Liquid Nitrogen Generation System
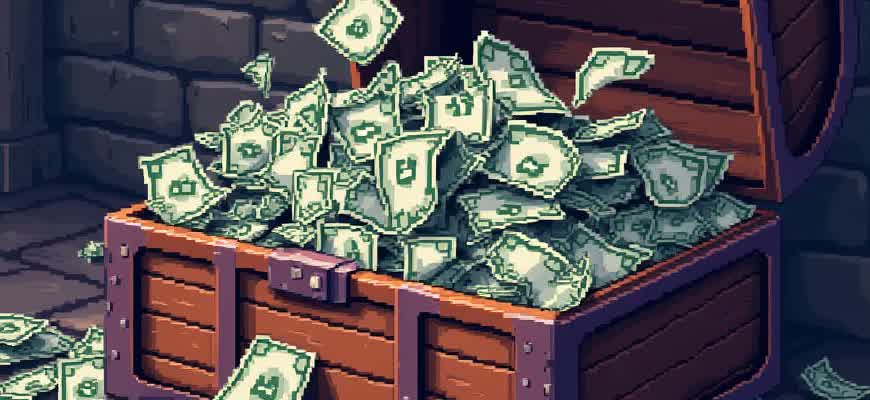
A liquid nitrogen generation system is designed to efficiently produce nitrogen in its liquid state for various industrial applications. These systems typically operate based on the principle of air separation, which involves separating nitrogen from other components in the atmosphere through cooling and compression techniques. The end result is nitrogen at extremely low temperatures, suitable for use in medical, laboratory, and industrial environments.
The core process involves several stages:
- Compression: Air is compressed to a high pressure for cooling.
- Cooling: The compressed air is cooled to low temperatures to condense gases.
- Separation: Nitrogen is isolated from oxygen and other gases through fractional distillation or membrane technology.
- Storage: The purified liquid nitrogen is stored in insulated tanks for future use.
Key Components:
Component | Description |
---|---|
Compressor | Compresses ambient air for cooling and separation. |
Heat Exchanger | Cool the compressed air to below freezing temperatures. |
Distillation Column | Separates nitrogen from other gases in the air. |
"Liquid nitrogen systems are integral in industries requiring precision cooling, including cryogenics, food processing, and medical applications." - Industry Expert
Key Components and Technologies Behind Liquid Nitrogen Production
The production of liquid nitrogen (LN2) relies on several complex systems and components that work together to separate nitrogen from the air and cool it to its liquefaction point. The most common method for producing liquid nitrogen is through air separation, utilizing cryogenic technologies. Below are the key components involved in this process:
These technologies are designed to separate nitrogen from other components of the air, such as oxygen and argon, while maintaining a high level of efficiency. By using the principle of gas liquefaction, liquid nitrogen can be produced with a high purity, making it essential for various industrial applications like cryogenics, food processing, and medical use.
Key Components
- Air Compressor: Increases air pressure to facilitate subsequent cooling and separation.
- Pre-cooling System: Lowers the temperature of the air before it enters the main separation unit.
- Distillation Column: Separates oxygen, nitrogen, and other gases based on their boiling points.
- Expansion Valve: Reduces the pressure of the nitrogen gas, leading to a temperature drop and liquefaction.
- Heat Exchanger: Transfers heat between gases in the system to improve energy efficiency.
Technologies Involved
- Pressure Swing Adsorption (PSA): A process used for nitrogen purification, which separates nitrogen from other gases based on adsorption characteristics.
- Liquefaction Process: A cryogenic process where nitrogen gas is cooled and compressed to reach its liquid form.
- Continuous Cryogenic Distillation: A highly efficient method for continuously separating air components at low temperatures.
"The efficiency of the air separation unit is highly dependent on the integration of these components and technologies, each playing a crucial role in achieving optimal nitrogen purity and production rates."
System Design and Efficiency
Component | Function |
---|---|
Compressor | Increases air pressure for cooling and separation. |
Pre-cooler | Reduces air temperature before entering the distillation unit. |
Distillation Column | Separates air components based on their boiling points. |
Heat Exchanger | Transfers heat to improve energy efficiency. |
Installation Process: Step-by-Step Guide for Setting Up a Nitrogen Generator
Setting up a nitrogen generator requires precise planning and accurate execution to ensure efficient operation and safety. The installation process involves several critical steps, from initial preparation to final testing. Proper installation helps to maximize the system's performance, prevent potential issues, and optimize nitrogen production. Below is a detailed step-by-step guide for setting up a nitrogen generator system.
Before beginning the installation process, ensure that all necessary equipment and tools are available. A typical nitrogen generator setup requires compressors, filtration units, pressure regulators, and nitrogen separation modules. Additionally, always verify that the installation area meets safety regulations and offers adequate ventilation for the equipment.
