Convert Nitro Rc to Electric
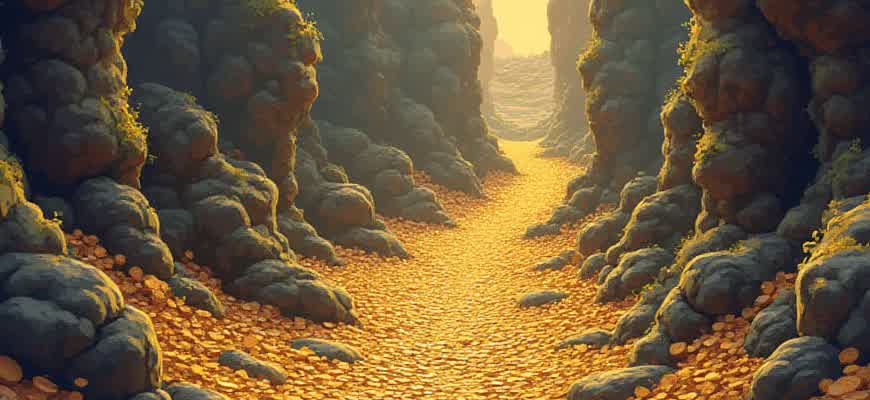
Converting a nitro-powered RC car to an electric system can be an exciting challenge for hobbyists looking to explore the benefits of electric propulsion. This process involves replacing the internal combustion engine with an electric motor and adding the necessary components such as an ESC (Electronic Speed Controller) and battery pack. The switch offers cleaner operation, less maintenance, and often greater performance control. However, it requires careful planning and the right components to ensure compatibility and performance.
Key Steps in the Conversion Process:
- Remove the Nitro Engine: Carefully disconnect the nitro engine from the chassis, making sure to preserve any parts that may be useful for the conversion.
- Choose the Electric Motor: Select a motor with appropriate power output for your car’s size and weight.
- Install the ESC: The ESC controls the power from the battery to the motor. Ensure it is compatible with the chosen motor and voltage system.
- Install the Battery Pack: Choose a battery with suitable voltage and capacity for the motor. LiPo (Lithium Polymer) batteries are commonly used in electric RC cars for their high energy density and light weight.
Important Note: Ensure all components, including the motor and ESC, are designed to handle the same voltage levels to avoid damage.
In some cases, the existing chassis may need modification to fit the new electric components. The motor mount and battery tray are often the most common areas requiring adjustments. Additionally, weight distribution is crucial for maintaining performance and handling, as the placement of the motor and battery can affect the car's balance.
Comparison of Components:
Component | Nitro System | Electric System |
---|---|---|
Power Source | Fuel (Nitromethane) | Battery (LiPo) |
Maintenance | High (Fuel, engine parts, tuning) | Low (Occasional battery care) |
Noise | High | Low |
Performance | Variable, engine tuning | Consistent, more control |
How to Convert Your Nitro RC to Electric: A Step-by-Step Guide
Converting a Nitro RC car to an electric-powered one can significantly improve its performance, reduce maintenance time, and provide a quieter experience. This process involves removing the internal combustion engine and replacing it with an electric motor, battery pack, and the necessary electronic components. By following the right steps, you can successfully complete this conversion, giving your RC car a new life with electric power.
Before starting, make sure you have all the tools and parts required for the conversion. A typical Nitro-to-electric conversion will require a new motor mount, electric motor, battery pack, ESC (electronic speed control), and possibly a new servo. This guide will walk you through the essential steps to complete the conversion.
Step-by-Step Conversion Process
- Remove the Nitro Engine: Start by carefully disassembling your RC car and removing the Nitro engine. Be sure to disconnect any fuel lines and exhaust pipes. This step is essential as it clears the space for your new electric components.
- Install the Motor Mount: You will need a motor mount that fits your specific RC chassis. The mount must be securely attached to the chassis to hold the electric motor in place. Ensure that the motor shaft aligns with the pinion gear.
- Fit the Electric Motor: Choose a suitable electric motor based on the type of RC car and desired performance. Install it onto the motor mount and ensure it’s tightly secured. Make sure the motor is properly aligned with the pinion gear to avoid misalignment.
