Nitrogen System for Transformers
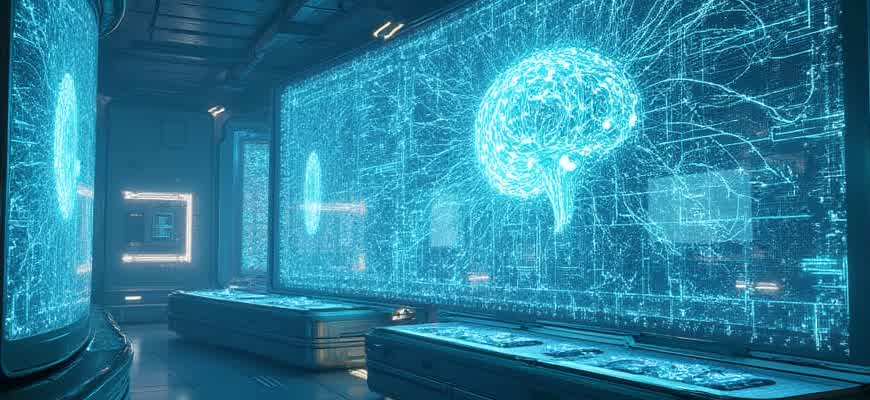
In modern transformer maintenance, the integration of a nitrogen-based protection system is becoming increasingly common. This method aims to prevent the risk of oxidation and degradation of the transformer oil, ensuring longevity and optimal performance. The nitrogen system is designed to create a controlled environment inside the transformer tank, minimizing the presence of oxygen and moisture, which can lead to the deterioration of insulation and other vital components.
The primary components of a nitrogen system include:
- Pressurized nitrogen cylinder
- Regulator for pressure control
- Distribution piping system
- Flow control valves
This system helps to significantly extend the life of transformer oil, reduce maintenance costs, and improve overall transformer efficiency.
Key Advantages of Nitrogen System Integration:
Advantage | Description |
---|---|
Prevention of Oxidation | Nitrogen eliminates the risk of oxidation in the transformer oil by displacing oxygen. |
Moisture Control | Reduced moisture content inside the transformer protects the insulation from premature aging. |
Improved Efficiency | Enhanced transformer efficiency due to the stable internal environment maintained by nitrogen. |
Comprehensive Guide to Nitrogen-Based Protection Systems for Transformers
In electrical power systems, transformers play a crucial role in the transmission and distribution of electricity. To ensure their reliable operation and prevent damage from internal faults or external conditions, advanced protection methods are implemented. One such method is the nitrogen-based protection system, which enhances the transformer's lifespan and operational efficiency.
Nitrogen systems are employed to safeguard transformers from moisture, oxygen, and other harmful elements that may cause oxidation or degradation of insulation materials. These systems use nitrogen gas to create an inert atmosphere inside the transformer, which reduces the risks of fire and failure, especially under harsh environmental conditions.
How Nitrogen Systems Work
The basic principle behind nitrogen-based systems is to inject nitrogen gas into the transformer’s tank, displacing the oxygen and moisture. This inert gas creates a protective shield that reduces the likelihood of corrosive reactions, thereby preserving the internal components of the transformer.
Key Benefits of Nitrogen Protection Systems
- Reduction in oxidation and corrosion of transformer components.
- Prevention of insulation degradation caused by moisture and air exposure.
- Minimized risk of fire or explosions by creating a non-reactive environment.
- Improved operational reliability and longevity of transformers.
Components of a Nitrogen Protection System
A typical nitrogen system consists of several key components to ensure consistent operation:
- Nitrogen Generator: Produces nitrogen gas by separating it from air using pressure swing adsorption (PSA) or membrane technology.
- Control Unit: Regulates the flow and pressure of nitrogen gas into the transformer tank.
- Safety Valve: Ensures that the gas pressure remains within the desired range.
- Monitoring Sensors: Track moisture levels, oxygen content, and temperature inside the transformer.
