Nitro Generator Working
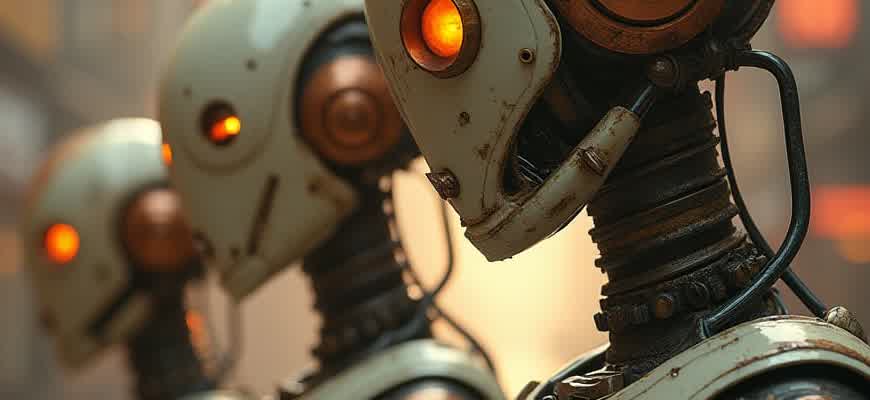
A Nitro generator is a device designed to produce nitrogen-based compounds through a chemical or physical process. These devices are widely used in various industries, from agriculture to electronics, to meet specific demands for nitrogen applications. The mechanism behind these generators often relies on the separation of nitrogen from air or the synthesis of nitrogen compounds from raw materials.
The basic working principle of a Nitro generator involves several stages:
- Air filtration and purification
- Nitrogen extraction via membrane technology or pressure swing adsorption (PSA)
- Compounding and mixing nitrogen with other gases or elements if needed
Here’s a breakdown of the different methods used in Nitro generators:
Method | Description | Application |
---|---|---|
Membrane Separation | Uses selective permeable membranes to separate nitrogen from other gases | Used in industries needing continuous nitrogen supply at low pressure |
Pressure Swing Adsorption (PSA) | Utilizes adsorbent materials to capture oxygen and other gases, leaving nitrogen | Common in high-purity nitrogen applications |
Important: The efficiency of a Nitro generator largely depends on the quality of raw materials and the specific technology employed. High-quality nitrogen production often requires precise control of operational parameters like pressure, temperature, and flow rate.
How Nitro Generator Increases Output Speed in High-Demand Environments
The use of nitro generators is becoming increasingly important in environments with high resource demands. By optimizing the way processing power is allocated, these devices enhance overall system performance. In such environments, where speed and efficiency are critical, they help minimize bottlenecks that would otherwise slow down operations. By incorporating nitro technology, companies can significantly improve throughput and responsiveness during peak times.
When deployed in high-demand situations, nitro generators work by providing additional computational resources that can handle bursts of activity. These systems are specifically designed to maintain a steady flow of operations, even under stress. By improving resource distribution and load balancing, nitro generators offer a clear advantage over traditional processing methods.
Key Advantages of Nitro Generators
- Improved Resource Allocation: Nitro generators dynamically distribute available processing power based on current needs, reducing the risk of overload.
- Reduced Latency: By enhancing data flow, nitro generators decrease delays, allowing faster response times in critical applications.
- Scalability: They can easily scale resources up or down in real-time, depending on demand fluctuations.
Operational Efficiency Boost
- On-Demand Power Surge: Nitro generators provide an on-the-fly power boost to handle peak loads without crashing or slowing down the system.
- Automated Adjustment: They automatically detect and adjust to the processing requirements, ensuring systems stay optimized without manual intervention.
- Reduced System Overload: By regulating usage and optimizing tasks, these generators prevent system failure during high-demand periods.
Nitro generators play a critical role in maintaining system stability by enhancing the speed and scalability of processing capabilities during peak operational periods.
Performance Monitoring
Performance is tracked and adjusted in real-time using specialized tools. A typical nitro generator setup includes:
Parameter | Before Nitro Generator | After Nitro Generator |
---|---|---|
Processing Speed | Low during peak hours | High with minimal interruptions |
System Load | Unpredictable and sometimes excessive | Balanced and optimized dynamically |
Response Time | Delayed under heavy usage | Fast and consistent during high demand |
Step-by-Step Guide to Setting Up Your Nitro Generator for Optimal Performance
Proper configuration of your Nitro Generator is crucial to ensure maximum output and efficiency. Follow this comprehensive guide to set up your device correctly and get the best results. This process includes hardware checks, software installation, and fine-tuning to achieve optimal performance.
