Nitro-v Steel Review
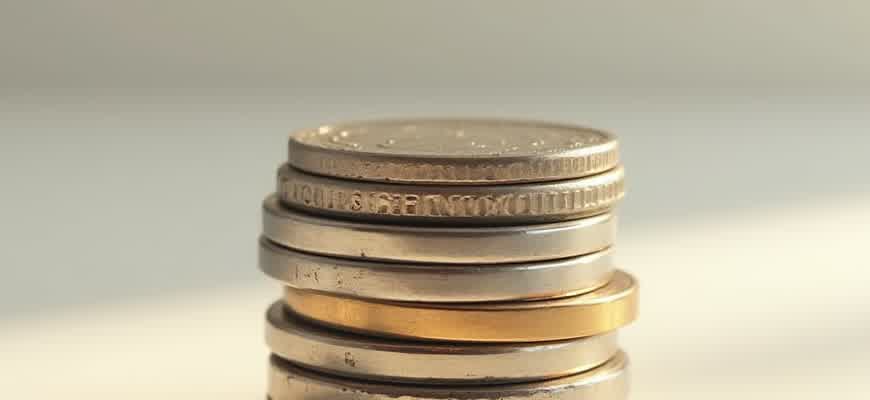
The Nitro-V steel is a high-performance alloy, designed to offer superior edge retention, corrosion resistance, and ease of sharpening. It has rapidly gained popularity among knife enthusiasts and manufacturers due to its balanced properties. This review explores its key features and evaluates how it compares to other well-known steels.
Key Properties of Nitro-V Steel:
- High corrosion resistance due to the inclusion of chromium and nitrogen
- Excellent edge retention, suitable for everyday use and outdoor activities
- Ease of sharpening, even for users with basic honing skills
- Good toughness, making it resistant to chipping under normal conditions
"Nitro-V steel is often favored for its balanced performance, making it ideal for both kitchen knives and field tools."
Comparison Table:
Steel Type | Edge Retention | Corrosion Resistance | Sharpening Ease |
---|---|---|---|
Nitro-V | Excellent | High | Easy |
S30V | Very Good | Good | Moderate |
VG-10 | Good | Good | Easy |
How Nitro-V Steel Enhances Blade Durability and Edge Retention
Nitro-V steel has become highly regarded in the knife-making industry due to its superior properties in terms of blade durability and edge retention. This stainless steel alloy is designed to withstand heavy use while maintaining a sharp edge for longer periods. It incorporates nitrogen into its composition, which significantly improves its toughness and overall performance, making it a top choice for high-quality blades.
One of the key features of Nitro-V steel is its ability to retain a fine edge for extended periods. This is largely due to the steel's high chromium content, which provides excellent corrosion resistance, and the addition of vanadium and nitrogen, which enhance hardness and edge stability. As a result, knives made with Nitro-V steel can handle tough tasks while maintaining sharpness much longer than traditional steels.
Key Factors Contributing to Durability and Edge Retention
- Chromium Content: High levels of chromium improve corrosion resistance, helping to prevent rust and deterioration from exposure to moisture.
- Vanadium Inclusion: Vanadium helps in maintaining edge retention by refining the grain structure, ensuring the steel remains resilient under pressure.
- Nitrogen Element: Nitrogen increases hardness and provides better wear resistance, contributing to a tougher edge that resists chipping and blunting.
Nitro-V steel is known for its ability to hold an edge for longer periods, outperforming many other stainless steels in this area.
In comparison to other premium steels, Nitro-V stands out due to its exceptional balance of toughness and edge retention. While it may not reach the extreme hardness of steels like CPM S30V, Nitro-V is still able to deliver a blade that resists wear and tear while maintaining a sharp cutting surface. Below is a table comparing the key attributes of Nitro-V steel against a few other popular steels used in knife-making:
Steel Type | Hardness (HRC) | Edge Retention | Corrosion Resistance |
---|---|---|---|
Nitro-V | 58-60 | Excellent | Excellent |
S30V | 58-60 | Very Good | Good |
VG-10 | 59-61 | Good | Very Good |
The balanced combination of edge retention and corrosion resistance makes Nitro-V a highly versatile steel choice for many outdoor and utility knives.
Understanding the Composition of Nitro-v Steel and Its Impact on Performance
Nitro-v steel is a high-performance alloy known for its exceptional durability, corrosion resistance, and edge retention. This steel is crafted with specific elements that contribute to its high toughness and versatility. Its composition is carefully engineered to balance wear resistance and strength, making it an ideal choice for various applications, including knives, tools, and cutting instruments.
