Convert Nitro to Electric
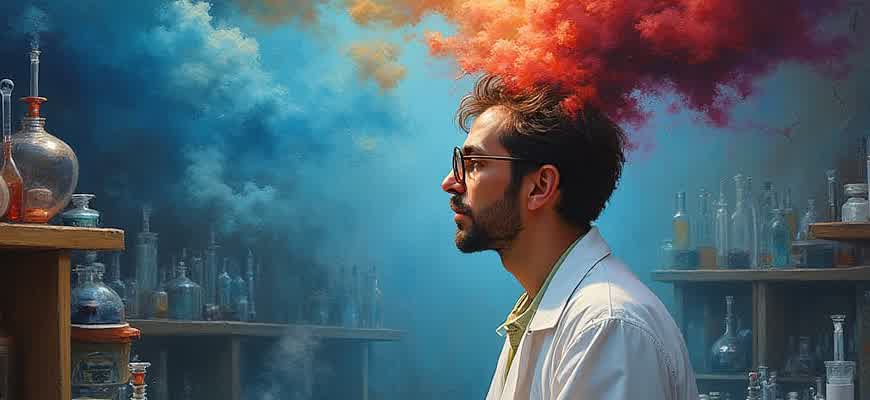
Transforming traditional nitro-powered vehicles to electric engines has become a popular modification for hobbyists and engineers alike. This shift not only provides environmental benefits but also enhances performance and reduces long-term maintenance costs. The process of converting a nitro vehicle to electric involves replacing the internal combustion engine with an electric motor and installing a suitable power system.
Key Benefits of Conversion:
- Reduction in fuel costs and emissions.
- Lower maintenance due to fewer moving parts.
- Improved torque and smoother acceleration.
Steps for Conversion:
- Remove the nitro engine, fuel tank, and associated components.
- Install the electric motor and transmission system.
- Fit a battery pack compatible with the motor's power needs.
- Update the electronic speed controller (ESC) to manage the motor's speed.
"Switching from nitro to electric offers a cleaner and quieter alternative, giving hobbyists more time on the track without the hassle of constant refueling and maintenance."
Conversion Cost Breakdown:
Component | Estimated Cost |
---|---|
Electric Motor | $150 - $300 |
Battery Pack | $100 - $200 |
Electronic Speed Controller (ESC) | $50 - $150 |
Understanding the Basics of Nitro-to-Electric Conversion
Converting a nitro-powered vehicle to electric propulsion is a popular project among RC enthusiasts. This process involves replacing the internal combustion engine with an electric motor, offering cleaner, quieter, and more efficient performance. The conversion provides several advantages, including reduced maintenance and improved control, but it also requires careful planning and understanding of the components involved.
To successfully complete a nitro-to-electric conversion, it’s essential to grasp the basic principles and components that play a role in the process. The transition involves changes to the powertrain, electronics, and fuel systems. Let’s break down the key aspects of such a conversion.
Key Components of Conversion
- Electric Motor – The heart of the electric power system. It provides the necessary torque and speed to the vehicle.
- Battery Pack – A reliable power source, typically lithium polymer (LiPo) or nickel-metal hydride (NiMH), which stores energy for the motor.
- Electronic Speed Controller (ESC) – Controls the speed and power distribution from the battery to the motor.
- Chassis Modifications – The physical frame of the vehicle may need adjustment to accommodate the motor and battery.
- Power Wiring – Properly sized cables and connectors ensure safe and efficient energy transfer.
Steps to Complete the Conversion
- Remove Nitro Engine: Disconnect and remove the nitro engine, fuel tank, and exhaust system.
- Install Electric Motor: Choose an appropriate motor size and mount it securely to the chassis.
- Battery and ESC Placement: Position the battery and ESC in locations that balance the vehicle's weight and ensure proper airflow.
- Wiring: Connect the motor to the ESC and the ESC to the battery, ensuring all connections are insulated and secure.
- Test and Tune: After assembly, test the vehicle under various conditions to ensure everything operates as expected.
Note: During the conversion, it's important to ensure that the ESC and battery are compatible with each other, as mismatched components can lead to overheating or underperformance.
Comparison of Nitro and Electric Powertrains
Feature | Nitro Powertrain | Electric Powertrain |
---|---|---|
Fuel Source | Nitro fuel | Electricity (Battery) |
Maintenance | High (engine maintenance, fuel system) | Low (minimal wear on motor and ESC) |
Noise | High (loud engine noise) | Low (silent operation) |
Performance | Variable (depends on fuel and engine tuning) | Consistent (smooth and predictable) |
Key Components Required for Conversion
Converting a nitro-powered vehicle to an electric one involves integrating a set of critical components that work together to replace the internal combustion engine and related systems. The main focus is on achieving high efficiency, performance, and reliability through the use of advanced electric technologies.