Before diving into the setup, make sure you have all the necessary components: the Nitro Generator unit, power cables, any required software or firmware, and a stable internet connection if needed for updates. Having everything ready will streamline the process and minimize downtime.
1. Initial Setup
- Power Connection: Plug the generator into a reliable power source, ensuring it meets the voltage requirements specified in the manual.
- Hardware Check: Inspect cables, ports, and cooling systems to ensure everything is in working order.
- Install Software: Install the necessary software on your control device (e.g., computer or smartphone) that is compatible with the Nitro Generator.
2. Software Configuration
- Update Firmware: Ensure the latest firmware is installed. Visit the official website or use the device’s software to check for updates.
- Set Parameters: Configure key settings such as performance modes, temperature thresholds, and operational limits based on your needs.
- Test Connections: Verify that the software and hardware are properly synced by running a test operation.
3. Optimization
To get the most out of your Nitro Generator, fine-tune the settings to match your specific usage requirements. Monitor output levels and adjust the system accordingly.
Important: Always check for overheating issues and ensure the cooling system is running optimally to prevent damage.
4. Troubleshooting
If you experience issues during setup or operation, consult the troubleshooting section of the manual. Common problems include connectivity issues, software errors, or insufficient power supply.
5. Performance Monitoring
Metric | Ideal Range |
---|---|
Output Efficiency | 80%-90% |
Temperature | 30°C - 60°C |
Power Consumption | Depends on configuration |
Common Issues When Using Nitro Generator and How to Fix Them
Nitro generators are powerful tools that help users get access to premium features without paying, but they can sometimes present challenges. Below are some of the most common problems users face and how to resolve them effectively. Understanding these issues can save time and enhance the experience when using such tools.
While many of these problems are related to technical issues, others may stem from incorrect usage or outdated versions of the software. In this guide, we'll cover both and offer straightforward solutions to fix them.
1. Error Messages or Failed Generation
One of the most frequent issues with a Nitro generator is the inability to generate a valid code. This can be caused by various factors such as server issues, outdated software, or improper input. Below are some steps to resolve the issue:
- Ensure you are using the latest version of the generator.
- Check your internet connection to make sure it's stable.
- Try restarting the tool or your device to refresh the session.
Tip: Always verify if the generator's server is experiencing downtime by checking online forums or the developer's website.
2. Incompatible Browser or Device
Another common problem is incompatibility with the browser or device you are using. Certain Nitro generators may not work properly on all platforms. If you're facing this issue, follow the steps below:
- Switch to a different browser, preferably Chrome or Firefox, as they are typically the most compatible.
- Clear the browser cache and cookies to remove any conflicting data.
- Ensure your device meets the minimum system requirements specified by the generator tool.
3. Generating Invalid or Expired Codes
Sometimes the Nitro code generated by the tool may be invalid or expired. This is often due to restrictions from the service provider or a malfunction in the generation process. You can resolve this by:
Problem | Solution |
---|---|
Expired Code | Try regenerating a new code after a few hours or check for updates. |
Invalid Code | Ensure you entered the code correctly and try again. |
Note: Keep an eye on expiration dates when using generators to avoid entering outdated codes.
Maximizing Energy Efficiency: Tips for Operating Nitro Generator Safely
Operating a Nitro generator requires careful consideration of energy management to ensure efficiency and safety. By following specific protocols, you can reduce fuel consumption while prolonging the lifespan of the equipment. The following guidelines provide actionable steps for enhancing energy efficiency when using these generators in various applications.
It's essential to monitor and maintain the generator regularly, as small issues can escalate into significant inefficiencies. Implementing a set of operational best practices will help optimize performance while minimizing environmental impact and operational costs.
Best Practices for Energy Efficiency
- Regular Maintenance: Schedule frequent inspections to ensure that all components, such as fuel lines and filters, are functioning optimally.
- Appropriate Load Management: Operate the generator at or near its rated capacity to avoid underloading, which can lead to fuel waste.