Step-by-Step Installation
- Preparation and Site Assessment
- Choose an installation location with sufficient space for the generator and auxiliary components.
- Ensure the area is well-ventilated to avoid buildup of nitrogen gas.
- Verify that all electrical connections, water sources, and air supplies are accessible.
- Assembly of Components
- Position the compressor and filtration units according to the system layout.
- Connect the nitrogen generation modules and ensure they are securely mounted.
- Install pressure regulators and control valves for proper gas flow management.
- Electrical and Piping Connections
- Connect the electrical supply to the nitrogen generator, ensuring that the power rating matches the system requirements.
- Install and secure the gas piping, ensuring there are no leaks in the system.
- Testing and Calibration
- Conduct initial power-on tests and check for system leaks.
- Calibrate the generator to ensure the proper nitrogen purity and flow rates.
- Run a full system test to verify functionality under operational conditions.
It is crucial to perform a final inspection and safety check before the generator becomes operational. This ensures that all connections are secure and the system meets regulatory standards.
Important Considerations
Factor | Recommendation |
---|---|
Electrical Requirements | Ensure the system is connected to a dedicated power source with the correct voltage and current. |
Pressure Settings | Adjust pressure regulators to ensure nitrogen production remains within the specified parameters for efficiency. |
Safety Precautions | Use appropriate protective gear and follow safety protocols to prevent accidents during installation. |
Energy Consumption and Cost Factors in Operating a Nitrogen Generation System
The energy demand and cost structure associated with running a nitrogen production system can be complex, as it depends on several variables such as the method of generation, system efficiency, and operational scale. The most common methods for nitrogen generation are pressure swing adsorption (PSA) and cryogenic distillation. Each method comes with its own energy consumption profile, which directly impacts operating expenses.
Factors influencing energy use include the purity level of nitrogen required, the flow rate, and system maintenance. Systems requiring higher purity levels typically consume more energy to achieve the necessary separation of gases. Moreover, fluctuating electricity prices and equipment depreciation also contribute significantly to the overall operating cost.
Key Energy Consumption Factors
- Method of Nitrogen Generation: PSA systems are generally more energy-efficient for smaller scale operations, while cryogenic systems are better suited for large-scale production but consume more power.
- Purity Level: Higher nitrogen purity demands greater energy consumption due to additional filtration and separation processes.
- Flow Rate: Larger flow rates require more significant compression and cooling, leading to higher energy needs.
- System Efficiency: Well-maintained systems with optimized components will use less energy over time.
Cost Breakdown
- Initial Setup Costs: This includes the purchase of equipment, installation, and any necessary infrastructure changes.
- Operational Costs: Primarily driven by energy consumption, but also by maintenance, labor, and other consumables such as adsorbent materials for PSA systems.
- Electricity Costs: These are usually the largest recurring cost, especially if the system operates 24/7.
Energy vs. Cost Efficiency Comparison
System Type | Energy Consumption (kWh/m3 N2) | Initial Cost | Operational Cost |
---|---|---|---|
PSA | 2-4 | Medium | Low |
Cryogenic Distillation | 5-8 | High | High |
Important: Optimizing system efficiency and regularly maintaining equipment can significantly lower both energy consumption and operational costs, improving overall profitability.
Maintenance Requirements: Keeping Your Liquid Nitrogen System Running Smoothly
Maintaining a liquid nitrogen generation system is crucial for ensuring its efficient operation and longevity. These systems rely on complex mechanical and electrical components, each of which requires regular monitoring and upkeep to function correctly. Without proper maintenance, performance can degrade, leading to potential system failures and increased operational costs. By adhering to a proactive maintenance schedule, operators can minimize downtime and ensure continuous, reliable nitrogen production.
Routine maintenance involves checking multiple system components, from compressors and heat exchangers to valves and pressure regulators. Identifying and addressing wear and tear early on can prevent costly repairs or even catastrophic breakdowns. Below are some essential maintenance tasks to help keep the system running optimally:
Key Maintenance Activities
- System Inspections: Conduct regular inspections of all moving parts, including compressors and pumps, to ensure they are functioning correctly.
- Lubrication: Apply the appropriate lubricants to mechanical components to reduce friction and prevent wear.
- Filter Replacement: Replace air and nitrogen filters regularly to avoid contamination and ensure proper gas purity.
- Check Pressure Levels: Monitor and adjust pressure settings to maintain optimal performance and avoid system overloads.
- Leak Detection: Use gas detectors to identify and repair any leaks in the system promptly.
Maintenance Checklist
- Check compressor oil levels and replace if necessary.
- Inspect and clean heat exchangers to remove dust and debris.
- Test safety valves and pressure relief devices.
- Ensure electrical connections are tight and free of corrosion.
- Inspect insulation for damage and repair as needed.
Important Considerations
Always consult the manufacturer's guidelines for maintenance intervals and specific procedures to avoid voiding warranties or damaging components.
