prevent system failures and costly repairs. Monitoring key components such as compressors, filters, and membranes is crucial to avoid unexpected breakdowns. Early identification of potential issues can significantly reduce downtime and operational costs. Additionally, adhering to the manufacturer's guidelines ensures that each part operates within its optimal parameters.
Routine inspections and maintenance tasks include checking the system for leaks, replacing worn-out filters, and verifying the functionality of sensors. Troubleshooting common issues involves understanding how different parts of the system interact, as well as recognizing the signs of malfunctions. Efficient troubleshooting requires both technical knowledge and access to the right diagnostic tools.
Common Maintenance Tasks
- Inspecting and replacing filters at regular intervals
- Monitoring the system’s air intake and exhaust valves
- Cleaning and lubricating moving parts to prevent wear
- Checking the integrity of seals and gaskets to prevent leaks
- Testing system pressure and flow rates for consistency
Typical Troubleshooting Steps
- Check for air compressor malfunctions, such as improper pressure or noise.
- Inspect the membrane for damage or clogging.
- Verify sensor readings and recalibrate if necessary.
- Examine the nitrogen purity level and adjust the settings as needed.
- Look for any blockages or leaks in the piping system.
Key Components to Monitor
Component | Common Issue | Solution |
---|---|---|
Compressor | Reduced pressure or noise | Check for leaks, replace worn parts, and lubricate as necessary |
Membrane | Clogging or reduced performance | Clean or replace membrane |
Filters | Blockage or contamination | Replace filters regularly |
Sensors | Incorrect readings | Recalibrate or replace faulty sensors |
Important: Always follow the manufacturer’s recommended service intervals and procedures for optimal performance.
Cost Comparison: Nitrogen Generation System vs. Cylinder Delivery
When evaluating the expenses of obtaining nitrogen, two main options arise: investing in a nitrogen generation system or relying on cylinder delivery. Each method carries its own cost structure, which can significantly impact long-term operations. A detailed understanding of the cost factors involved can help businesses determine the most economical solution based on their specific requirements.
A nitrogen generator system typically requires an upfront investment, but it can significantly reduce ongoing costs compared to regular nitrogen cylinder deliveries. The key factors influencing this comparison are initial setup costs, maintenance, and the frequency of nitrogen consumption. On the other hand, cylinder delivery involves recurring transportation and rental fees, with fluctuations based on demand and usage volumes.
Initial Investment
The initial setup costs for a nitrogen generator system include purchasing the equipment, installation, and potential modifications to the facility. These expenses are typically higher compared to the initial cost of nitrogen cylinder delivery, which usually only involves rental fees for cylinders.
- Nitrogen Generator: Initial purchase, installation, and facility modifications
- Cylinder Delivery: Rental fees for cylinders and transportation costs
Operational Costs
When considering ongoing expenses, nitrogen generators offer a more predictable cost structure, where the primary costs are electricity, maintenance, and replacement parts. Cylinder deliveries, however, include costs for regular refills, transportation, and cylinder rentals, which can vary greatly depending on usage patterns.
- Nitrogen Generator: Electricity consumption, maintenance, and replacement parts
- Cylinder Delivery: Refills, transportation, and cylinder rental fees
Long-Term Cost Comparison
Factor | Nitrogen Generator | Nitrogen Cylinder Delivery |
---|---|---|
Initial Setup | High | Low |
Maintenance | Low | None |
Refill & Delivery | None | Frequent |
Ongoing Costs | Electricity, parts | Rent, transport |
Nitrogen generation systems typically prove to be more cost-effective in the long run, particularly for facilities with high nitrogen consumption or continuous use. Cylinder delivery, while lower in initial investment, incurs high operational costs over time.