- Connect the ESC and Battery: Install the ESC in a convenient location on the chassis. Connect it to the motor and the battery pack, ensuring that the ESC is compatible with the motor and voltage requirements. The battery pack should be securely mounted to prevent any shifting during operation.
- Install New Electronics: Replace any necessary electronics, such as the servo or receiver, to work with the electric system. This ensures smoother control and compatibility between components.
- Check and Test: Before testing the RC car, double-check all connections and components to ensure they are secure and correctly installed. Perform a test run to ensure the motor, ESC, and other electronics are functioning properly.
Important Considerations
Make sure to choose a motor and battery that match the scale and weight of your RC car. Incorrectly sized components can lead to overheating or reduced performance.
Conversion Kit Options
Part | Options | Notes |
---|---|---|
Motor | Brushless, Brushed | Brushless motors are more efficient and provide higher speeds. |
ESC | Waterproof, Standard | Waterproof ESCs are recommended for off-road RC cars. |
Battery | Lipo, NiMH | Lipo batteries are lighter and offer better performance. |
Always check compatibility between your motor, ESC, and battery pack before purchasing to ensure optimal performance and safety.
Selecting the Right Electric Motor for Your Nitro RC Conversion
When converting a Nitro RC car to an electric system, choosing the appropriate motor is crucial for optimal performance. The motor determines the power, speed, and efficiency of your vehicle. There are a variety of electric motors available, each designed for different applications, so it's essential to understand their specifications to match your needs.
The choice of motor will depend on the type of performance you're aiming for, the weight of your car, and the driving conditions. Whether you're aiming for speed, endurance, or a balance of both, the right motor can make a significant difference in the overall driving experience.
Types of Electric Motors
- Brushed Motors: Simple and cost-effective, but less efficient and wear out faster than brushless motors.
- Brushless Motors: More efficient, durable, and provide more power for high-performance needs, but at a higher cost.
- Sensorless Motors: Common in budget setups, offering good performance with simpler control, but can be less smooth at low speeds.
- Sensored Motors: Provide smoother acceleration and better control, especially at low speeds, ideal for precise driving.
Factors to Consider When Selecting a Motor
- Motor KV Rating: The KV rating defines how many revolutions per minute (RPM) the motor can achieve per volt. A higher KV means more speed but less torque, whereas a lower KV provides more torque but less speed.
- Motor Size and Weight: Ensure that the motor size fits within your car's chassis and that it doesn't add too much weight, which could affect the overall handling.
- Voltage Compatibility: Verify that the motor is compatible with your battery's voltage to ensure efficient power delivery and prevent overheating.
It is important to select a motor that not only fits physically but also aligns with the power demands of your RC vehicle. A motor that's too powerful can strain other components, while one that's too weak will limit the car's performance.
Motor Comparison Table
Motor Type | Efficiency | Power Output | Cost |
---|---|---|---|
Brushed | Low | Moderate | Low |
Brushless | High | High | High |
Sensorless | Moderate | High | Moderate |
Sensored | High | High | High |
Choosing the Right Battery Type and Capacity for Your Electric RC
When converting a nitro RC to electric, selecting the correct battery type and capacity is essential for optimal performance. The battery not only determines how long your RC can run but also how much power it can generate. There are several factors to consider, such as voltage, capacity, and the type of battery chemistry, which directly impact the speed, efficiency, and runtime of the vehicle.
Choosing the right battery involves understanding your RC car's needs and matching those to the battery's specifications. Different types of batteries offer unique advantages, and understanding these differences is crucial for maximizing performance while maintaining safety and longevity.
Battery Types and Their Advantages
- Lipo (Lithium Polymer) - Popular for its light weight and high energy density, providing more power with less weight.
- NiMH (Nickel-Metal Hydride) - Known for being safer and offering more stability, although heavier than LiPo batteries.
- LiFe (Lithium Iron Phosphate) - Offers longer life cycles and better safety characteristics compared to standard LiPo batteries.
Battery Capacity and Voltage
Battery capacity is measured in mAh (milliampere-hours), indicating how much energy the battery can store. A higher mAh rating means longer runtime, but it can also add weight to the vehicle.