Common Maintenance Issues
Issue | Potential Cause | Solution |
---|---|---|
Decreased Nitrogen Production | Clogged filters or worn-out compressors | Replace filters and service the compressor |
Pressure Imbalance | Faulty pressure regulators or leaks | Replace regulators and seal leaks |
Excessive Noise | Insufficient lubrication or damaged parts | Lubricate components and replace damaged parts |
Integrating a Liquid Nitrogen Production System into Existing Infrastructure
Integrating a liquid nitrogen generation system (LN2) into pre-existing infrastructure requires careful planning to ensure compatibility with current processes and systems. This involves assessing the capacity, location, and type of equipment required, as well as understanding the potential for upgrades in safety measures and energy consumption. A successful integration will maximize efficiency and minimize operational disruptions while maintaining safety standards and environmental compliance.
There are several key factors to consider when adding an LN2 system to existing operations. These include determining the required nitrogen production capacity, adapting the infrastructure to accommodate new equipment, and training personnel for safe operation. Below are the essential steps for successful integration.
Steps for Integration
- Assess Infrastructure Needs: Evaluate the existing system for space, power, and gas handling capabilities. Ensure there is sufficient room and utilities to support the liquid nitrogen equipment.
- Select Equipment: Choose an appropriate liquid nitrogen generator based on production volume and operational requirements. Pay attention to the specific models that best fit the site’s conditions and processes.
- Install and Calibrate: Install the system, ensuring proper connections to storage tanks and supply lines. Calibrate the system to meet operational demands and ensure efficiency.
- Ensure Safety Compliance: Integrate safety systems, including pressure relief valves, leak detection systems, and emergency shutoff mechanisms, in line with regulatory standards.
- Train Personnel: Provide training on safe operating procedures, system maintenance, and emergency protocols.
Key Considerations
Factor | Consideration |
---|---|
Energy Consumption | Ensure that the system's energy usage aligns with current capabilities and does not overload existing power supplies. |
System Integration | Ensure that the LN2 production unit is seamlessly connected to the existing gas distribution system and equipment without major modifications. |
Operational Continuity | Minimize downtime during installation and ensure that production schedules are not impacted by the integration process. |
Important: Conduct a detailed risk assessment before installation to avoid any disruptions and guarantee that safety standards are met throughout the process.
Safety Measures and Standards for Handling Cryogenic Nitrogen Systems
Handling liquid nitrogen (LN2) systems involves significant risks due to the extreme low temperatures and potential hazards associated with cryogenic substances. Strict safety protocols are essential to protect personnel and equipment from accidents or damage. Adhering to safety guidelines ensures the safe operation of LN2 generation systems, minimizes the risks of exposure, and prevents incidents such as frostbite or asphyxiation due to nitrogen displacement.
In order to manage the hazards associated with liquid nitrogen, operators must follow a series of structured protocols and regulations. These safety measures cover the use of proper protective equipment, correct storage procedures, and emergency responses to potential accidents. Ensuring that all staff members are properly trained in safety protocols is crucial to maintaining a safe working environment in any facility using LN2 systems.
Essential Safety Protocols
- Always wear insulated gloves, face shields, and safety goggles when handling liquid nitrogen.
- Ensure that ventilation systems are properly functioning to avoid nitrogen gas buildup in confined spaces.
- Store liquid nitrogen containers in well-ventilated areas to prevent the risk of asphyxiation.
- Never allow untrained personnel to operate or repair LN2 systems.
- Regularly inspect and maintain the cryogenic equipment for any signs of damage or malfunction.
Regulatory Guidelines
The handling of liquid nitrogen is governed by a set of safety regulations defined by international and local standards. These include guidelines set by bodies such as OSHA (Occupational Safety and Health Administration) and the CGA (Compressed Gas Association). Compliance with these regulations is mandatory in order to minimize risk and ensure workplace safety.
- OSHA Standard 1910.133: Requires appropriate eye and face protection when handling cryogenic substances.
- CGA P-1: Provides guidelines on the safe handling and storage of gases, including liquid nitrogen.
- ISO 21017: Establishes standards for cryogenic storage tanks, focusing on pressure relief devices and proper labeling.
Always ensure that your LN2 system is inspected and certified by a professional before initial use and regularly thereafter to comply with the safety standards.
Emergency Procedures
In the event of a leak or spill, the immediate response must follow a defined set of steps to prevent further escalation. Key emergency measures include:
Emergency Situation | Action |
---|---|
Spill of liquid nitrogen | Evacuate the area immediately, ensure proper ventilation, and do not attempt to clean the spill without proper protective gear. |
Asphyxiation Risk | Move individuals to a well-ventilated area immediately and seek medical attention. |
Frostbite | Apply lukewarm water to the affected area and seek medical attention promptly. |