The performance of Nitro-v steel is heavily influenced by its alloying elements. These components work in harmony to provide an optimal balance of hardness, toughness, and corrosion resistance. A detailed breakdown of the composition reveals the role of each element in enhancing the material's properties.
Key Components of Nitro-v Steel
- Carbon (C): Improves hardness and wear resistance, allowing the steel to hold a sharp edge for a longer period.
- Chromium (Cr): Increases corrosion resistance and hardness, while also enhancing the steel's overall durability.
- Vanadium (V): Refines the grain structure, contributing to increased toughness and strength while improving wear resistance.
- Molybdenum (Mo): Adds to the steel's toughness and resistance to high temperatures, preventing softening during extended use.
- Niobium (Nb): Enhances strength and wear resistance by stabilizing the steel’s structure, making it more resistant to wear over time.
Nitro-v steel's composition allows for a fine balance between hardness and toughness, offering excellent edge retention without sacrificing strength under heavy use.
Performance Characteristics of Nitro-v Steel
- Edge Retention: Due to the high carbon content, Nitro-v steel is known for its ability to maintain a sharp edge for extended periods.
- Corrosion Resistance: Chromium and other alloying elements protect the steel from rust and oxidation, ensuring longevity and reliability in harsh environments.
- Toughness: The combination of vanadium, molybdenum, and niobium contributes to the material’s toughness, making it resistant to chipping and cracking under pressure.
Comparing Nitro-v Steel to Other Alloys
Property | Nitro-v Steel | CPM-S30V |
---|---|---|
Edge Retention | Excellent | Very Good |
Corrosion Resistance | Good | Excellent |
Toughness | Good | Excellent |
Wear Resistance | Very Good | Good |
Comparing Nitro-V Steel to Other Popular Knife Steel Alloys
Nitro-V steel has gained popularity in the world of knives due to its unique combination of performance features. It stands out for its corrosion resistance, edge retention, and toughness. When comparing Nitro-V to other common knife steels, it’s essential to evaluate several key characteristics like hardness, wear resistance, and ease of sharpening, as these factors influence overall blade performance in various environments.
In this comparison, we will examine Nitro-V against several widely recognized steel alloys like VG-10, S30V, and 154CM. Each of these steels offers specific advantages, but Nitro-V has distinct qualities that make it an appealing choice for knife enthusiasts and professionals alike. Below is a detailed look at how Nitro-V stacks up against its competitors.
Key Steel Comparison
Steel Type | Corrosion Resistance | Edge Retention | Toughness | Sharpening Ease |
---|---|---|---|---|
Nitro-V | High | Good | Moderate | Moderate |
VG-10 | High | Excellent | Moderate | Easy |
S30V | Moderate | Excellent | Good | Hard |
154CM | Moderate | Good | High | Easy |
Nitro-V steel excels in its corrosion resistance, outperforming many other steels, but it does not offer the same level of edge retention as steels like VG-10 or S30V. However, its combination of factors makes it an ideal choice for users who require a balanced performance steel for daily tasks.
Advantages and Disadvantages
- Advantages of Nitro-V:
- Great corrosion resistance, especially in humid and salty environments.
- Decent edge retention and sharpening ease for those who prioritize maintenance.
- Cost-effective compared to premium steels like S30V and VG-10.
- Disadvantages of Nitro-V:
- Edge retention is not as long-lasting as higher-end steels like S30V.
- May not perform as well under extreme impact situations as steels with higher toughness ratings.
Why Nitro-V Steel is Perfect for Outdoor and Tactical Knives
When selecting a blade for outdoor and tactical use, it's crucial to consider the steel's composition, edge retention, and durability. Nitro-V steel has gained significant attention for its impressive balance of these characteristics, making it a prime choice for high-performance knives. This modern stainless steel combines the best qualities of both carbon and stainless steels, offering excellent corrosion resistance without sacrificing sharpness or toughness.
One of the key advantages of Nitro-V is its ability to maintain a sharp edge for longer periods while being relatively easy to sharpen compared to other high-performance steels. For outdoor and tactical knives, this is a critical factor, as users often rely on their blades for extended periods without access to proper sharpening tools.
Advantages of Nitro-V Steel
- Corrosion Resistance: Nitro-V steel boasts superior rust resistance, a crucial feature for knives exposed to moisture, salt, and extreme weather conditions.