- Voltage (V): A higher voltage results in more power and speed but also increases stress on the motor and ESC. Typical voltage configurations are 2S (7.4V), 3S (11.1V), and 4S (14.8V).
- Capacity (mAh): A higher mAh rating provides longer usage time. However, larger capacities often result in heavier batteries, which can impact handling and speed.
Note: The balance between voltage and capacity is key. If you select a battery with too high of a voltage, you may exceed the motor's and ESC's limits, causing overheating or damage.
Choosing the Right Battery for Your RC
Battery Type | Voltage (V) | Capacity (mAh) | Pros | Cons |
---|---|---|---|---|
Lipo | 7.4V, 11.1V, 14.8V | 1500mAh - 5000mAh+ | Lightweight, High power, Long runtime | More expensive, Sensitive to overcharge/overdischarge |
NiMH | 7.2V | 3000mAh - 7000mAh+ | Safe, Durable, More affordable | Heavier, Shorter runtime |
LiFe | 6.6V | 2000mAh - 5000mAh+ | Long life cycles, Safer | Lower energy density, Heavier |
Upgrading the Transmission System to Support Electric Power
When converting a Nitro RC vehicle to electric power, one of the most critical aspects to address is the transmission system. Nitro-powered models rely on internal combustion engines that generate power through a mechanical setup, whereas electric vehicles use electric motors that require a different approach for efficient power transfer. This shift demands careful modifications to ensure the transmission system can handle the unique characteristics of electric power delivery.
Electric motors deliver torque instantly, which can lead to higher stresses on components like the gears and drive shafts. Upgrading the transmission system involves not only ensuring that the gears are compatible with the motor's power output but also that they can sustain the sustained torque without excessive wear. The following considerations are essential when upgrading the transmission system for electric power.
Key Considerations for Transmission Upgrade
- Gear Compatibility: Select gears that can handle higher torque and reduce the risk of stripping or failure.
- Reinforced Components: Opt for stronger materials in the transmission parts to handle the increased load and heat generated by the electric motor.
- Motor Mounting: Ensure the motor is securely mounted, allowing for proper alignment with the transmission system.
- High-Efficiency Bearings: Use bearings with low resistance to reduce power loss and heat buildup during operation.
Steps for Upgrading the Transmission
- Disassemble the Existing Transmission: Carefully remove the old transmission system, ensuring to inspect for any wear or damage that may affect performance.
- Install Electric Motor and Gearbox: Select a suitable electric motor and pair it with a compatible gearbox designed for the torque requirements.
- Reinforce the Drive System: Install stronger gears, shafts, and bearings to support the higher power output of the electric motor.
- Test and Adjust: After assembly, perform extensive testing to ensure the transmission functions smoothly and can handle the electric motor's performance under load.
Component Comparison Table
Component | Nitro (Stock) | Electric (Upgraded) |
---|---|---|
Transmission Type | Manual Gearbox | Automatic/Single-Speed |
Gear Material | Plastic/Metal | Metal Alloy |
Drive Shafts | Standard Steel | Reinforced Steel or Aluminum |
Bearings | Standard | High-Efficiency Bearings |
Important: Proper alignment and cooling of the transmission components are critical when adapting to electric power. Overheating can cause gear damage and premature wear of components.
Installing an Electronic Speed Controller (ESC) in Your Nitro RC
When converting a Nitro RC car to an electric setup, one of the essential components you'll need is an Electronic Speed Controller (ESC). This device is responsible for regulating the power flow from the battery to the motor, ensuring smooth acceleration and braking. Proper installation of the ESC is crucial to achieving optimal performance and protecting your components from damage.
Installing an ESC is straightforward but requires careful attention to wiring and compatibility with your new electric motor. Below is a step-by-step guide to help you with the process.
Step-by-Step Installation
- Prepare the ESC and Motor: Before starting, make sure that the ESC is compatible with your electric motor and battery. Double-check the motor specifications to ensure that the ESC's voltage and current ratings match the motor’s requirements.
- Mount the ESC: Position the ESC in a safe, secure spot within the car's chassis. Typically, this is near the motor mount or where the Nitro engine used to sit. Use double-sided tape or mounting brackets to secure it in place.