The conversion process requires careful selection of parts that are compatible with each other and suited for the specific type of vehicle. Below is a list of the essential components needed for this transformation.
Essential Components for Electric Conversion
- Electric Motor: The core component that replaces the engine, providing the vehicle with propulsion. These motors vary in size and power depending on the desired performance.
- Battery Pack: Supplies power to the electric motor. The capacity and voltage of the battery depend on the desired range and speed.
- Controller: Regulates the power flow between the motor and the battery, ensuring smooth acceleration and deceleration.
- Charging System: Allows the battery to be recharged, often through an external connection to an electric power source.
- Battery Management System (BMS): Monitors the health of the battery pack, ensuring safe charging and discharging cycles to maximize battery life.
Steps to Follow in the Conversion Process
- Remove the internal combustion engine and associated components.
- Install the electric motor and mount it securely within the vehicle frame.
- Place the battery pack in a safe, accessible location, ensuring proper weight distribution.
- Connect the motor to the controller and the controller to the battery pack.
- Install a charging system and integrate the BMS to manage the battery's operation.
- Test the system for proper functionality and make adjustments as necessary.
Important Considerations
Ensure that the electric motor’s power rating matches the vehicle's weight and desired performance specifications. The battery pack should also be chosen carefully to balance between range, size, and weight.
Component Comparison Table
Component | Purpose | Key Considerations |
---|---|---|
Electric Motor | Replaces the combustion engine for propulsion | Power output, efficiency, size |
Battery Pack | Stores electrical energy for the motor | Capacity, voltage, weight |
Controller | Manages power flow from the battery to the motor | Compatibility, power management |
Charging System | Recharges the battery pack | Charging speed, connectivity |
Battery Management System (BMS) | Monitors battery health and safety | Monitoring accuracy, safety protocols |
Choosing the Right Electric Motor for Your Nitro Model
When converting a nitro model to electric power, selecting the correct motor is one of the most crucial steps in ensuring a smooth transition. The choice of motor impacts the performance, handling, and overall experience of the model. Whether you're aiming for speed, endurance, or balance, understanding the different motor types and their specifications will guide you toward the best option for your needs.
Electric motors for model cars typically come in two main types: brushed and brushless. Each type has its own advantages and is suited for different applications. Before making your decision, consider factors like the size and weight of your model, your performance goals, and your budget.
Factors to Consider When Choosing an Electric Motor
- Motor Type: Brushless motors are more efficient, offer higher torque, and are more durable compared to brushed motors, making them ideal for high-performance setups.
- Motor Size: Ensure the motor fits within the space constraints of your model. The size should match the intended design, especially in terms of power-to-weight ratio.
- KV Rating: The KV (RPM per volt) rating indicates the motor's speed capabilities. Higher KV ratings are better for speed, while lower KV motors offer more torque and are better suited for climbing or heavy-duty use.
- Power Output: Choose a motor with sufficient power to match the weight and desired performance. Overpowered motors can lead to handling issues and excessive heat, while underpowered ones may fail to deliver the desired speed or torque.
Comparison Table of Brushed vs. Brushless Motors
Feature | Brushed Motor | Brushless Motor |
---|---|---|
Efficiency | Lower | Higher |
Maintenance | Requires regular maintenance | Minimal maintenance |
Torque | Lower | Higher |
Price | Cheaper | More expensive |
When transitioning from nitro to electric, consider the power-to-weight ratio, as this will significantly affect both speed and handling. Brushless motors are often the preferred choice for high-performance electric model cars.
Step-by-Step Process of Replacing the Nitro Engine
Switching from a nitro engine to an electric motor involves several crucial steps to ensure that the vehicle operates efficiently and safely. This transformation requires not only replacing the engine but also making adjustments to the vehicle's electrical system, battery setup, and other key components. Following the right steps can help ensure that the conversion is done smoothly, offering better performance, reduced maintenance, and cleaner operation.
The process begins with removing the existing nitro engine and preparing the chassis for the new electric components. This involves careful planning, as different vehicles may require specific modifications. Once the vehicle is prepped, you will need to install the motor, power system, and other related parts, which require both mechanical and electrical work. The following steps outline this conversion in detail.
Step-by-Step Guide
- Remove the Nitro Engine
- Disconnect the fuel lines, exhaust, and engine mounting screws.
- Carefully detach the nitro engine from the chassis.
- Clean the area where the engine was mounted, removing any residue or fuel-related components.