- Edge Retention: The alloy is designed to hold a sharp edge longer, reducing the frequency of sharpening, which is ideal for heavy use in outdoor environments.
- Ease of Maintenance: Despite its toughness, Nitro-V is relatively easy to sharpen and maintain, even in field conditions.
- Durability: It offers a high level of toughness, preventing chipping or breaking during high-stress tasks like chopping or batoning.
Comparison of Nitro-V Steel with Other Common Knife Steels
Steel Type | Corrosion Resistance | Edge Retention | Toughness | Ease of Sharpening |
---|---|---|---|---|
Nitro-V | High | Good | Excellent | Easy |
154CM | Moderate | Good | Good | Moderate |
S30V | High | Excellent | Good | Hard to sharpen |
Nitro-V steel’s balanced properties make it ideal for outdoor knives that need to withstand harsh environments while delivering high performance during long-term use.
Corrosion Resistance of Nitro-V Steel: A Deep Dive
Nitro-V steel, known for its high wear resistance and toughness, is also notable for its corrosion resistance properties. Unlike traditional steels, Nitro-V benefits from the incorporation of nitrogen during its production, enhancing its overall resistance to environmental factors like moisture and salts. This steel has been engineered to provide a balance between toughness and the ability to resist rust and corrosion under harsh conditions.
When evaluating corrosion resistance, it's essential to consider several factors, including the alloy composition and the type of protective coatings applied. Nitro-V steel, while not entirely immune to corrosion, exhibits significantly improved resistance when compared to other high-carbon steels. This is due to its higher concentration of chromium and vanadium, which help to form a more stable oxide layer on the surface, providing a barrier against corrosive elements.
Key Features Contributing to Corrosion Resistance
- Chromium Content: The presence of chromium in Nitro-V steel enhances its resistance to oxidation, which is the primary cause of corrosion.
- Vanadium's Role: Vanadium strengthens the steel's overall structure, making it more resistant to both wear and corrosion over time.
- Nitrogen Addition: Nitrogen improves the steel's ability to resist pitting corrosion, a common issue in many stainless steels.
While Nitro-V steel offers superior corrosion resistance compared to many high-carbon steels, proper maintenance and protective coatings are still recommended in environments with extreme corrosive conditions.
Corrosion Resistance in Different Environments
- Marine Environments: Nitro-V steel shows promising results in marine applications due to its ability to resist chloride-induced corrosion.
- Industrial Settings: In environments where exposure to chemicals and moisture is frequent, Nitro-V performs well, although coatings may be necessary for prolonged exposure.
- Outdoor Usage: The steel maintains its integrity even in variable weather conditions, offering resistance to rain, snow, and humidity.
Corrosion Resistance Comparison
Steel Type | Corrosion Resistance | Applications |
---|---|---|
Nitro-V Steel | High corrosion resistance, especially in marine and industrial environments | Knives, tools, outdoor equipment |
Stainless Steel | Excellent corrosion resistance but can still pit in high chloride environments | Marine, kitchen, medical instruments |
Carbon Steel | Low corrosion resistance, prone to rust without coatings | Construction, automotive |
Heat Treatment Techniques for Optimizing Nitro-v Steel Performance
Nitro-v steel is a high-performance alloy, renowned for its excellent wear resistance and toughness. Achieving the best properties of Nitro-v steel requires careful heat treatment techniques. These processes help to maximize the steel’s hardness, wear resistance, and overall mechanical properties, which are crucial for applications such as knives, tools, and industrial equipment. Below, we’ll cover some of the most important heat treatment techniques for optimizing Nitro-v steel's performance.
One of the key aspects of heat treatment for Nitro-v steel is the use of proper austenitizing and quenching procedures. These processes influence the steel's microstructure, which in turn affects its final hardness and resistance to wear. The right temperature and cooling rate must be carefully selected to achieve optimal results.
Austenitizing and Quenching
- Austenitizing - Heating Nitro-v steel to the appropriate temperature, typically between 1020°C and 1050°C, allows the steel to reach its austenitic phase. This is crucial for maximizing the steel’s hardness potential.
- Quenching - Rapid cooling using oil or air ensures the formation of a martensitic structure, which provides high hardness and strength. The cooling medium must be chosen carefully to avoid warping or cracking.
Tempering
After quenching, the steel is typically tempered to relieve internal stresses and reduce brittleness. This step enhances toughness without sacrificing too much hardness.