Maintenance Considerations
Proper maintenance is essential to ensure the nitrogen system continues to operate effectively. Regular checks on nitrogen purity, pressure levels, and sensor functionality are necessary to maintain optimal protection. It is also important to ensure that the generator is properly serviced to avoid any malfunctions.
Important: Regularly replacing filters and monitoring nitrogen purity levels helps prevent contamination that may compromise the transformer’s protection system.
Advantages and Limitations
Advantages | Limitations |
---|---|
Increases transformer lifespan by reducing internal degradation. | Initial setup and installation costs can be high. |
Improves safety by minimizing fire hazards and explosions. | Requires regular monitoring and maintenance for effective operation. |
Reduces maintenance costs related to corrosion and insulation failure. | System efficiency may decline if nitrogen purity is not maintained. |
How Nitrogen Systems Prevent Transformer Oil Contamination
Transformer oil plays a critical role in ensuring the proper functioning of electrical transformers by providing insulation and cooling. Over time, however, exposure to air, moisture, and other contaminants can degrade the quality of this oil, leading to reduced transformer efficiency and potential failure. To prevent such issues, nitrogen-based systems are widely utilized to protect transformer oil from contamination and deterioration.
A nitrogen system works by creating a controlled environment inside the transformer, which helps in minimizing the ingress of moisture, oxygen, and other harmful gases into the oil. By purging the transformer with nitrogen, the system maintains an inert atmosphere that significantly reduces the likelihood of oxidation and degradation of the oil, ensuring long-term reliability.
Key Benefits of Nitrogen Systems in Transformer Oil Protection
- Prevention of Oxidation: Nitrogen is an inert gas, which means it does not react with transformer oil, preventing the formation of acids and other harmful byproducts.
- Moisture Control: Nitrogen purges air, which often carries moisture, thus reducing the risk of water contamination that can cause insulation breakdowns.
- Prevention of Airborne Contaminants: The nitrogen atmosphere creates a barrier, limiting the entry of airborne particles and gases that can damage the oil’s properties.
How Nitrogen Systems Function in Protecting Transformer Oil
- Continuous Nitrogen Purging: Nitrogen is continuously supplied to the transformer, displacing the oxygen and moisture present in the oil tank.
- Pressure Maintenance: The system ensures that the internal pressure of the transformer is slightly higher than the external pressure, preventing the entry of external contaminants.
- Monitoring and Control: Sensors and automated systems monitor the nitrogen levels and pressure, adjusting the flow to ensure optimal protection.
"By introducing a steady flow of nitrogen into the transformer, the system ensures the oil remains free of contaminants and maintains its insulating properties for an extended period."
Effectiveness Comparison: Nitrogen vs. Traditional Methods
Method | Effectiveness in Preventing Contamination | Maintenance Requirements |
---|---|---|
Nitrogen System | High - Provides a consistent, inert environment | Low - Requires minimal maintenance once set up |
Traditional Sealing | Moderate - Relies on mechanical seals and air-tight enclosures | Moderate - Regular checks needed for seal integrity |
Optimizing Nitrogen Purity in Transformer Systems
In transformer applications, nitrogen gas is used to protect insulation materials from oxidation and moisture absorption, thus ensuring the longevity and reliability of electrical equipment. The purity level of nitrogen plays a critical role in maintaining the desired protective environment. High purity nitrogen helps to reduce the risk of contamination and enhances the performance of the transformer by preventing internal degradation over time.
The key to optimizing nitrogen purity levels is understanding the specific requirements of each transformer system, as different types of transformers and their applications may demand varying levels of gas purity. The goal is to achieve a balance between adequate nitrogen protection and operational efficiency while minimizing unnecessary energy consumption and equipment wear.
Key Factors in Nitrogen Purity Optimization
- Transformer Type: Different transformer configurations, such as oil-filled or gas-insulated, may require different nitrogen purity levels based on their design and operating conditions.
- Ambient Conditions: External environmental factors, like temperature and humidity, can influence the nitrogen gas requirement to maintain optimal protection.