- Efficient Fuel Use: Use high-quality fuel and consider fuel additives that reduce combustion inefficiencies.
- Monitoring Fuel Consumption: Keep track of fuel usage with precise instruments to detect early signs of inefficiency or malfunction.
Safety Measures
- Proper Ventilation: Ensure adequate ventilation around the generator to prevent overheating and maintain optimal combustion conditions.
- Temperature Monitoring: Regularly check the engine temperature to prevent damage from over-heating.
- Proper Installation: Follow installation guidelines to place the generator on stable ground and away from hazardous materials.
"Efficient operation isn't just about reducing fuel costs, but also about maintaining the long-term health of the generator. Proper maintenance practices directly contribute to both safety and energy efficiency."
Maintenance Checklist
Task | Frequency | Recommended Action |
---|---|---|
Oil Change | Every 50-100 hours | Replace with manufacturer-recommended oil to ensure smooth engine performance. |
Fuel Filter Check | Every 100 hours | Inspect and clean to prevent clogging and ensure fuel efficiency. |
Air Filter Inspection | Every 25 hours | Clean or replace to maintain optimal air-to-fuel ratio. |
How Nitro Generator Supports Scalable Production in Industry Applications
Nitrogen generators play a critical role in modern industrial processes, offering reliable and cost-effective solutions for the continuous supply of nitrogen. By generating nitrogen on-site, industries can significantly reduce operational costs and improve efficiency in production lines. This technology is particularly beneficial in environments where the demand for nitrogen fluctuates, such as in chemical manufacturing, food packaging, and electronics production.
The scalability of nitrogen generators is one of the primary reasons they are increasingly adopted in industries. These systems are designed to cater to both small-scale and large-scale operations, offering flexibility and adaptability for different production requirements. As production needs grow, nitrogen generators can be easily expanded to meet higher demands without requiring significant additional infrastructure or changes to existing processes.
Key Benefits of Nitro Generators for Scalable Production
- Cost Efficiency: On-site nitrogen generation eliminates the need for expensive deliveries and reduces long-term gas costs.
- Flexibility: These generators can be sized according to the specific requirements of the production process, with the ability to adjust output based on demand.
- Continuous Operation: Nitro generators provide a constant supply of nitrogen, ensuring uninterrupted production and reducing the risk of downtime.
How Scalability Works in Industrial Applications
- Modular Design: Nitro generators often have modular components that can be added or removed as necessary. This flexibility allows industries to scale nitrogen production without overhauling the system.
- Advanced Control Systems: Modern systems include intelligent control mechanisms that adjust nitrogen output according to real-time consumption, ensuring efficient use of resources.
- Energy Efficiency: By optimizing energy usage, these systems maintain high efficiency even as production demands increase.
"Nitrogen generators provide industries with a reliable, scalable solution that supports growth and maintains optimal production conditions."
Feature | Benefit |
---|---|
Modular Design | Allows easy scaling without major infrastructure changes. |
Continuous Supply | Ensures that nitrogen is always available for production processes. |
Energy Optimization | Reduces energy consumption while maintaining production efficiency. |
Comparing Nitro Generator with Alternative Energy Solutions
Energy generation technologies are diverse, and each approach offers unique advantages and challenges. One of the emerging energy solutions is the Nitro Generator, which has gained attention due to its efficiency and lower environmental impact compared to traditional energy sources. However, when compared to alternative energy solutions such as solar, wind, and hydro power, the Nitro Generator presents a different set of trade-offs that are essential to consider for specific applications.
This comparison explores the Nitro Generator in relation to other renewable energy options. While all these technologies aim to reduce reliance on fossil fuels, the way they generate and store energy, as well as their scalability and environmental effects, differ significantly.
Advantages and Drawbacks of Nitro Generator
- Efficiency: Nitro generators are highly efficient, especially in environments where renewable sources like solar or wind might not be reliable.
- Flexibility: Nitro generators can be used in a variety of settings, from industrial to residential applications, unlike some energy solutions which are location-dependent.
- Environmental Impact: Though less impactful than fossil fuels, Nitro generators still produce some emissions, which could be a concern for areas aiming for zero emissions.