- Heat to 150°C to 200°C for 1-2 hours for optimal balance between hardness and toughness.
- Ensure a uniform temperature distribution during tempering to avoid uneven properties.
Tempering is essential to avoid brittle failure, ensuring the steel maintains strength and flexibility for practical use.
Table: Heat Treatment Process for Nitro-v Steel
Process | Temperature Range | Duration |
---|---|---|
Austenitizing | 1020°C - 1050°C | 1 hour |
Quenching | Rapid Cooling | Instantaneous |
Tempering | 150°C - 200°C | 1-2 hours |
Real-World User Feedback on Nitro-V Steel: What You Need to Know
Nitro-V steel has become a popular choice for various knives and tools due to its combination of durability, corrosion resistance, and edge retention. However, real-world feedback from users provides valuable insights into how this material performs under different conditions. From outdoor enthusiasts to professional chefs, the steel has been tested in diverse environments, leading to a more complete understanding of its strengths and weaknesses.
One common observation is the balance between toughness and ease of sharpening. Users note that while Nitro-V can hold an edge for a long time, it may require a bit more effort when it comes time to sharpen. This feedback is especially important for those who rely on their tools in demanding situations, as sharpening ease can be a deciding factor in choosing a material. Below, we’ll break down some of the key takeaways from real-world experiences with Nitro-V steel.
Key Points from User Experiences
- Edge Retention: Users report that Nitro-V steel maintains its edge well under heavy use, even after prolonged exposure to abrasive materials.
- Corrosion Resistance: Many users have praised the steel’s resistance to rust and staining, even in harsh, wet conditions.
- Sharpening: While edge retention is excellent, some users have found Nitro-V slightly harder to sharpen compared to other high-performance steels.
- Toughness: The steel is durable and resistant to chipping, making it ideal for users who engage in tough, high-impact tasks.
Strengths and Weaknesses in Practical Use
"In my experience, Nitro-V provides an excellent balance between edge retention and ease of maintenance. However, it does take more time to sharpen compared to my previous knives." – Professional Chef
Overall, Nitro-V steel seems to strike a good balance between performance and maintenance. Below is a table summarizing the general user feedback on its key properties:
Property | User Rating |
---|---|
Edge Retention | 8/10 |
Corrosion Resistance | 9/10 |
Ease of Sharpening | 7/10 |
Toughness | 8/10 |
How to Care for and Sharpen Nitro-V Steel Blades
Nitro-V steel is known for its excellent edge retention, corrosion resistance, and ease of maintenance, making it a popular choice among knife enthusiasts. However, to keep your Nitro-V knives in top condition, regular care and sharpening are essential. Proper maintenance ensures your blade remains sharp and performs optimally for years.
Sharpening and maintaining Nitro-V steel is straightforward, but understanding the right tools and techniques is key to preserving its integrity. Below are some tips for keeping your knife sharp and in excellent working condition.
Sharpening Nitro-V Steel
To sharpen Nitro-V blades, it’s important to follow these steps to maintain the quality of the edge:
- Choose the right sharpening tool: Use diamond stones, ceramic rods, or sharpening systems specifically designed for high-quality steel like Nitro-V.
- Maintain the correct angle: Keep the edge angle between 20 to 25 degrees for optimal sharpness and durability.
- Use light pressure: Apply light, consistent pressure when sharpening to avoid removing too much material.
- Use fine grit for finishing: After coarse sharpening, finish with a finer grit to refine the edge.
Maintenance Tips for Nitro-V Blades
In addition to sharpening, keeping your Nitro-V knife well-maintained is essential for longevity. Regular care will prevent rusting and damage:
- Clean after each use: Wipe the blade with a damp cloth and dry thoroughly to avoid moisture buildup.
- Apply oil: Regularly apply a light coating of oil, such as mineral oil or food-safe oils, to prevent rust.
- Store properly: Store your knife in a dry place, away from humidity, and preferably in a protective sheath.
Important Care Information
Always use sharpening tools that are appropriate for high-performance steels like Nitro-V. Using improper sharpening methods can lead to edge damage or an uneven bevel.
Comparison of Sharpening Tools
Tool | Pros | Cons |
---|---|---|
Diamond Stone | Fast, effective, works on high-hardness steel | Can be rough on softer steels, expensive |
Ceramic Rod | Gentle, great for finishing | Slower than diamond stones, may not work well on very dull blades |
Sharpening System | Consistent results, adjustable angle guides | More expensive, can be bulky |