Nitro Beer Keg System
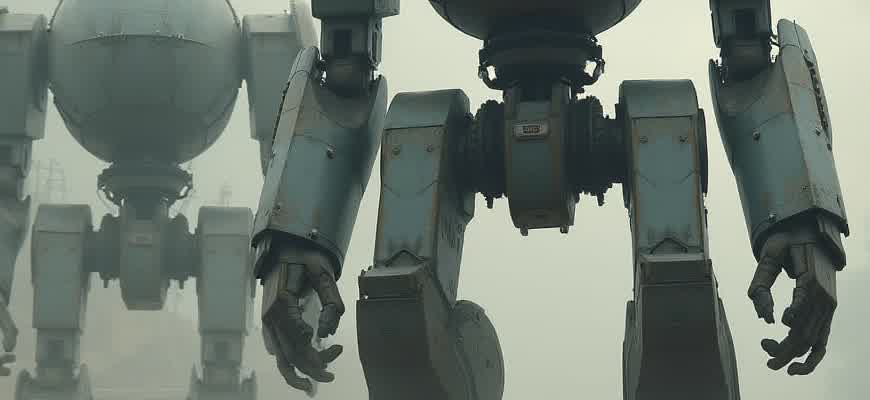
The nitrogen beer keg system offers a unique method of serving draft beer, enhancing the overall drinking experience. Unlike traditional CO2-based systems, nitrogen-infused systems provide a smoother, creamier pour with a richer texture, especially suited for stouts and porters. This system works by substituting carbon dioxide with nitrogen, which is less soluble in liquid, creating smaller bubbles that contribute to a velvety mouthfeel.
Key Components:
- Nitrogen Cylinder: Provides the necessary gas for pressurizing the keg.
- Beer Keg: Holds the beer, ensuring it is properly chilled and carbonated.
- Regulator: Controls the pressure, ensuring the correct nitrogen level is maintained.
- Tap System: Dispenses the beer from the keg to the glass with consistent flow.
Advantages of Nitro Beer Systems:
- Smoother Texture: Creates a creamier, softer mouthfeel that enhances flavor profiles.
- Improved Pour Quality: Produces a rich, dense head that enhances aroma and visual appeal.
- Stable Pressure: Ensures consistent pouring without fluctuations, maintaining optimal taste.
Important Note: Nitro beer systems are ideal for beers that benefit from a rich, smooth head, such as stouts, porters, and some IPAs. It’s not suitable for all types of beer.
System Comparison:
System Type | Gas Used | Ideal Beer Types |
---|---|---|
CO2 System | Carbon Dioxide | Ales, Lagers, Wheat Beers |
Nitrogen System | Nitrogen | Stouts, Porters, Creamy Beers |
Choosing the Correct Nitrogen Gas Pressure for Perfect Beer Dispensing
When using a nitrogen system for dispensing beer, selecting the right gas pressure is crucial for achieving a smooth, creamy pour with the perfect head. Nitrogen pressure directly impacts the beer’s texture, carbonation, and overall presentation. Too high or too low a pressure can result in an overly foamy or flat pour, which compromises the drinking experience. Achieving balance is essential for optimal results, and this balance varies depending on the beer style and the equipment used.
Understanding the relationship between nitrogen pressure and beer dispensing can help ensure consistent results. Different beers, such as stouts and lagers, require different pressures to achieve the desired pour. The pressure setting should take into account factors like the length and diameter of the beer line, the keg’s temperature, and the CO2/Nitrogen mixture. Below is a guide on how to determine the optimal nitrogen pressure for various situations.
Key Factors to Consider for Nitrogen Gas Pressure
- Beer Type: Different styles of beer require varying amounts of nitrogen pressure for the ideal pour. For example, stouts typically need higher pressure to achieve the rich, creamy texture associated with this beer type.
- Beer Line Length and Diameter: The longer and narrower the beer line, the more resistance it creates, which affects the required pressure to maintain a smooth flow.