- Wiring the Motor and ESC: Connect the three motor wires to the corresponding terminals on the ESC. Ensure the connections are tight and insulated to prevent any short circuits.
- Connecting the Battery: Attach the power leads from the ESC to your battery's power connectors. Again, ensure secure and insulated connections. You may need a battery connector that matches your ESC’s input terminal.
- Calibration and Testing: Once everything is connected, calibrate the ESC with your transmitter and check for proper functionality. Test for smooth acceleration and deceleration.
Important Considerations
- ESC Compatibility: Make sure the ESC can handle the voltage and amperage your motor requires. Overloading the ESC can cause overheating and failure.
- Motor Type: The ESC needs to be compatible with the type of motor you're using, whether it's a brushed or brushless motor. Each type requires different handling from the ESC.
- Battery Voltage: Ensure your battery voltage is suitable for both the ESC and motor. Using a higher or lower voltage than recommended could damage your components.
Tip: When installing the ESC, always route wires away from hot components like the motor or exhaust area to avoid heat damage.
ESC Settings Table
Parameter | Recommended Setting | Explanation |
---|---|---|
Voltage Cutoff | 3.2V per cell | Protects the battery from deep discharge by cutting power at a safe voltage level. |
Motor Type | Brushless | Ensure that the ESC is configured for the type of motor you are using. |
Timing | 0 degrees | Adjust timing settings based on motor and ESC specifications to optimize performance. |
Wiring and Connecting Components for a Seamless Conversion
When converting a nitro RC car to electric, proper wiring and component integration are crucial to ensure efficient performance and longevity. Electric power systems require different wiring setups compared to their nitro counterparts, so understanding the components and their connections is key. Proper connections not only improve reliability but also maximize power delivery and minimize the risk of component failure.
This section will cover the essential steps in connecting the motor, battery, speed controller, and other electrical components to achieve a seamless conversion. Clear and organized wiring is critical for reducing interference, managing power flow, and ensuring safety during operation.
Key Steps for Proper Wiring
- Motor Connection: The electric motor should be connected to the ESC (Electronic Speed Controller) using the appropriate gauge wire. Ensure that the motor wires are securely soldered to the ESC terminals to prevent loose connections that could result in power loss or overheating.
- Battery Integration: Choose a battery with a suitable voltage and capacity for your motor and ESC. Connect the battery to the ESC using high-quality connectors, ensuring that polarity is correctly observed. Always check the voltage rating to match the specifications of the motor and ESC.
- ESC Setup: The ESC needs to be calibrated to recognize the motor's characteristics, including the number of cells in the battery pack. Most modern ESCs allow for automatic detection or manual setup via the ESC's programming card or software.
Wiring Diagram
Component | Connection Type | Notes |
---|---|---|
Electric Motor | ESC | Solder the motor wires to the ESC terminals. |
Battery | ESC | Use secure connectors, ensuring proper polarity. |
Receiver | ESC | Use a dedicated signal wire from the receiver to the ESC for throttle control. |
Tip: Double-check all connections before powering up the system to avoid shorts and electrical failures. A good practice is to use heat shrink tubing or electrical tape to insulate exposed wires and connectors.
Managing Wiring for Optimal Efficiency
- Wire Routing: Keep wires tidy and routed away from moving parts such as the wheels or suspension to prevent wear and tear.
- Wire Length: Avoid excess wire length, as it can cause resistance and interfere with clean power delivery.
- Connector Quality: Use high-quality connectors that offer secure connections to minimize the risk of power loss.
Adjusting the Gear Ratio for Electric Conversion
When converting a Nitro RC car to an electric setup, one of the key factors to optimize is the gear ratio. The gear ratio determines how efficiently the power from the motor is transmitted to the wheels, and getting it right can significantly improve the performance of your electric vehicle. Since electric motors behave differently than nitro engines, adjusting the gear ratio is essential for maximizing speed, acceleration, and overall efficiency.