- Operational Efficiency: It is essential to maintain a purity level that prevents excess nitrogen usage, as overuse can lead to increased operating costs and energy consumption.
Recommended Nitrogen Purity Levels
For effective protection, maintaining a nitrogen purity of 95% or higher is generally recommended. The following table outlines the common purity thresholds based on transformer applications:
Application | Recommended Nitrogen Purity |
---|---|
Oil-Filled Transformers | 95% to 98% |
Gas-Insulated Transformers | 98% and above |
HVDC Transformers | 99%+ |
Optimizing nitrogen purity ensures not only protection against corrosion but also enhances the operational efficiency and lifespan of transformers.
Choosing the Right Nitrogen Generation Method for Transformers
When selecting the most suitable nitrogen generation system for transformer protection, understanding the specific needs of the transformer and the available technologies is crucial. The primary objective is to provide a constant and reliable nitrogen supply to maintain the optimal conditions inside the transformer. Different nitrogen generation methods offer varying levels of efficiency, cost-effectiveness, and reliability. Factors such as installation environment, transformer size, and operational requirements should all be considered when making a decision.
The two most common methods for generating nitrogen are Pressure Swing Adsorption (PSA) and Membrane Nitrogen Generation. Each system has its strengths and limitations, which need to be evaluated in terms of long-term performance, ease of maintenance, and the required purity of nitrogen. Below is a comparison of the two methods to help with the selection process.
Comparison of Nitrogen Generation Methods
Method | Advantages | Disadvantages |
---|---|---|
Pressure Swing Adsorption (PSA) |
|
|
Membrane Nitrogen Generation |
|
|
Important Consideration: The choice between PSA and Membrane Nitrogen Generation depends largely on the transformer’s size and the level of purity required. PSA is better suited for large transformers requiring high-purity nitrogen, while Membrane systems are cost-effective for smaller applications.
Installation Guidelines for Nitrogen Systems in Power Transformers
When implementing a nitrogen system for a power transformer, proper installation is critical to ensure its effectiveness in enhancing transformer performance and longevity. These systems help to maintain a controlled atmosphere, reducing the risk of oxidation and preserving the integrity of insulating oil. Adhering to a precise installation procedure guarantees that the nitrogen system will function optimally and provide long-term benefits to the transformer.
The installation process involves several key steps, from selecting appropriate equipment to ensuring proper integration with the transformer. Detailed planning and execution are necessary to avoid common issues such as leaks or improper pressure regulation. Below are the recommended guidelines to follow during the installation of nitrogen systems.
Key Steps for Installing Nitrogen Systems
- System Design and Layout: Ensure the nitrogen generator, storage, and distribution components are placed according to the manufacturer's guidelines. The nitrogen delivery system should be designed to prevent contamination and maintain a stable pressure within the transformer.
- Integration with Transformer: Properly connect the nitrogen supply line to the transformer's breather or inert gas valve. Ensure that all fittings are secure and leak-proof.
- Pressure and Flow Control: Install pressure regulators and flow meters to control the nitrogen flow and pressure. These components help maintain the required atmospheric conditions inside the transformer.
- System Calibration: After installation, calibrate the system to monitor and adjust the nitrogen levels automatically. Ensure that the system is responsive to changes in transformer conditions.
Installation Checklist
- Verify transformer specifications and nitrogen system compatibility.
- Check all components for quality and integrity before installation.
- Ensure proper grounding of nitrogen equipment.
- Test pressure regulation system to ensure correct nitrogen flow.
- Confirm all connections are leak-proof and sealed.
Important Considerations
The nitrogen system should be designed with redundancy in mind to prevent failures due to equipment malfunction. Backup nitrogen sources or storage systems may be required to ensure continuous operation under all conditions.
System Maintenance and Monitoring
Regular monitoring and maintenance of the nitrogen system are essential to ensure its continued efficiency. Scheduled inspections and adjustments to pressure and flow rates will help prevent system degradation and protect the transformer from operational failures.