Comparison Table: Nitro Generator vs Alternative Energy Sources
Feature | Nitro Generator | Solar Power | Wind Power | Hydro Power |
---|---|---|---|---|
Energy Efficiency | High | Medium | Medium | High |
Environmental Impact | Medium | Low | Low | Low |
Installation Cost | Medium | High | Medium | High |
Scalability | High | Medium | Medium | Low |
Important Considerations
The Nitro Generator offers a versatile and efficient solution, but it cannot fully replace renewable sources like solar and wind in terms of environmental impact. For a sustainable future, a combination of these technologies may be the most effective approach.
Alternative Energy Solutions
- Solar Power: Relies on sunlight, making it an excellent option for sunny regions, but it is not ideal for areas with limited sunlight.
- Wind Power: Harnesses wind energy and is highly effective in windy regions, although it requires significant space and infrastructure.
- Hydro Power: Generates electricity from water flow, providing a consistent energy source, but large-scale hydro projects can disrupt ecosystems.
Maintenance Checklist for Extending the Life of Your Nitro Generator
Proper maintenance is key to ensuring the longevity and optimal performance of your Nitro Generator. Regular servicing not only helps in preventing unexpected breakdowns but also improves efficiency. By following a strict maintenance schedule, you can avoid costly repairs and reduce downtime. This checklist covers essential steps that should be followed to keep your generator running smoothly over time.
Maintaining a Nitro Generator involves routine inspections, cleaning, and part replacements. It is important to create a system for regular checks, ensuring that all components are functioning as intended. Here is a detailed list of maintenance tasks that will help extend the life of your machine.
Key Maintenance Tasks
- Inspect the fuel system: Ensure fuel filters are clean and free from contaminants. Check for leaks and replace fuel lines if necessary.
- Air Filter Replacement: Regularly replace or clean the air filter to prevent clogging and maintain air circulation.
- Coolant Levels: Check coolant levels and top up if needed to prevent overheating of the generator.
- Electrical Connections: Tighten any loose electrical connections and check for signs of wear or corrosion.
Scheduled Servicing
- Monthly: Inspect the air filter and clean or replace as necessary. Check fuel levels and look for potential leaks.
- Quarterly: Test the system for functionality and check the battery charge level. Inspect all hoses for wear.
- Annually: Perform a full engine inspection, check spark plugs, and test exhaust systems.
Maintenance Table
Task | Frequency | Action |
---|---|---|
Air Filter | Monthly | Clean or Replace |
Fuel Filter | Every 6 months | Replace |
Coolant Check | Quarterly | Top-up if necessary |
Electrical System | Annually | Inspect and Tighten |
Important: Regular maintenance can prevent system failures and reduce the need for costly repairs. Always consult your generator's manual for specific maintenance guidelines.
Real-World Case Studies: How Companies Benefit from Using Nitro Generator
Several businesses across various industries have harnessed the power of nitrogen generation technology to optimize their operations. This innovative solution provides on-demand nitrogen, offering enhanced safety, cost savings, and efficiency. By transitioning from traditional nitrogen delivery methods to in-house generation, companies are improving their bottom line while increasing reliability and reducing environmental impact.
Below are real-world examples showcasing the tangible benefits of integrating nitrogen generators into company operations, illustrating both economic and operational improvements.
Case Study 1: Food Packaging Industry
A leading food packaging company integrated a nitrogen generator to enhance the shelf life of packaged goods. Prior to this, the company relied on nitrogen delivery services, which were costly and inconsistent. With their own nitrogen generator in place, they were able to:
- Reduce nitrogen-related costs by 30% annually
- Eliminate delivery delays and ensure consistent nitrogen purity
- Minimize environmental impact by reducing CO2 emissions from delivery trucks
"By using a nitrogen generator, we not only reduced costs but also improved our packaging process, ensuring the best quality for our customers," said the operations manager of the company.
Case Study 2: Automotive Manufacturing
In an automotive manufacturing plant, a nitrogen generator was implemented to improve the quality of welded parts. Nitrogen is used in the welding process to prevent oxidation, which can compromise the strength and appearance of welded seams. Benefits included:
- Improved weld quality and reduced defects
- Lowered operational costs related to external nitrogen supply
- Enhanced production efficiency, reducing downtime during supply chain disruptions
Benefit | Impact |
---|---|
Cost Reduction | Saved 25% on nitrogen supply expenses |
Operational Efficiency | Reduced downtime by 15% |