The gear ratio influences both the top speed and acceleration of the car. A higher gear ratio results in faster top speeds, while a lower gear ratio improves acceleration but limits maximum speed. Finding the right balance between these two factors is crucial, depending on whether you prioritize acceleration or speed for your specific driving conditions.
Factors to Consider When Adjusting the Gear Ratio
- Motor Kv Rating: The Kv rating of the motor defines how many revolutions it makes per minute for every volt applied. A higher Kv motor will generally require a higher gear ratio for optimal performance, whereas a lower Kv motor may need a lower ratio to avoid overheating.
- Battery Voltage: The voltage of your battery also plays a role in the gear ratio. A higher voltage battery provides more power, allowing for a higher gear ratio without causing excessive strain on the motor.
- Traction and Terrain: The type of surface and traction you have will affect your gear choice. For rough terrain, a lower gear ratio might provide better control, while on smooth surfaces, a higher gear ratio might be more effective.
Steps to Find the Ideal Gear Ratio
- Assess Your Motor and Battery Setup: Start by considering the motor's specifications, such as its Kv rating and power output, alongside the voltage of the battery. These factors will guide your initial gear ratio choice.
- Experiment with Gear Combinations: Test different gear combinations to find the one that delivers the right balance between acceleration and top speed. Begin with the manufacturer's recommendations for similar setups.
- Monitor Temperature: After making adjustments, always monitor the motor and ESC temperatures. If either component gets too hot, it might indicate that the gear ratio is too aggressive, and you need to reduce it.
Quick Reference Table: Gear Ratios for Common Setups
Motor Kv Rating | Recommended Gear Ratio (Pinion to Spur) |
---|---|
3000 - 4000 Kv | 15T to 20T / 60T |
4000 - 5000 Kv | 18T to 22T / 58T |
5000+ Kv | 20T to 25T / 55T |
Important: Always ensure that your gear ratio is within the recommended range for your specific motor and battery combination. An improperly adjusted ratio can lead to motor failure or reduced performance.
Testing Your Converted Electric RC: Troubleshooting Common Issues
After converting your nitro RC to an electric model, it’s essential to test the vehicle thoroughly to ensure everything is functioning as expected. The transition from a fuel-powered engine to an electric system can introduce a variety of challenges that need to be addressed before you hit the track. In this section, we’ll explore some of the most common issues encountered during testing and offer practical troubleshooting advice.
When testing, always be prepared to check multiple systems in your RC, from the power electronics to the mechanical components. Identifying issues early can prevent long-term damage to your components. Below are some of the frequent problems and solutions that arise during the testing phase.
Common Issues and Solutions
- Motor Overheating: Overheating can occur if your motor is under heavy load for too long or if there is inadequate ventilation. Ensure the motor is not too small for your RC’s size and weight, and verify that your motor is mounted with enough airflow to prevent overheating.
- Battery Issues: If the battery doesn’t seem to hold a charge or drains quickly, check for poor connections or damaged wiring. Make sure the battery is suitable for your setup and that it is properly balanced.
- ESC Malfunctions: The electronic speed controller (ESC) may malfunction due to improper setup or faulty connections. Verify that the ESC is calibrated correctly and check all the wiring connections for integrity.
Diagnostic Checklist
- Check power connections: Ensure the battery, ESC, and motor are all connected correctly. Loose connections can cause inconsistent performance.
- Inspect the drivetrain: Look for any signs of friction or damage in the drivetrain. Ensure all gears and bearings are lubricated and functioning smoothly.
- Monitor motor performance: Pay attention to any unusual noises or excessive vibrations. These could indicate alignment issues or potential motor damage.
- Test ESC settings: Double-check that your ESC is properly configured for the motor you’re using. Many ESCs have multiple settings for different motor types.
Table of Common Issues
Issue | Possible Cause | Solution |
---|---|---|
Motor not spinning | Loose connections or faulty ESC | Inspect connections, recalibrate ESC |
Battery draining too fast | Overuse, damaged battery, or improper charger | Check battery condition, replace if necessary |
ESC overheating | Incorrect settings or poor ventilation | Ensure correct ESC configuration and airflow |
Note: Always perform a test run in a controlled environment to minimize damage to your components during troubleshooting. Be sure to have the right tools on hand to make adjustments quickly.