Maintenance Task | Frequency |
---|---|
Check nitrogen pressure | Monthly |
Inspect filtration system | Quarterly |
Test system for leaks | Annually |
Monitoring and Maintaining Nitrogen Pressure in Transformer Systems
Maintaining optimal nitrogen pressure within transformer systems is critical for their safe and efficient operation. Nitrogen is often used to create a protective atmosphere that prevents oxidation, moisture accumulation, and internal arcing. Accurate monitoring and consistent pressure regulation ensure that transformers operate within the required parameters, reducing the risk of damage and enhancing their lifespan.
Monitoring nitrogen pressure involves the use of specialized sensors and gauges that track pressure levels in real time. These devices are integrated into the transformer's nitrogen system and are designed to trigger alarms if pressure falls outside predefined thresholds. Regular checks and adjustments are necessary to compensate for pressure fluctuations due to environmental changes or system leaks.
Key Considerations for Effective Nitrogen Pressure Management
- Pressure Sensors: Regular calibration of sensors ensures accurate readings and prevents false alarms.
- Leak Detection: Routine inspections for potential leaks help identify issues early and prevent pressure loss.
- System Integrity: Maintenance of valves, pipes, and seals is necessary to avoid pressure fluctuations caused by mechanical failure.
- Environmental Factors: Seasonal temperature variations can affect nitrogen pressure, requiring adjustments to maintain consistent levels.
Steps for Maintaining Nitrogen Pressure
- Check nitrogen pressure levels daily using integrated sensors or manual gauges.
- Perform routine leak checks to identify any loss of nitrogen, ensuring the system remains pressurized.
- Adjust nitrogen pressure based on environmental conditions and transformer load.
- Verify proper function of pressure relief valves to prevent over-pressurization.
Important: Low nitrogen pressure can lead to moisture ingress, which compromises the insulating properties of the transformer oil, potentially causing electrical faults. Conversely, high pressure can damage seals and increase wear on system components.
Recommended Pressure Ranges
Transformer Type | Recommended Pressure Range |
---|---|
Oil-immersed Transformers | 0.2 to 0.4 MPa |
Gas-insulated Transformers | 0.3 to 0.6 MPa |
Addressing Common Issues with Nitrogen Systems in Transformers
The implementation of nitrogen systems in transformers plays a crucial role in preventing oxidation and ensuring the longevity of transformer components. However, despite their benefits, these systems can face several operational challenges that require careful attention. These issues can affect the overall efficiency of the nitrogen system, and addressing them is vital to maintaining optimal transformer performance.
One of the primary concerns with nitrogen systems is the maintenance of consistent nitrogen pressure and purity. Fluctuations in either parameter can compromise the system's ability to effectively displace moisture and oxygen, leading to potential damage to transformer parts. Proper monitoring and adjustments are necessary to prevent such issues and enhance the reliability of the system.
Common Issues and Solutions
- Pressure Fluctuations: Variations in nitrogen pressure can disrupt the protective atmosphere, leading to the possibility of air entering the transformer. This can be caused by faulty pressure regulators or leaks in the system.
- Low Nitrogen Purity: If the purity of nitrogen drops below the required threshold, the protective environment becomes ineffective, and moisture or oxygen can cause deterioration of the transformer components.
- System Contamination: Contaminants in the nitrogen, such as moisture or hydrocarbons, can harm the transformer’s insulation materials, causing premature failure.
Key Maintenance Actions
- Regular Inspection: Ensure that all seals, valves, and regulators are intact and functioning correctly to prevent nitrogen leakage.
- Periodic Nitrogen Purity Checks: Regular testing of nitrogen purity is essential to ensure that it meets the required standards for transformer protection.
- Contamination Prevention: Install filters and moisture separators to remove impurities from the nitrogen supply.
Important: Timely detection and resolution of these issues can significantly extend the operational life of a transformer and reduce the need for costly repairs or replacements.