- Temperature: Colder temperatures require lower pressures for proper dispensing, while warmer temperatures often need higher pressures to prevent the beer from flowing too slowly or being over-carbonated.
Recommended Nitrogen Gas Pressures for Common Beer Styles
Beer Type | Recommended Pressure (PSI) |
---|---|
Stout | 30-35 PSI |
Pale Ale | 18-22 PSI |
Lager | 12-15 PSI |
When adjusting nitrogen pressure, always ensure that you do not exceed the recommended PSI for each beer type, as this can lead to over-carbonation and poor pouring results.
Adjusting Nitrogen Pressure for the Best Pour
- Start with the recommended pressure based on the beer style and keg temperature.
- Monitor the pour; if the beer is foamy or too slow, adjust the pressure incrementally.
- Consider the beer line resistance and tweak the pressure accordingly to maintain a steady flow.
- Test the pour again after adjustments, keeping track of the pressure settings for future use.
Maintenance Tips to Extend the Life of Your Nitro Beer System
Proper maintenance is essential to ensure the longevity and efficiency of your Nitro Beer System. Regular care not only improves the quality of the beer served but also minimizes the risk of costly repairs. The following tips outline key practices for keeping your system in optimal working condition.
By following these steps, you can maintain consistent beer quality and extend the lifespan of your equipment. With minimal effort, you’ll ensure your system remains free from issues such as carbonation problems, leaks, or poor flow rates.
Key Maintenance Tips
- Clean Lines Regularly: Beer lines can accumulate residue that affects both flavor and system performance. Clean the lines every two weeks to prevent build-up.
- Replace Seals and O-Rings: Inspect seals and o-rings for wear and replace them as necessary. Leaking gases can lead to inefficiency.
- Check Pressure Regularly: Monitor the pressure to ensure it stays within the recommended range (usually between 30-40 PSI). Incorrect pressure can affect pouring and foam quality.
Steps to Clean and Maintain the System
- Disconnect the keg and relieve the pressure from the system.
- Remove all beer lines, faucets, and fittings for cleaning.
- Soak parts in a cleaning solution designed for beer systems.
- Rinse thoroughly with clean water and let the parts dry completely.
- Reassemble the system, ensuring all components are securely tightened.
Regular cleaning and inspection are the key to avoiding major maintenance issues. Neglecting these steps can lead to poor beer quality and costly repairs.
Common Issues and Solutions
Issue | Solution |
---|---|
Low or inconsistent pressure | Check regulator, replace faulty seals, and verify nitrogen tank levels. |
Flat beer | Adjust nitrogen levels and ensure pressure settings are accurate. |
Foamy beer | Check for leaks in the system and verify proper line cleaning. |
Common Issues with Nitro Beer Systems and How to Fix Them
Nitro beer systems are designed to deliver a smooth, creamy texture to beers like stouts, but they can experience several issues that impact performance and taste. These systems require proper maintenance and troubleshooting to ensure optimal functionality. Below are some common problems faced by users and effective solutions for each.
Understanding the potential issues with your Nitro beer system is key to maintaining the quality of your drinks. By addressing these problems early, you can avoid wasting time, money, and effort, and keep your system running smoothly for a better beer experience.
1. Low or Inconsistent Nitrogen Flow
One of the most common issues with Nitro systems is low or fluctuating nitrogen flow, which leads to poorly poured beer with insufficient creaminess. The nitrogen gas flow needs to be precise to achieve the signature smooth texture.
- Clogged Regulator or Lines: Over time, nitrogen lines or regulators can become clogged with beer residue or other debris, restricting the flow.
- Incorrect Gas Pressure: If the gas pressure is set too low or too high, it can result in an improper pour and inconsistent texture.
- Faulty Nitrogen Tank: A low or empty nitrogen tank may lead to reduced pressure, affecting the flow.
Fixes:
- Check the nitrogen tank’s pressure gauge and refill or replace the tank if necessary.
- Inspect and clean the regulator and lines regularly to ensure no blockages.