- Prepare for the Electric Motor Installation
- Check the chassis for space compatibility with the electric motor.
- Install motor mounts if necessary, ensuring they are securely fastened.
- Install the Electric Motor
- Mount the motor on the chassis, ensuring proper alignment with the drivetrain.
- Secure the motor with appropriate screws and verify tightness.
- Wiring and Power System Setup
- Connect the electric motor to the speed controller.
- Install a suitable battery pack and make sure the wiring is well insulated and secure.
- Test and Fine-Tune
- Test the motor’s response to throttle input and adjust settings if necessary.
- Monitor the temperature and power distribution to ensure everything is functioning properly.
Tip: Always use high-quality connectors and wires to avoid potential overheating or power loss issues in the system.
Component Compatibility Table
Component | Nitro Engine | Electric Conversion |
---|---|---|
Engine | Combustion engine with fuel tank | Brushless DC motor |
Fuel System | Fuel lines, exhaust | Battery pack, ESC (Electronic Speed Controller) |
Mounting | Engine mounts and screws | Motor mounts and brackets |
Integrating Electric Power System into a Nitro-Powered Chassis
Converting a nitro-powered vehicle to electric requires a careful approach to integrate the electric components into an existing chassis. The chassis, originally designed to house internal combustion engines, must be modified to accommodate an electric powertrain while ensuring optimal performance and safety. Proper planning and execution are essential to achieve a balanced and functional system that does not compromise the vehicle's structural integrity.
The integration process starts with selecting the appropriate electric motor, battery, and power electronics that match the vehicle's intended performance. Afterward, it is necessary to plan the placement and secure the components to the chassis. This involves adapting the suspension, drivetrain, and other structural elements to ensure they support the added weight and power output of the electric system.
Steps for Integration
- Remove Existing Nitro Components: Start by stripping down the vehicle, removing the nitro engine, fuel tank, exhaust system, and any associated parts. This creates space for the electric motor and battery system.
- Design Custom Mounting Points: The electric motor and battery require custom mounting points. Depending on the chassis, brackets and reinforcements may be needed to secure the components in place.
- Install Electric Powertrain: Install the motor in place of the old engine, ensuring proper alignment with the drivetrain. The battery should be placed in a secure location, such as under the chassis or within the frame, ensuring weight distribution is balanced.
- Integrate Power Electronics: Place the power electronics (e.g., ESC, wiring, and connectors) in a protected area, such as near the motor or within the chassis. Proper insulation and waterproofing may be necessary to ensure longevity and reliability.
Important: Proper integration of cooling systems is crucial for preventing overheating, especially for the motor and battery. Ensure that airflow is adequate and consider adding additional cooling systems if necessary.
Key Considerations
Consideration | Action |
---|---|
Weight Distribution | Ensure that the motor and battery are placed in a way that maintains or improves the vehicle's handling and performance. |
Power Requirements | Select motor and battery combinations that meet the desired performance goals without exceeding the vehicle's capacity. |
Structural Integrity | Reinforce areas where new components are mounted to avoid compromising the chassis' strength and safety. |
Calculating Battery Requirements for Optimal Performance
When converting a Nitro-powered vehicle to electric, the battery choice plays a crucial role in determining overall performance. Properly selecting the right battery capacity ensures the vehicle delivers sufficient power while maintaining efficiency. Factors such as vehicle weight, motor specifications, and expected driving conditions must be carefully considered when calculating the ideal battery size.
To achieve the best balance between performance and endurance, it is essential to calculate the required energy storage based on the energy demands of the electric motor and driving requirements. This calculation helps in selecting the right battery type, capacity, and voltage for optimal results.
Key Factors in Battery Sizing
- Motor Power Rating: The power output of the electric motor directly influences battery capacity requirements. Higher-powered motors will demand larger battery capacities to maintain performance over extended periods.
- Vehicle Weight: A heavier vehicle requires more energy to move, which means a larger battery pack is necessary to ensure adequate range and performance.
- Driving Style: Frequent acceleration and high speeds will require a higher energy demand, impacting the battery size required for optimal power delivery.
Calculation Steps
- Determine Energy Consumption: Estimate the average energy consumption (in Wh/mile) based on the motor's power output and vehicle characteristics.
- Define Desired Range: Determine the desired range (in miles) you want the vehicle to travel on a single charge.
- Calculate Battery Capacity: Multiply the energy consumption (Wh/mile) by the desired range (miles) to determine the required battery capacity in watt-hours (Wh).
Example: If the motor consumes 150 Wh/mile and you want a range of 50 miles, the required battery capacity would be:150 Wh/mile * 50 miles = 7500 Wh (or 7.5 kWh).