Table of Common Issues
Issue | Possible Cause | Solution |
---|---|---|
Pressure fluctuations | Faulty regulators, leaks | Inspect and repair the system’s pressure regulators |
Low nitrogen purity | Contaminated nitrogen source | Regularly check nitrogen purity and replace filters as needed |
Contamination in nitrogen | Improper filtration, faulty moisture separators | Install or replace filters and moisture separators to ensure clean nitrogen |
Cost-Effectiveness of Nitrogen Systems for Long-Term Transformer Protection
Transformers are essential components in the electrical grid, and their reliability is critical for uninterrupted power supply. Traditional methods for transformer protection have been widely used, but recent advancements suggest that integrating nitrogen-based systems can provide more cost-efficient and long-lasting solutions. By utilizing nitrogen to maintain an inert environment within transformers, these systems minimize the risk of oxidative damage, reducing the frequency of maintenance and extending the lifespan of equipment.
The implementation of nitrogen systems reduces the need for costly repairs or replacements caused by environmental factors such as moisture and oxygen, which are major contributors to transformer degradation. The long-term cost savings come from lower operational disruptions, fewer maintenance cycles, and increased reliability. This makes nitrogen systems a highly cost-effective alternative to conventional protection methods.
Key Benefits of Nitrogen Systems
- Extended Transformer Lifespan: Reduced exposure to oxygen and moisture decreases internal wear and tear, leading to a longer operational life.
- Reduction in Maintenance Costs: Fewer breakdowns and less frequent need for maintenance or oil replacement can drastically reduce operational costs.
- Improved Safety: Nitrogen systems mitigate the risk of fire and explosion by preventing the combustion of flammable gases inside the transformer.
Comparison with Conventional Methods
Feature | Nitrogen System | Traditional Methods |
---|---|---|
Maintenance Frequency | Lower | Higher |
Cost Over Time | Lower | Higher |
Impact on Transformer Longevity | Higher | Lower |
Key takeaway: Nitrogen-based protection systems offer significant long-term savings due to their ability to extend transformer life, reduce maintenance needs, and improve overall operational safety.
Comparing Nitrogen Systems with Traditional Transformer Oil Preservation Methods
In the field of transformer maintenance, the preservation of insulating oil plays a crucial role in ensuring reliable operation and long service life. Traditionally, transformer oil has been preserved using various methods, primarily through the use of oil filtration and breathing systems. These methods are designed to protect the oil from contamination by moisture and air, which can lead to deterioration. However, nitrogen-based preservation systems have recently emerged as an alternative, offering distinct advantages in oil protection and transformer reliability.
While traditional oil preservation techniques have served their purpose, they come with certain limitations, such as the risk of air and moisture ingress during operation. Nitrogen systems, on the other hand, offer a more controlled and effective solution to this problem by creating a sealed, inert atmosphere inside the transformer. This approach minimizes oxidation and moisture absorption, thus prolonging the life of the insulating oil and improving overall transformer performance.
Comparison of Key Aspects
Aspect | Traditional Methods | Nitrogen Systems |
---|---|---|
Protection Mechanism | Oil filtration and air/breathing systems | Inert nitrogen atmosphere |
Moisture Control | Limited; prone to moisture absorption | Prevents moisture ingress effectively |
Oxidation Prevention | Air exposure leads to oxidation | Completely eliminates oxidation risks |
Maintenance Requirements | Frequent maintenance of filters and seals | Lower maintenance, minimal intervention |
Transformer Longevity | Subject to wear and oil degradation | Extended service life due to reduced contamination |
Advantages of Nitrogen Systems
- Moisture control: Nitrogen systems effectively prevent moisture from entering the transformer, ensuring the insulating oil remains dry and stable.
- Oxidation reduction: By replacing oxygen with nitrogen, these systems eliminate the risk of oil oxidation, thus preserving the oil's insulating properties.
- Lower maintenance: Nitrogen systems require less frequent maintenance compared to traditional methods, reducing downtime and operational costs.
- Improved transformer reliability: The reduction of moisture and oxidation helps maintain optimal performance, leading to fewer failures and extended service life.
"The adoption of nitrogen-based preservation systems represents a significant improvement in the way we protect transformers, offering long-term benefits in both performance and cost efficiency."