- Adjust the nitrogen gas pressure to the recommended level (typically 30-40 PSI for Nitro systems).
Always ensure the tank pressure is adequate before troubleshooting the lines or regulator.
2. Flat Beer or Poor Foam Quality
Flat beer with minimal foam is another sign that something is wrong with the Nitro system. This issue can stem from both improper nitrogen levels and temperature issues.
- Improper Gas-to-Liquid Ratio: If the nitrogen is not properly mixed with the beer, the result can be a lack of foam.
- Temperature Imbalance: Nitro systems require beers to be stored at specific temperatures, usually around 38°F (3°C). Temperatures that are too high or low can lead to poor pour quality.
- Over-carbonation: Excessive carbonation can also affect the foam structure, leading to a lack of the characteristic Nitro creaminess.
Fixes:
- Ensure that the beer is at the optimal serving temperature (38°F or 3°C).
- Check the gas-to-liquid ratio and ensure nitrogen is being used at the proper levels.
- Regulate the CO2 levels, if any, to avoid over-carbonating the beer.
Consistent beer temperature is critical for maintaining the right texture and foam quality.
3. Leaking Nitrogen Lines
Leaks in the nitrogen lines can cause pressure drops, which lead to inconsistent pouring and a lack of proper foam. A small leak in the system can significantly impact performance.
- Loose Fittings: Connections that are not securely tightened can result in air leaks.
- Damaged Hoses: Over time, the hoses used in Nitro systems can wear out, crack, or develop holes, leading to leaks.
Fixes:
- Inspect the hoses and fittings for signs of wear and tear. Replace any damaged parts immediately.
- Tighten all connections to ensure there are no gaps where gas can escape.
- Check for leaks using a soapy water solution–bubbles will form at the point of leakage.
Issue | Solution |
---|---|
Low Nitrogen Flow | Refill tank, clean regulator and lines, adjust pressure |
Flat Beer | Ensure proper gas-to-liquid ratio, regulate temperature |
Leaking Nitrogen Lines | Inspect hoses, replace damaged parts, tighten fittings |
Understanding the Costs and ROI of a Nitro Beer System
When considering the installation of a nitrogen beer dispensing system, one must evaluate both the initial investment and the ongoing operational costs. The system itself requires a variety of components, including nitrogen tanks, specialized kegs, regulators, and unique taps. These factors contribute to a larger initial outlay compared to a traditional CO2 system. However, the distinctive smooth pour and rich texture that nitrogen creates can attract a premium price for your beer, potentially increasing revenue in the long term.
Calculating the return on investment (ROI) involves more than just considering upfront expenses. Operational savings, such as reduced waste and enhanced product shelf life, should also be factored into the equation. Additionally, the unique appeal of nitro beer may lead to greater customer loyalty and increased sales volume. In this analysis, it's crucial to weigh both direct costs and the intangible benefits that a nitro system brings to your establishment.
Initial Costs Breakdown
- System Components: Nitro tanks, regulators, and special taps are essential for the setup.
- Installation: Professional installation services might be required to ensure everything is set up correctly.
- Beer Kegs: Nitro beer requires kegs designed for nitrogen, which can be pricier than standard kegs.
Ongoing Costs
- Gas refills: Nitrogen tanks need regular refills, which may become a recurring cost.
- Maintenance: Routine checks and maintenance of the system to prevent issues such as leaks or blockages.
- Energy costs: Nitro systems may require slightly higher energy consumption for the dispensing equipment.
ROI Considerations
Benefit | Impact on ROI |
---|---|
Premium Pricing | Increased profit margin per pint due to higher perceived value of nitro beer. |
Customer Appeal | Attracts customers seeking a unique drinking experience, boosting sales volume. |
Reduced Waste | Less spillage and waste due to the smoother pour, contributing to overall savings. |
Important: While the initial investment can be high, the potential for increased revenue and customer loyalty makes a nitro system an attractive option for establishments looking to stand out in the competitive craft beer market.