Battery Specifications Table
Motor Power (kW) | Energy Consumption (Wh/mile) | Desired Range (miles) | Required Battery Capacity (Wh) |
---|---|---|---|
5 | 150 | 50 | 7500 |
10 | 250 | 60 | 15000 |
15 | 300 | 70 | 21000 |
Common Challenges and Troubleshooting Tips During Conversion
Converting a nitro vehicle to electric involves overcoming several technical hurdles. From battery placement to electrical connections, there are various factors to consider to ensure the conversion is successful. Many of these challenges stem from differences in power delivery and the need to adapt components to fit within the constraints of the original vehicle design.
While the benefits of electric vehicles are clear, the conversion process can be tricky. Below are some common issues and troubleshooting tips to help you navigate the challenges associated with transforming your nitro-powered vehicle into an electric one.
Power and Electrical System Compatibility
One of the primary difficulties lies in the integration of the electric motor with the existing mechanical components. The power demands of the electric system must be carefully balanced with the vehicle’s original frame and drivetrain.
- Issue 1: Motor and ESC Compatibility – It is essential to choose a motor that matches the vehicle's size and weight. Mismatched motor power can lead to overheating or underperformance.
- Issue 2: Battery Sizing – The battery pack must provide sufficient voltage and capacity without adding unnecessary weight. Too large a battery could affect the vehicle’s handling.
- Issue 3: Wiring and Connections – Improperly installed wiring can cause electrical shorts or instability in power delivery, leading to unreliable performance.
Mechanical Adaptation and Space Constraints
Adapting the mechanical structure to accommodate the electric components is another significant challenge. Many nitro-powered vehicles have limited space for battery and motor installation, requiring modifications.
- Challenge 1: Space Management – You may need to make adjustments to the frame or chassis to fit larger batteries or motors. This may involve removing non-essential parts or repositioning components.
- Challenge 2: Weight Distribution – Battery placement can significantly affect the balance of the vehicle. Incorrect placement can make the vehicle harder to control and impact handling.
Important Tip: Always check the alignment and balance after installation. A poorly balanced vehicle can result in poor handling and faster wear on the tires.
Troubleshooting Table
Problem | Possible Cause | Solution |
---|---|---|
Battery not holding charge | Battery capacity mismatch | Upgrade to a battery with higher capacity or ensure proper charging cycle. |
Motor overheating | Excessive load or inadequate cooling | Install a cooling fan or reduce motor load by adjusting gear ratios. |
Vehicle not moving | Wiring or ESC malfunction | Check all wiring connections for loose or damaged wires and test the ESC for faults. |
Testing and Tuning Your Converted Electric Vehicle
Once you’ve completed the conversion of your vehicle to electric power, it’s time to ensure everything works as intended. This phase involves rigorous testing and fine-tuning to optimize the performance and safety of your newly converted electric vehicle. Carefully assessing the various components and systems is crucial for a successful conversion, ensuring it drives smoothly and reliably. Without thorough testing, there could be performance or safety issues that may not be immediately apparent.
In this stage, you will perform tests on the battery pack, electric motor, and control systems, followed by tuning to enhance the efficiency and driving experience. Proper calibration of parameters such as voltage, current, and regenerative braking will be necessary to ensure that your vehicle functions as efficiently as possible. Attention to detail in this phase can also lead to increased range and better handling on the road.
Essential Testing Procedures
- Battery System Check: Ensure that the battery pack is properly installed and securely mounted. Verify that all wiring and connectors are intact and free of faults.
- Motor Performance: Test the electric motor under various load conditions to check for smooth operation and sufficient power output.
- Thermal Management: Monitor the temperature of the motor and battery during operation to prevent overheating and ensure efficient cooling systems are functioning.
- Regenerative Braking: Test the regenerative braking system to make sure it engages correctly and helps slow the vehicle efficiently.
Important Tuning Considerations
- Battery Voltage Adjustment: Fine-tune the battery voltage settings to match the motor’s requirements and optimize power delivery.
- Throttle Response: Adjust the throttle mapping for smooth acceleration and deceleration, ensuring the vehicle is responsive but not jerky.
- Energy Management: Configure the energy management system to balance battery usage and power regeneration for maximum range and efficiency.
Always consult your vehicle’s user manual and the manufacturer’s guidelines for specific testing procedures to avoid damage or voiding warranties.
Key Performance Metrics
Metric | Recommended Value |
---|---|
Motor Temperature | Under 85°C (185°F) |
Battery Voltage | Nominally between 3.7V and 4.2V per cell |
Range per Charge | Depending on the vehicle size, at least 100 miles |
Regenerative Braking Efficiency | Effective energy recovery during braking |